Printable Electronics Inks
Printed electronics are electrical devices that have been made by using printing processes to apply functional (conductive) coatings onto various substrates. can be thin, flexible circuits produced at highvolume and low cost. A wide range of potential applications for printed electronics and printed functionalities are under development and many companies are working on the industrialization of these applications, trying to incorporate more functionalities in smaller devices for reduced cost.
There are various printable electronic materials but for our main focus area, Printable inks we can differentiate between Conductive, Resistive, Dielectric and Electrode inks. Conductive inks are filled with silver, carbon and other conductive pigments for circuit, switch and antenna printing. Resistive inks are based on blends of silver, carbon and non-conductive pigments to adjust resistance levels for printed resistors, potentiometers and heating elements. Dielectric inks are used for printing dielectric layers, conformal coatings and encapsulations. And finally, Electrode inks are based on silver/silver chloride for biosensors, ECG electrodes and transdermal drug delivery.
These inks for printable electronics can be used on a variety of substrates such as plastic foils, PCB materials, paper and cardboard, glass and ceramic and textile. The selection of the substrate can limit product usage due to solvent sensitivity, temperature limitations and compatibility. Therefore product performance on the substrate and product/process compatibility with the substrate need to be checked beforehand.
JNC PI-6643-004 | Insulating Polyimide Ink
- Thermal Curable
- High Heat Resistance
- Inkjet Printing
- 6 - 8 weeks
JNC PI-6302-004 | Insulating Polyimide Ink
- Thermal Curable
- Low Temperature Curing
- High Heat Resistance
- 6 - 8 weeks
JNC PI-6322-001 | Insulating Polyimide Ink
- Thermal Curable
- Heat Resistance
- Low Temperature Curing
- 6 - 8 weeks
JNC PI-6673-002 | Insulating Polyimide Ink
- Thermal Curable
- Low Temperature Curing
- Low Warpage
- 6 - 8 weeks
JNC PA-1210-020 | Insulating Polyacrylate Ink
- UV Curable/ Solvent free
- Standard
- Optoelectronics
- No longer available
JNC PA-1210-034 | Insulating Polyacrylate Ink
- UV Curable/ Solvent free
- High Insulation reliability for fine pitch devices
- Advance Sensors
- No longer available
JNC PA-1210-035 | Insulating Polyacrylate Ink
- UV Curable/ Solvent free
- High Insulation reliability for thin film devices
- Optical Devices
- 6 - 8 weeks
JNC PA-1510-003| Insulating Polyacrylate
- UV curable
- Heat Resistance
- Removable process material
- No longer available
JNC PA-1510-005| Insulating Polyacrylate
- UV curable
- Dissolutes in 5 minutes
- Removable process material
- No longer available
LOCTITE ECI 8001 E&C
- Rapid heating with fast, defined cut-off temperatures, no external control devices needed
- Printable on most common substrates
- Screen printable
- 8 - 12 weeks
LOCTITE ECI 7004HR E&C
- High Resistivity
- Screen Printable
- Flexible low temperature drying cycles
- 8 - 12 weeks
LOCTITE NCI 7002 E&C
- Non-Conductive
- Screen Printable
- Flexible low temperature drying cycles
- 8 - 12 weeks
LOCTITE EDAG 479SS E&C
- Good conductivity
- Screen printable
- Superior adhesion to polyester film
- 8 - 12 weeks
LOCTITE ECI 1014 E&C
- Low temperature drying
- High conductivity
- Compatible for use with polycarbonate, polyester and polyurethane
- 8 - 12 weeks
LOCTITE ABLESTIK EMI 3620FA
- Compartment EMI Shielding
- No popcorning and delamination
- For gap, hole and trench filling
- 8 - 12 weeks
LOCTITE ABLESTIK EMI 8660S
- Conformal EMI shielding
- Excellent adhesion on EMC, Au, Ag
- Spray, Print, Dispense
- 8 - 12 weeks
LOCTITE ECI1011 E&C
- Highly Conductive Ink
- Screen and Flexo printable
- Paper and PET substrates
- 8 - 12 weeks
Product Selector Guide
Henkel Printable Inks
