Heat Spreaders
Heat spreaders, often referred to as 'lids,' play a crucial role in dissipating heat from chips and components, ensuring optimal performance and reliability in various applications. These versatile components are designed to address the thermal challenges of moderate to high-performance environments, including high-end desktop and server CPUs, as well as memory and power devices like inverters.
We offer a comprehensive range of advanced stamping technologies tailored to meet your specific needs. Whether it's coining, high-speed progressive stamping, or multi-stage, high-tonnage transfer die stamping, we have the expertise to manufacture intricate geometries for Copper Integrated Heat Spreaders. Beyond heat spreaders, our precision-stamped products exhibit the same level of excellence and reliability.
With continuous Ni plating lines and MIL standard compliant Au spot plating, we ensure a consistent and impeccable surface finish that meets the most demanding standards. Our dedicated team of skilled professionals ensures top-notch production, backed by a robust quality management system adhering to ISO 9001 certification.
HW-HSPS | Heat Spreader - Progressive Stamping
- Nickel plated / Au Spot
- Small and medium form factors
- Simplified parts - Lower volumes
- 4 - 6 weeks
HW-HSTD | Heat Spreader - Transfer die stamping
- Nickel plated / Au Spot
- Wide range form factor
- Complex designs - Higher volumes
- 4 - 6 weeks
COOLINQ SG-25 | Graphite heat spreader
- 25um Graphite
- Light weight and flexible
- Excellent thermal conductivity
- 6 - 8 weeks
COOLINQ SG-90 | Graphite Heat Spreader
- 90um Graphite
- Light weight and flexible
- Excellent thermal conductivity
- 6 - 8 weeks
Product Selector Guide
Capability / Tolerances | COOLINQ SG-25 | COOLINQ SG-90 |
Thickness (mm) | 0.025 | 0.090 |
Density | 2.1 | 1.5 |
Specific Heat | 0.94 | - |
X,Y Thermal Conductivity (W/mK) | 1500 | 400 - 450 |
Z Thermal Conductivity (W/mK) | 10 | 10 - 20 |
Operating Conditions | -40 to 400 | -40 to 400 |
Capability / Tolerances | HW-HSPS | HW-HSTD |
Max size (mm) | 46.5 X 50 | 130 X 130 |
OD & ID (mm) | ±0.05 | ±0.05 |
Radii (mm) | >0.30 | >0.30 |
Seal band with (mm) | ±0.050 | ±0.040 |
Thickness (mm) | 0.5 - 3.5 | 0.5-3.5 |
Topside & Cavity flatness by part area (40mm2) in (mm) | 0.04 | 0.04 |
Topside & Cavity flatness by part area (50mm2) in (mm) | 0.07 | 0.07 |
Topside & Cavity flatness by part area (60mm2) in (mm) | - | 0.12 |
Topside & Cavity flatness by part area (70mm2) in (mm) | - | 0.20 |
Flange Width (mm) | ±0.10 | ±0.10 |
Cavity Depth (mm) | ±0.05 | ±0.05 |
Surface Profile (mm) | ±0.003 | ±0.003 |
Pedestal Depth (mm) | - | ±0.050 |
Pedestal X,Y (mm) | - | ±0.050 |
Frequently Asked Questions
What are Heat Spreaders?
Heat spreaders, commonly referred to as 'lids', are crucial components used to dissipate heat away from chips, especially in high-performance applications such as high-end desktop and server CPUs. They are also employed in other applications like memory and power devices, such as inverters. These spreaders are designed using a variety of stamping technologies to achieve efficient heat dissipation and are known for their reliability and consistency in surface finish.
What's the Difference between Progressive and Transfer Stamping?
Heat spreaders can be manufactured using different processes, including progressive and transfer stamping. Progressive stamping is suitable for relatively small to medium-sized, simple designs. On the other hand, transfer stamping is ideal for complex and large designs. The choice between these processes depends on the size and complexity of the heat spreader.
What about Complex Geometries?
Heat spreaders can feature complex geometries achieved through transfer and progressive stamping techniques. These techniques allow for the creation of intricate features such as multiple cavities, wings, flanges, etc. In some cases, a hybrid approach combining stamping and machining is employed to achieve even more intricate designs. The materials used include Cu-based, Al-based, and stainless-steel materials, with tight tolerances for critical parameters ensuring consistent quality.
