Carbon Dioxide Electrolyzers
Closing the Carbon Loop through CO2 Electrolysis
CO2 emissions continue to increase as several industries continue to depend on fossil fuels. The atmospheric CO2 concentration has almost doubled after the Industrial Revolution (Current: >400 ppm, before the Industrial Revolution: 280 ppm). This increase translated to a global temperature rise of approximately 2 °C. To reduce the adverse effects of global warming to human life and property, the Intergovernmental Panel on Climate Change (IPCC) limits greenhouse gas emissions in such a way that the global temperature rise will decrease to 1.5 °C.
One promising way to decarbonize industries is to couple the heavy industrial processes with renewable energy. This route necessitates the use of efficient carbon capture and utilization strategies to sequester CO2 from the atmosphere or any other gaseous streams and then convert it to high-value chemicals and fuels. The most commonly used carbon capture and utilization techniques involve the use of thermal catalysts, electrolysis, and biotechnology. Among these CO2 conversion technologies, CO2 electrolysis proves to be low cost, scalable, and sustainable. It enables the direct storage of renewable electricity in a convenient and high-energy-density form. In contrast to the conventional thermochemical conversion method that requires huge energy input, the electrochemical conversion of CO2 using a CO2 electrolyzer can be operated under mild conditions and can be powered using renewable energy sources, such as solar, wind, tide, and geothermal energy.
