Hybrid Dual-Clutch Transmission
Basic Transmission Technologies
The transmission in a vehicle is a major component that transmits engine power and speed to the wheels according to the driver's demand. Hence the operating efficiency of the transmission or its ability to transmit an appropriate amount of power with minimum losses has always been a design challenge.
The key drivers for automotive transmission development are fuel Economy, emissions and cost. Table 1 shows the various pros and cons of an automatic and manual transmission.
Advances in electronics and the need for compliance with environmental and legislative requirements have given directive to variants of automatic transmissions such as Automated Manual Transmission (AMT), Dual Clutch Transmission (DCT), and Continuously Variable Transmission (CVT). Closer look at the global market shows that depending on the market (North America or Europe or Japan) each of these technologies has their own penetration levels. However, DCT with its refinement, efficiency, low cost and driving satisfaction is the probable winner.
Since DCT delivers very high comfort levels along with improved transmission efficiency, it is a promising and exciting alternative for drivers of automatic transmissions who want to keep the fuel costs low and yet have the comforts of automatic transmissions.
Table 1. Qualitative Comparison of Automatic and Manual Transmission | ||
Automatic Transmission | Manual Transmission | |
Cost | Expensive | Lower |
Efficiency | Moderate | High |
Ease of Use | Easy | Hard |
Comfort | Good | Poor |
DCT’s are well suited for higher torque diesel engines and high revolving gas engines alike. The easy software tunability characteristics of DCT make them a favorite amongst the powertrain engineers around the world. Due to these attributes, leading powertrain companies have intensified efforts for its hybridization. The expected reductions of up to 30% in emissions for the hybrid dual clutch transmission as compared to the conventional drivetrain. Some of the major drivers for DCT hybridization include:
• Flexible and software tunable launch strategies.
• Gear ratio flexibility being the same as that of manual lay shaft transmissions allowing greater compatibility to any engine characteristic.
What is a Dual Clutch Transmission (DCT) System?
In a DCT system, the two clutches are connected to two separate sets of gears. The odd gear set is connected to one of the clutches and the even gear set to the other clutch. It is necessary to preselect the gears to realize the benefits of the DCT system. Accordingly, the off-going clutch is released simultaneously as the on-coming clutch is engaged. This gives the uninterrupted torque supply to the driveline during the shifting process. This pre-selection of gears can be implemented using complicated controllers such as fuzzy logic or simple ones such as selections based on the next anticipated vehicle speed.
Difference between Hybrid Dual Clutch Transmission (HDTC) and Dual Clutch Transmission (DCT)
An HDCT incorporates the features of a DCT but is specifically designed to work in conjunction with a hybrid powertrain. In addition to the internal combustion engine, an HDCT integrates an electric motor and a hybrid power system, such as a battery pack. This allows for the seamless blending of power from both the internal combustion engine and the electric motor.
In a hybrid system, the motor supports the engine, improving driving performance and fuel consumption by regenerating with the motor and storing energy in the battery, using this to drive like an EV and for accelerating. The one-motor two-clutch hybrid system can separate the engine from the drivetrain as necessary. It can utilize the engine and motor as power sources, from running just on the motor to using both motor and engine for full acceleration, achieving a more efficient drive as per the situation. During regeneration and electric-mode driving, the engine is completely disconnected from the drive-train, resulting in zero loss from engine friction.
Figure 1. DCT (A) Dana P2.5 (B) Magna 7HDT300 | 7HDT400
Key differences and features of an HDCT compared to a standalone DCT
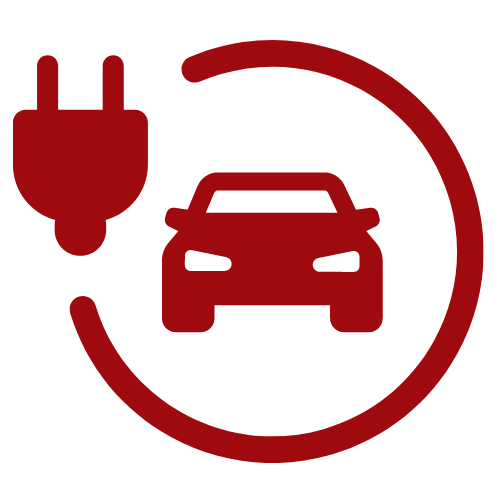
Hybrid Power Integration
HDCT is part of a hybrid powertrain wherein it can manage the distribution of power between the internal combustion engine and the IPM electric motor. This integration enables electric-only driving, hybrid driving modes, and regenerative braking.
.png)
Energy Recovery
HDCT, being part of a hybrid system, can take advantage of regenerative braking to recover and store energy in the battery packs. This contributes to overall energy efficiency and fuel savings.
.png)
Electric-Only Mode
In certain driving conditions, an HDCT-equipped hybrid vehicle can operate solely on electric power, utilizing the electric motor without engaging the internal combustion engine. EV Propulsion System
.png)
Enhanced Fuel Efficiency
The hybridization allows for optimized power conversion delivery based on driving conditions, contributing to improved fuel efficiency and reduced emissions.
Thermal Interface Materials Application on HCDT Components
Operating Temperature, oC | Materials Use | |
Clutch Components | 150 - 200 | Thermal Grease Phase Change Materials |
Power Electronics (Inverter and Motor Controller) | (-40) - 100 | Phase Change Materials |
Power Electronics ( Semiconductor Devices) ex. IGBTS, MOSFETS | (-40) - 150 | Phase Change Materials PTM6000HV (Optimized for IGBT printing) |
Transmission Fluid Temperature Control | 70 - 100 | Phase Change Materials Thermal Gap Pads Thermal Grease |
Electric Motor | Generator | (-40) - 100 | Phase Change Materials Thermal Gap Pads Thermal Grease |