What Plating Processes are Used?
Heat spreaders often undergo various plating processes to achieve desired surface finishes. Nickel (Ni) and Gold (Au) are commonly used for plating. Continuous plating lines ensure repeatability and consistency in high-volume manufacturing. Surface finish control parameters include brightness, gloss, roughness, thicknesses, etc. These plating processes play a crucial role in enhancing the performance and longevity of heat spreaders.
How to Properly Store and Maintain Heat Spreaders?
Proper storage of heat spreaders is essential for maintaining their quality. Storage below recommended temperatures could lead to issues like crystallization or freeze-thaw voids, affecting dispensing characteristics. Conversely, storage above recommended temperatures may decrease shelf life. Following the manufacturer's guidelines for storage and usage, along with ensuring suitable equipment and conditions, helps maximize the performance of heat spreaders.
Are Heat Spreaders Compatible with Different Materials?
Heat spreaders are designed to work with a range of materials, including various metals and alloys. Compatibility with materials like gold and silver is considered, with considerations for bonding difficulties and reliability. While the bonding process might differ for different materials, manufacturers aim to offer heat spreaders that are versatile and effective across various applications.
What are the Benefits of Using Heat Spreaders?
Heat spreaders play a critical role in maintaining the optimal operating temperature of chips and components. By efficiently dissipating heat, they enhance the performance and longevity of electronic devices. Heat spreaders also provide better thermal management, which is essential for high-performance applications. Their ability to accommodate complex geometries and use in various applications makes them an essential component in modern electronics.
How to Choose the Right Manufacturing Process for Your Heat Spreaders?
The choice between progressive and transfer stamping depends on the specific requirements of your heat spreaders. Progressive stamping is suitable for simpler designs and smaller volumes, while transfer stamping is preferable for larger, more complex designs and higher volumes. Evaluating the size, complexity, and intended use of your heat spreaders will guide you in selecting the most appropriate manufacturing process. The Heat Spreader Application Profile Analysis allows customers to share their requirements and lets CAPLINQ match the best-suiting heat spreader to this demand.
Is Gold Plating available on all base materials?
Currently due to limited assembly, gold plating is only available on copper base material spreader
Learn More
Heat spreader designs are custom
While they might look similar and easy to mass produce, Heat spreaders always have some design or I.P behind them that makes them unique. All parts are custom. We may have designed similar parts for different customers, but the customers own the IP and we cannot share that with other customers.
We also do not specify the requirements for the Heat Spreader. That is generally done by the thermal engineers by the customer. What we do have, is expertise in the manufacturing of these parts to meet very tight tolerances for optimal thermal performance as specified by the customer.
Tooling costs are dependent on the detail/design/tolerances required for each part. They may change slightly from part to part – but we utilize a third party to fabricate the die tooling required to stamp each part. Tooling costs are passthrough prices. Tooling can be charged either as an NRE (non refundable engineering) fee or can be amortized on the spreader price.
Comparing Metal vs. Graphite Heat Spreaders
Property | Metal Heat Spreaders | Graphite Heat Spreaders |
---|---|---|
Thermal Conductivity (W/mK) | High | Exceptionally High (XY) |
Weight | Heavier | Lightweight |
Mechanical Flexibility | Rigid | Flexible |
Anisotropy | Isotropic (Uniform) | Highly Anisotropic (XY) |
Manufacturing Process | Machining and Forming | Chemical Vapor Deposition |
Electrical Conductivity | Conductive | Semiconductive |
Cost | Moderate to High | Moderate |
Metallic Heat Spreaders
Progressive Stamping vs. Transfer Die
Heat spreaders are unsung heroes in the world of electronics, quietly conducting thermal energy away from vital components to ensure consistent performance and unwavering reliability. These components play a critical role in preventing overheating and maintaining the delicate balance required for optimal device operation.
In the realm of manufacturing heat spreaders, two prominent techniques take the spotlight: progressive stamping and transfer die. Manufacturers select the most fitting method based on the intricate demands of the application. Progressive stamping method follows a systematic and linear approach. It involves a step-by-step process where each station contributes to shaping the raw material into the final spreader design. This technique shines brightest when crafting heat spreaders with simpler geometries and in low-volume production scenarios.