Product | Description | Viscosity (mPAs) | Density (g/cm3) | Cure Type | Cure Schedule | Process | Substrates | Application |
---|---|---|---|---|---|---|---|---|
ECI 1006 | Highly conductive silver ink for touch screen applications | 57,000 | 2.6 | Heat | 10min @130°C | Screen print | ITO, PET | ITO film, Membrane switches, Digitizers, Flexible circuits and Electroluminescent lamps |
ECI 1010 | Highly conductive silver ink with high flexibility | 9,000 | 2.1 | Heat | 15min @120°C | Screen print and Flexographic | PET films | Smartcard, flexible circuits, PCB, switches, RFID |
ECI 1011 | Highly conductive silver ink for thinner lines | 2,800 | 3 | Heat | 10min @150°C | Screen print and Flexographic | Paper, PET | Smartcard, Flexible switches, RFID |
ECI 1014 | Highly conductive, silver, high-elongation ink based on a thermoplastic polyurethane binder | 10,000 | 2.2 | Heat | 15minutes @120°C | Screen print | PET, PC, TPU, PI, PEN | Inks and coatings, Conductive Ink |
ECI 7004 | screen printable, high resistance carbon solvent-based ink | 10,000 | 1.1 | Heat | 10 minutes @ 120°C | Screen print | Treated polyester, Polyimide | Force sensitive modules, Printed resistors and Sensing devices |
ECI 8001 | Positive Temperature Coefficient (PTC) screen printable conductive ink | 6,500 | 1.0 | Heat | 10 minutes @ 120°C | Screen print | PET, PEN, PI | Self regulating heating elements |
EDAG 461SS | Extremely flexible polyester resin with a butyl cellosolve acetate | 17,000 | - | Heat | 15min @93°C | Screen print | - | ITO coated films, membrane switches, digitizers, flexible circuits |
EDAG 479SS | Halogen-free conductive ink with good flexibility | 20,000 | 2.56 | Heat | 15min @93°C | Screen print | PET , PEN, PI | Membrane switches and Flexible circuitry display devices |
EDAG 7019 | flexible conductive ink with low electrical resistance and long screen residence time | 14,000 | - | Heat | 10min @107°C | - | - | - |
EDAG 725A(6S54) | Conductive ink that requires no thinning | 12,500 | 2.14 | Heat | 15min @120°C | - | PET films | Membrane keyboards, membrane touch switches |
EDAG 965SS | Very finely divided graphite particles dispersed in a thermoplastic resin | 32,500 | - | Heat | 15min @120 | Screen print | Polyester | Membrane switches, keyboards, protection from ESD |
EDAG PF 407A | Carbon filled ink for contact areas | 35,000 | 1.12 | Heat | 30min @90°C | Stencil print | PET, Polyimide, Paper, Carboard | Resistors, Membrane switches, heating elements |
EDAG PF 407C | Thick polyester film for low voltage circuitry | 42,500 | 1.1 | Heat | 15min @120°C | Screen print | Polyester, Polyimide, Polycarbonate, Paper, Cardboard | Printed resistors, membrane touch switches, heating elements, flexible circuits and protection from ESD |
EDAG PF 410 | - | 17,500 | - | Heat | 15min @120°C | Screen print | Polyester | manual, semi automatic, high speed reel to reel screen printing |
EDAG PM 406V1 | Highly conductive and solids content inks | 21,600 | 3 | Heat | 15min @120°C | Screen print | PET, Paper, PVC | Printed circuitry, RFID, conductive circuits |
EDAG PF 455B | UV curable acrylate and excellent adhesion | 13,500 | 1,02 | UV | 120Watt/cm | - | - | Printed circuitry, conductive circuits |
EDAG PF 455BC | Translucent UV curable acrylate | 13,500 | 1,02 | UV | 120Watt/cm | - | - | Printed circuitry, conductive circuits |
NCI 7002 | screen printable ink that is specifically designed for blending with LOCTITE ECI 7004HR E&C | 10,000 - 25,000 | 1.27 | Heat | 5 to 10 minutes @ 120°C | Screen print | Treated polyester and Polyimide | Printed resistors, Sensing devices, Heating elements, Protection against electrostatic discharge (ESD) |
Product | Description | Viscosity (mPAs) | Volume resistivity (Ω*cm) | Cure Type | Cure Schedule | CTE | TG(℃) | Application |
---|---|---|---|---|---|---|---|---|