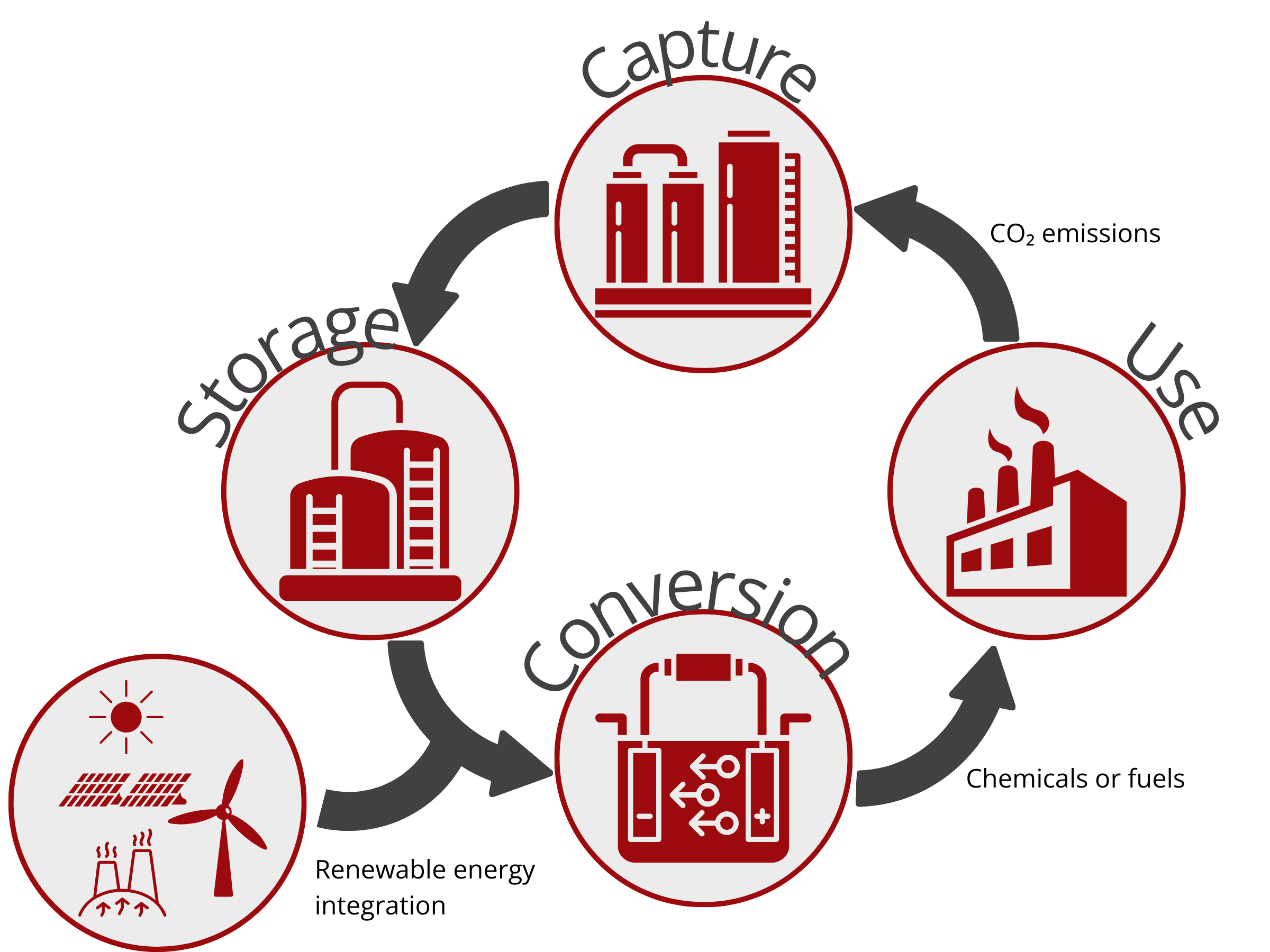
As such, electrochemical techniques can be carbon negative, thereby closing the carbon loop and possibly reducing CO2 atmospheric emission. Additionally, unlike some methods, electrolysis has a single-step dissociation process without moving parts, allowing the separate release of products in the anode and cathode compartments with solid electrolyte. Electrolysis cells are well-suited for mass production and automated maintenance.
Advantages and disadvantages of carbon utilization technologies
Carbon Utilization Technology | Advantages | Disadvantages |
Thermal Conversion | High conversion efficiency | Energy-intensive processes |
Versatility in product outputs | Limited selectivity in product formation | |
Applicable to various feedstocks | Some processes may release pollutants | |
Established technologies in certain applications | High operational temperatures may affect materials | |
Electrochemical Conversion | Efficient utilization of renewable energy sources | Energy-intensive electrochemical processes |
Direct conversion to valuable products | High capital and operating costs | |
Flexibility in the type of products generated | Limited scalability | |
Potential for integration with renewable sources | Technological challenges in scaling up production | |
Biological Conversion | Sustainable and renewable approach | Productivity and efficiency depend on biological systems |