On the other hand, the transfer die method embraces complexity. A mechanical transfer system shuttles the material between different stations, allowing intricate designs to gradually emerge. This approach thrives when intricate detailing and design complexity is paramount. It is better suited for higher volume productions and it excels in bringing to life unique designs.
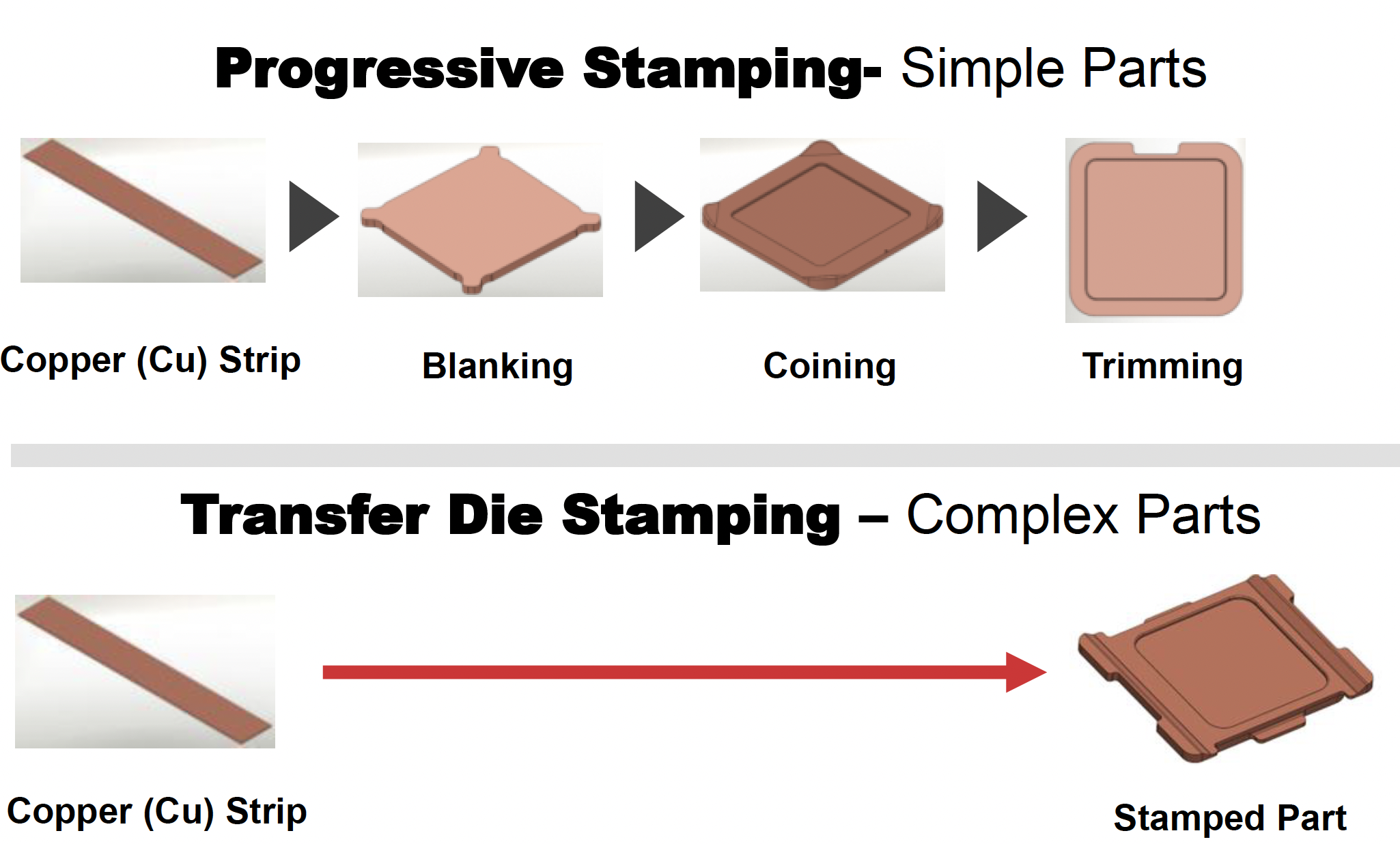
Differences between Progressive Stamping and Transfer Die
Aspect | Progressive Stamping | Transfer Die |
---|---|---|
Method | Individual stations perform operations on a metal sheet in a linear sequence. | Metal sheet is moved between stations using a mechanical transfer system. |
Process Complexity | Well-suited for simple geometries | Ideal for complex designs |
Design Flexibility | Limited flexibility for intricate shapes and features. | Offers greater flexibility for unique and complex designs. |
Tooling Cost | Lower initial tooling cost. | Higher initial tooling cost due to complex transfer systems. |
Lead Time | Shorter lead time for production. | Longer lead time due to setup and optimization. |
Production Volume | Best for low-volume production. | Suitable for medium to high production volumes. |
Both progressive stamping and transfer die methods offer unique benefits, and the choice between them depends on factors such as production volume, design complexity, and cost considerations.