PI-6643-004 | High-heat insulating polyimide ink | 12 | 1E+16 | Heat | 30min @350°C | 60 | 395 | Aerospace Engineering, Electronics manufacturing, High temperature sensors |
PI-6302-004 | Low-temperature cured insulating polyimide ink | 6 | 1E+16 | Heat | 30min @230°C | 65 | 255 | Electronics Manufacturing, Consumer Electronics, Sensors and IoT Devices |
PI-6322-001 | Polyimide insulating ink designed to provide thermally curable solution to heat resistance and electrical insulation | 11 | 1E+16 | Heat | 120min @180°C | 75 | 250 | Aerospace and Defense, Electronics Manufacturing, Industrial Sensors |
PI-6673-002 | Low-temperature cured insulating polyimide ink specially designed to meet the demands of high thermal applications | 9 | 2E+16 | Heat | 60min @175°C | 146 | 140 | Electronics Manufacturing, Consumer Electronics, Sensors and IoT Devices |
PA-1210-020 | UV-curable, solvent-free polyacrylate insulating ink | 23 | 1E+16 | UV | 2,000mJ/cm2 @ 365nm | 55 | 116 | Electronics Manufacturing, Optoelectronics, Microelectronics |
PA-1210-034 | UV-curable, solvent-free polyacrylate insulating ink with high reliability | 35 | 1E+15 | UV | 2,000mJ/cm2 @ 365nm | 91 | 136 | Fine Pitch Electronics, Microfabrication, Advance Sensors |
PA-1210-035 | UV-curable, solvent-free polyacrylate insulating ink, with a perfect balance between flexibility and durability | 36 | 6E+16 | UV | 2,000mJ/cm2 @ 365nm | 76 | 126 | Thin Film Electronics, Microfabrication, Optical Devices |
PA-1510-003 | UV-curable, solvent-free polyacrylate process material with its advanced polyacrylate technology | 5.4 | - | UV | - | - | 124 | Microelectronics Mechanical Systems (MEMS), Assembly Line Component Protection |
PA-1510-005 | UV-curable, solvent-free polyacrylate process material | 4.4 | - | UV | - | - | 135 | Microelectronics Mechanical Systems (MEMS), Assembly Line Component Protection |
Frequently Asked Questions
Can I really make a printed antenna?
Yes. An antenna is an electrical device which converts radio waves in an AC current and vice versa. Therefore an antenna needs to be conductive. Our silver inks in combination with dielectric inks (crossovers) can be used for printing HF, UHF and other antennae for RFID cards and labels.
The same conductive materials can be used for printing automotive, telephone and other antennae.
How do formable inks work?
The electronic circuitry is printed onto the flat substrate in one or multiple layers by screen printing and then components are mounted on the printed substrate. Afterwards, the flat substrate is thermoformed by either vacuum thermoforming or mechanical thermoforming creating the circuit form.
Then injection molding is used to put the plastic in place and result in the final product. Injection molding is a manufacturing process for producing parts by injecting plastic into a mold.
What are the benefits of using printed insulating inks?
Printed insulating inks offer advantages like simplified manufacturing processes, reduced material waste, and the ability to create intricate designs. They also provide a cost-effective way to isolate different circuit elements without the need for traditional insulating materials like tapes or films.
Can printed insulating inks replace traditional insulation methods?
Printed insulating inks offer an alternative to traditional insulation methods like tapes and films, especially for applications where space constraints or intricate designs are important. However, the choice between methods depends on the specific requirements of the application. It is difficult to build up multiple layers or thicker films with PI ink. If you want to laminate in multiple layers, you can use PA ink and laminate with UV pinning. PA ink is traditionally inferior to PI ink in terms of heat resistance, so whether or not the required properties are met will determine whether or not PA ink can be used for your application.
Which substrates are compatible with printed insulating inks?