Bio-based products, fuels, and chemicals | Sensitivity to environmental conditions | |
Utilizes microorganisms for CO2 conversion | Limited control over metabolic pathways | |
Potential for low-energy conversion processes | Contamination and stability issues |
What are the key processes involved in carbon dioxide electrolysis?
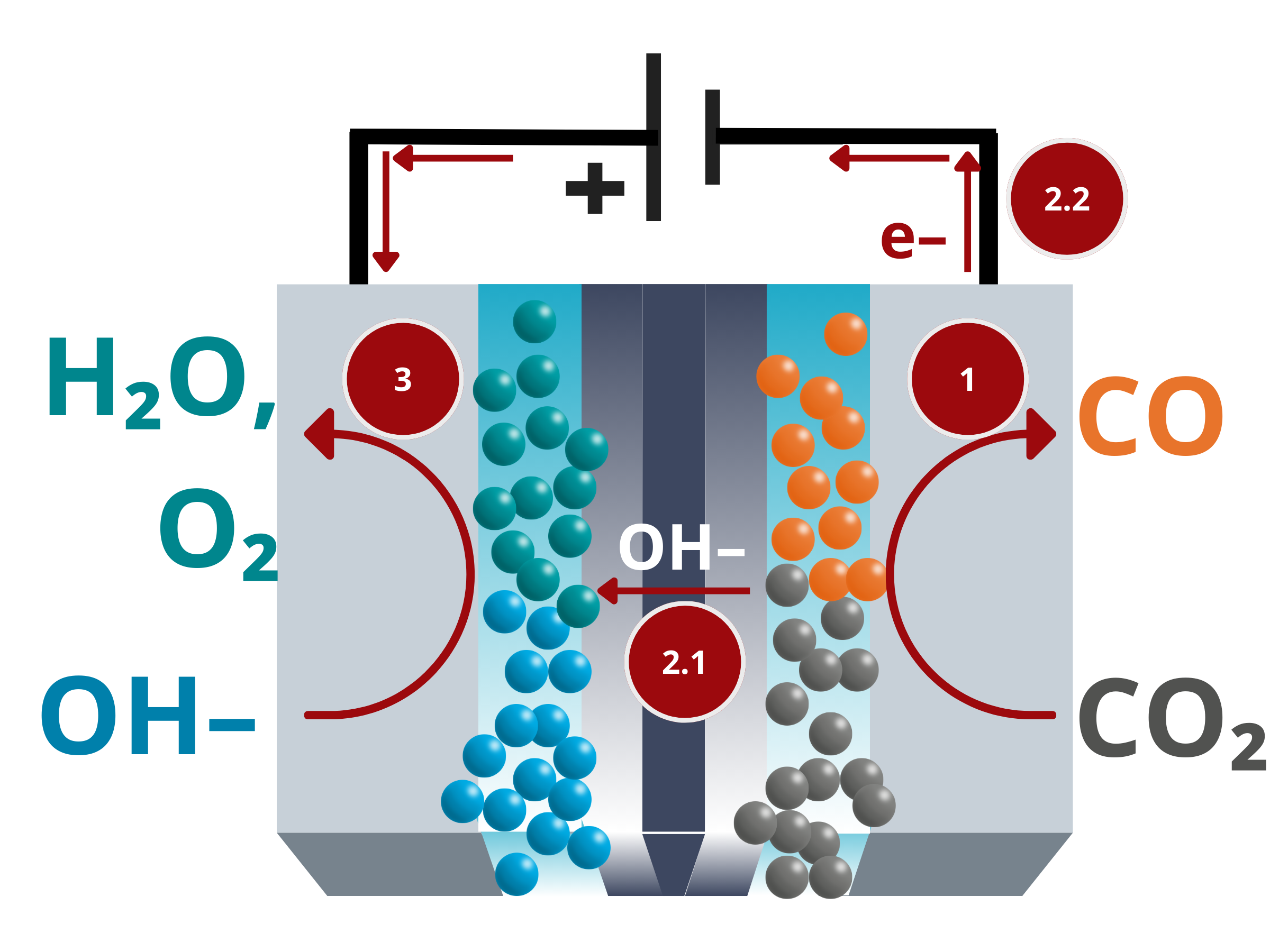
- CO2 reduction reaction. During CO2 electrolysis, CO2 is introduced and dissolved in the catholyte. Under the influence of an applied electrical potential, the dissolved CO2 undergoes reduction reactions at the cathode to form the desired product.
For example, for CO formation, the reaction is:
CO2(aq) + H2O + 2 e– → CO + 2 OH–. - Ion and electron transfer. To complete the circuit, the generated OH– ions move from the cathode to the anode through the ion exchange membrane. On the other hand, the electrons travel along the external wirings of the circuit.
- Oxidation. OH– ions that cross from the cathode to the anode undergoes oxidation or oxygen evolution reaction, which produces water and O2 gas.
2 OH– → O2(g) + 2 H2O + 4 e–
High Value-Added Products from CO₂ Conversion
Depending on the energy input, operating and reaction conditions, and metal or alloy electrodes/catalysts employed, the electrolysis or electrochemical reduction of CO2 can generate different products, such as carbon monoxide (CO), formic acid (HCOOH), hydrocarbons like ethylene (C2H4), and alcohols (e.g. CH3OH).