Progressive Stamping:
This method involves a series of individual stations that perform various operations on the metal sheet, such as cutting, bending, and shaping. It is well-suited for low-volume production and relatively simple geometries. Progressive stamping offers excellent precision and efficiency, making it a popular choice for simple, batch production. Smaller form size. Generally speaking, max lid thickness can be up to 3.1mm and max cavity depth can be 1mm.
Transfer Die:
Transfer die method is ideal for complex designs and a wide range of production volumes. In this process, the metal sheet is moved from station to station using a mechanical transfer system. Transfer die allows for intricate shapes and features that may be challenging to achieve with progressive stamping. It offers greater flexibility and customization options for unique heat spreader designs. Larger form size.
Choosing the Right Method
The decision between progressive stamping and transfer die depends on the specific requirements of your project. Consider factors such as production volume, design complexity, lead time, and budget constraints. Collaborating with experienced manufacturers like us, can help you determine the most suitable method for your heat spreader manufacturing needs. Please contact us with your design requirements.
Graphite Heat Spreaders
Graphite heat spreaders have emerged as versatile solutions for effective thermal management in various electronic applications. Their exceptional thermal conductivity properties make them invaluable in dissipating heat efficiently. Let's delve into their applications, manufacturing methods, and how they compare with traditional metal heat spreaders.
Applications
Graphite heat spreaders find applications across diverse industries and technologies:
- Electronics: They are widely used in smartphones, laptops, and tablets to transfer heat away from processors and other heat-sensitive components. This prevents overheating and ensures optimal device performance.
LED Lighting: Graphite sheets help maintain consistent temperatures in LED modules, prolonging the lifespan and efficiency of LED lights.
Automotive: In electric and hybrid vehicles, graphite heat spreaders contribute to battery cooling, ensuring safe and efficient operation.
Aerospace: These sheets play a crucial role in avionics, ensuring electronics remain within safe temperature limits during flights.
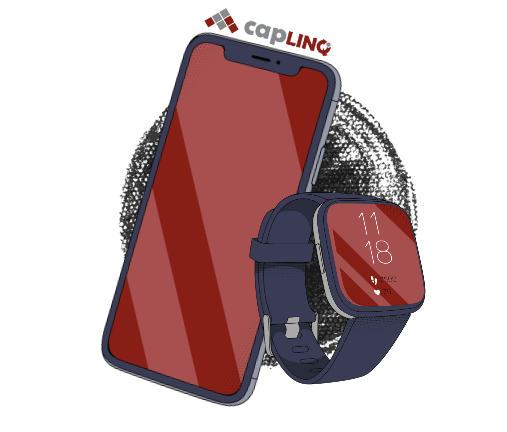
Graphite heat spreaders excel in scenarios where high XY thermal conductivity, lightweight properties, and flexibility are essential. Metals on the other hand, offer uniform thermal conductivity but may be heavier and less flexible.
Graphite's unique properties make it an ideal choice for applications demanding exceptional heat-spreading capabilities while minimizing weight and mechanical constraints. Graphite heat spreaders have revolutionized thermal management in electronics and various industries. Their exceptional XY thermal conductivity, lightweight nature, and flexibility make them a valuable addition to modern thermal solutions, ensuring electronic devices run efficiently and safely.