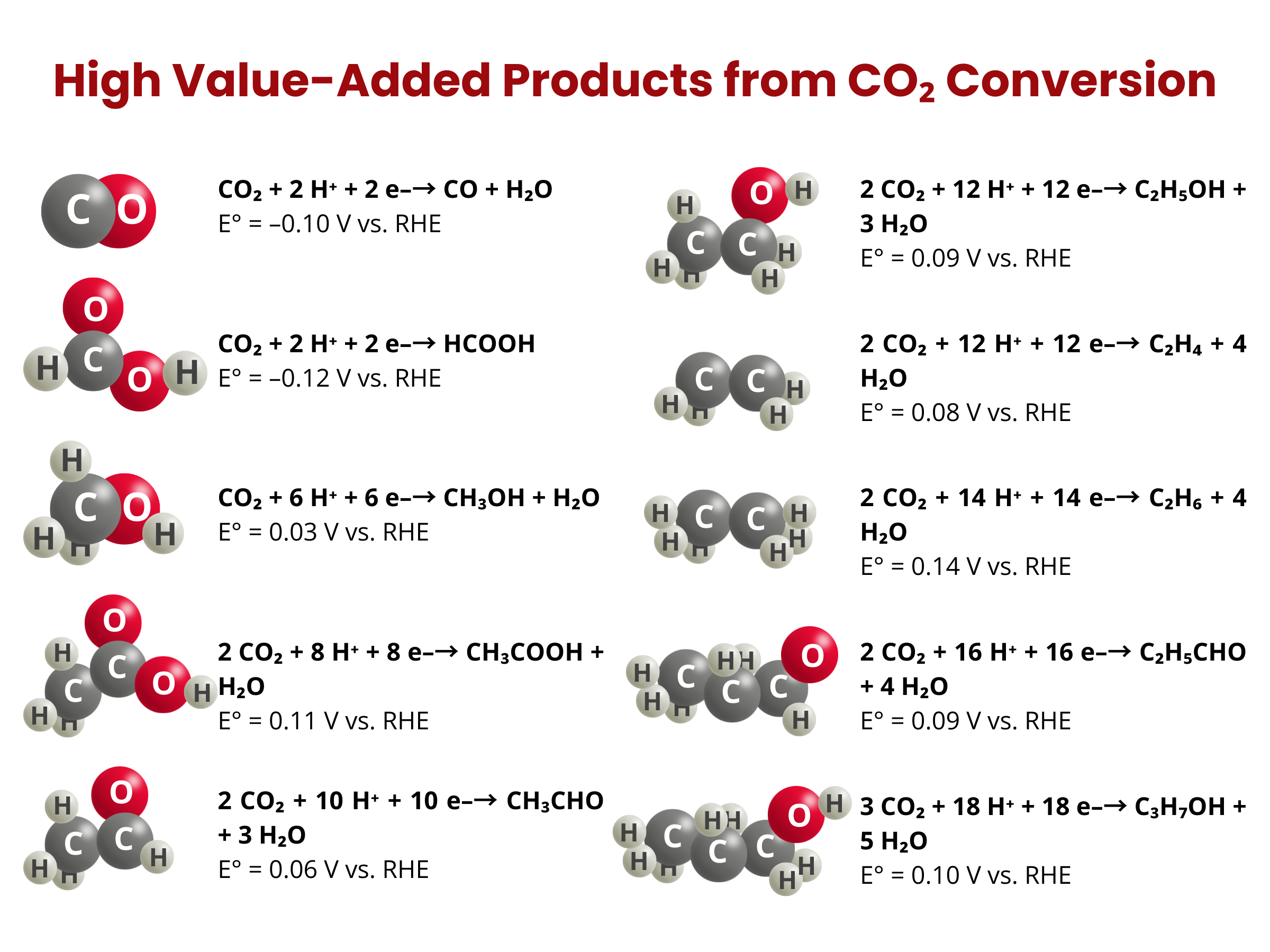
What are the different types of electrolysis cells used in carbon dioxide reduction processes?
CO2RR electrolyzers are classified as H-cells or flow cells.
- H-cells earn their name due to their H-shaped design. In these reactors, the anode and cathode chambers contain liquid electrolytes and are separated by an ion exchange membrane. This setup prevents the unwanted mixing of reactants and the reoxidation of products back into CO2. H-cells find extensive use in electrochemical CO2 reduction research, particularly in studies on catalyst design and screening because this setup enables straightforward and easy testing procedures. However, the low solubility of CO2 in aqueous electrolytes at atmospheric conditions (only 34 mM) causes mass transport limitation when conducting electrolysis in H-type cells. This restricts the current density to values well below 100 mA cm–2. For reference, target industrial scale throughput is set at 300 mA cm–2. Results obtained in an H-type cell are not directly applicable to its performance under industrial conditions. Consequently, testing and optimizing catalysts under realistic operating conditions at higher current densities require alternative setups.
- Flow cells were designed to perform CO2 electrolysis at an industrial scale. In contrast to H-cells wherein CO2 is supplied and dissolved in the liquid catholyte, CO2 is transported in the gaseous phase in flow cells. This makes the reaction not limited by the solubility of gaseous CO2 in a liquid electrolyte. Flow cells are continuous reactors in which CO2 and the electrolyte are continuously cycled, allowing the device to reach current densities >200 mA cm–2. Depending on the state of the electrolyte used, flow cells can be further classified as liquid-phase or solid phase electrolyzers. In liquid-phase flow cells, the cathode and anode compartments are also separated by an ion Exchange Membrane (IEM), which allows the migration of ions essential for the electrochemical reactions while preventing the undesired crossover of liquid products from the cathode to the anode side and vice versa. In contrast, in solid-phase flow cells, solid materials or components play a significant role in the cell's operation. This could involve the use of solid electrolytes, solid-state electrodes, or other solid components within the electrochemical cell.
Comparison between H-cells and flow cells
Feature | H-cells | Flow Cells |
Operation Principle | Electrochemical reduction of CO2 occurs in a single cell or compartment. | Electrochemical reduction of CO2 takes place in a continuous flow system. |
Design | Typically a closed system with electrodes immersed in a liquid electrolyte. | Consists of a flow-through setup with electrodes placed in a continuous flow path. |
Mass Transfer | May face limitations in mass transport, especially in the bulk liquid. | Offers better mass transfer due to continuous flow, reducing concentration gradients. |
Productivity | Limited by mass transport constraints, potentially leading to lower productivity. | Enhanced productivity due to improved mass transfer, leading to higher conversion rates. |
Control | Generally simpler control systems as the reaction occurs in a confined space. | Requires more sophisticated control systems to manage continuous flow parameters. |
Energy Efficiency | May have lower energy efficiency due to mass transport limitations. | Higher energy efficiency can be achieved with optimized flow conditions. |
Scalability | May face challenges in scaling up due to limitations in mass transport. | Generally more scalable as adjustments in flow rates can accommodate larger systems. |
Selectivity | Selectivity can be affected by concentration gradients in the liquid phase. | Improved selectivity as continuous flow conditions allow better control over reaction parameters. |
Applications | Suitable for laboratory-scale experiments and some small-scale applications. | Ideal for larger-scale industrial applications where continuous production is desired. |
Advantages | Simplicity in design and operation for small-scale setups. | Enhanced mass transfer and higher productivity for large-scale applications. |
Challenges | Mass transport limitations may restrict efficiency and productivity. | Requires more complex engineering and control systems, potentially increasing costs. |
What are the primary components of the electrolysis cells used in carbon dioxide reduction processes?
Electrolysis cells used in carbon dioxide reduction processes typically consist of several key components that facilitate the conversion of carbon dioxide into valuable products. The primary components of these cells include:
1. Anode catalyst and substrate. The anode is the electrode where oxidation reactions occur. The anode reaction also affects the overall energy efficiency of the cell. As such, OER or water oxidation catalysts are also critical. Typical anode substrates used are non-porous metal substrates.
2. Cathode catalyst and substrate. In a liquid-phase flow cell, the CO2 reduction reaction occurs at a gas diffusion electrode. A gas diffusion electrode (GDE) typically consists of a porous and conductive substrate or gas diffusion layer (e.g., graphitized carbon paper or cloth) with a catalyst layer (commonly precious metals like platinum) for enhancing electrochemical reactions. Common CO2 reduction catalysts include metals (Cu, Ag, Pt, and Au), metal–organic frameworks (Cu-, and porphyrin-based MOFs), nitrogen-doped carbon materials, and single atom catalysts. In certain applications, some GDEs may contain hydrophobic coating to repel water.3. Electrolyte. The electrolyte is the medium through which ions can move between the anode and cathode. It may be a liquid or solid substance that facilitates the ionic conduction necessary for the electrochemical reactions.
4. Ion Exchange Membrane (IEM). Regardless of the type of electrochemical cell, an ion exchange membrane is used. The IEM allows the migration of ions while preventing the unwanted crossover of reactants or products between the two compartments.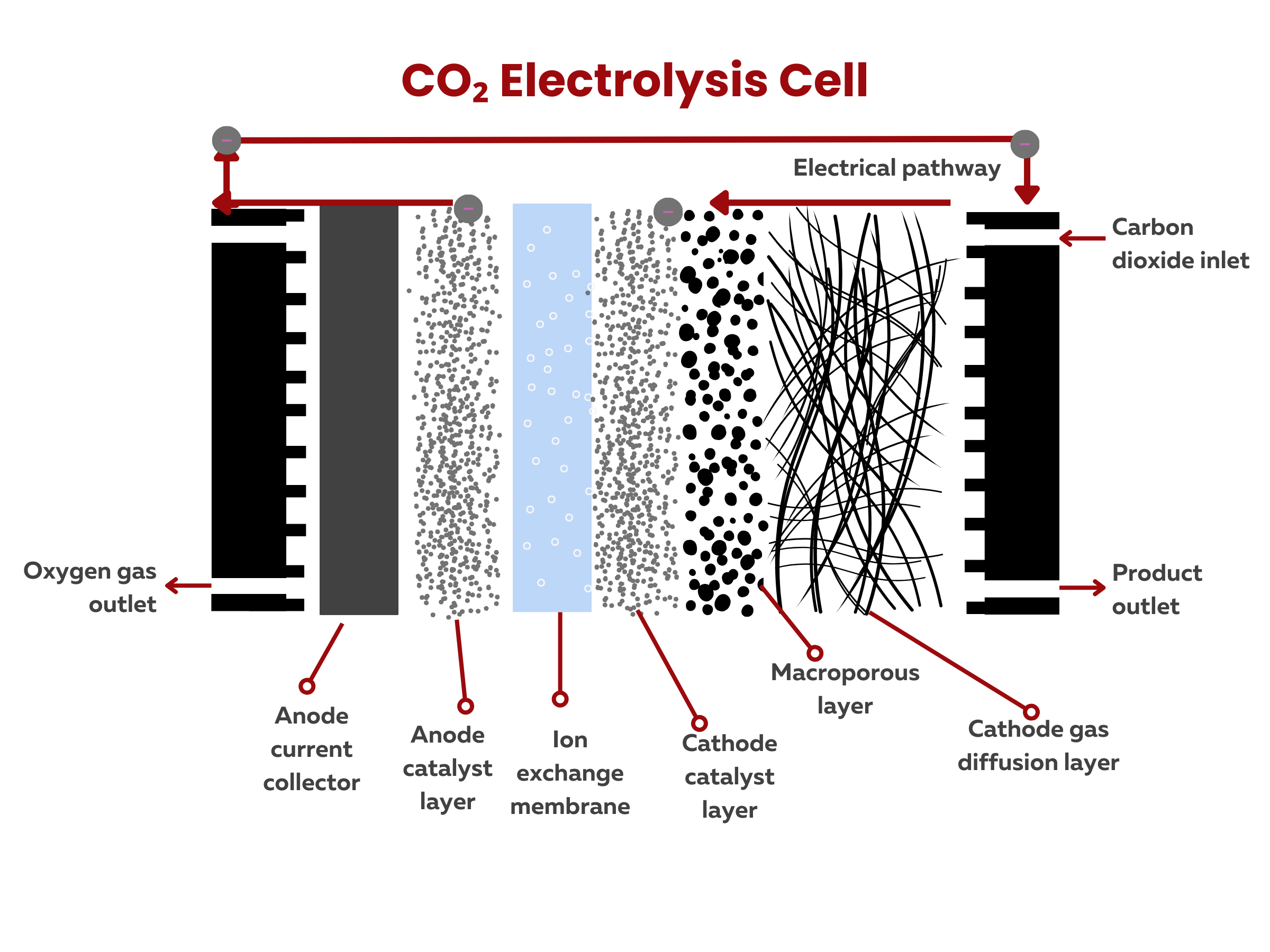