Printed insulating inks can be applied to a variety of substrates, including rigid and flexible circuit boards, glass, ceramics, and even certain types of plastics. The compatibility depends on the specific ink formulation and the substrate's surface properties.
What is the amount of cleaner usage is recommended on printable inks?
The rule of thumb is 3x the volume of the PI or PA printable ink
What is the Shelf life and Opened bottle pot life of JNC printable materials?
Before opening, the product is basically guaranteed for 6 months after shipping which have exceptions depending on the grade. Once the product has been opened, JNC does not guarantee its quality.
Learn More
Process and Application methods
There are various ways to apply printable inks. The main ones are:
- Rotogravure printing
- Flexographic printing
- Screen printing
- Dispenser printing
- Inkjet printing
- Aerosol jet and spray printing
They all come with their pros and cons and usually these are in terms of design flexibility, printing speed, quality, thickness and cost.
The advantage of screen printing is the ability to apply thick layers (5-25 µm) when compared to rotogravure or flexographic processes that can apply 1-2um in one print pass. On the other hand flat bed screen printing is much slower than flexography or rotogravure. So it all comes down to your needs to strike a perfect balance. There is also stencil printing but that is a more "simplistic" solution for dots and lines and won\'t be discussed here.
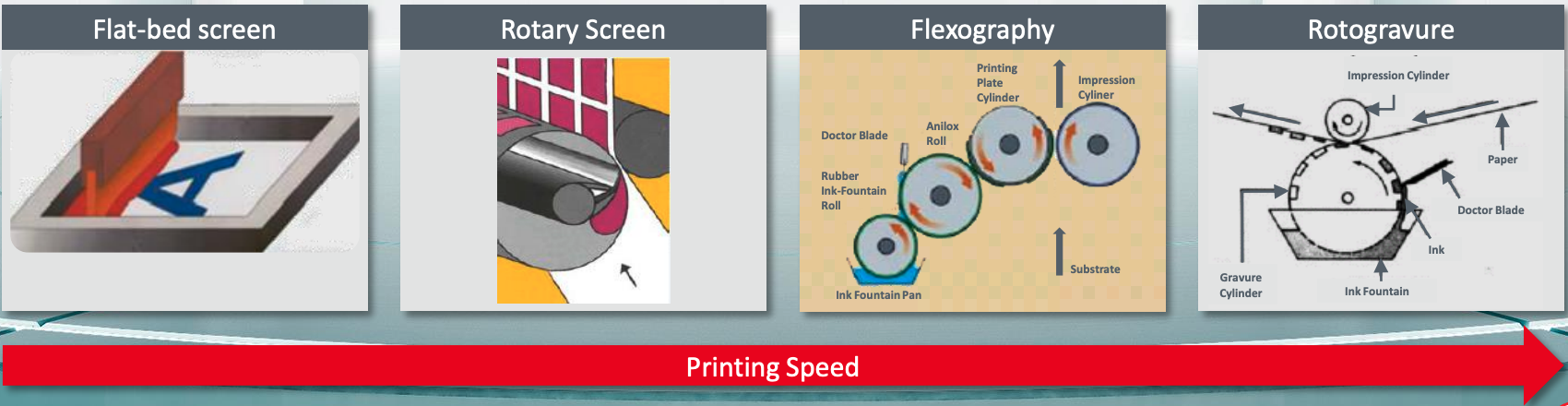
Rotogravure printing
Flexographic and Rotogravure printing are high speed printing processes using Anilox or Gravure rolls to control the amount of applied ink.
Rotogravure works on the principle of vacuum printing. There is a metal hole with the required image on it which passes through an inkpad. A doctor blade scrapes the ink from the roll\'s surface and just leaves the ink in the metal image. This ink image is then pressed against the substrate and the impression cylinder creating the final printed result.
As we will explain later, rotographic printing is a direct and really stiff (not flexible) process. In order to change the design you need to spend a significant amount of money to adjust your equipment. Having said that, this type of printing, even though non flexible, admittedly prints much better than the flexographic process. It is recommended for "standard" designs when you know you will have a specific design that will not need to change often.
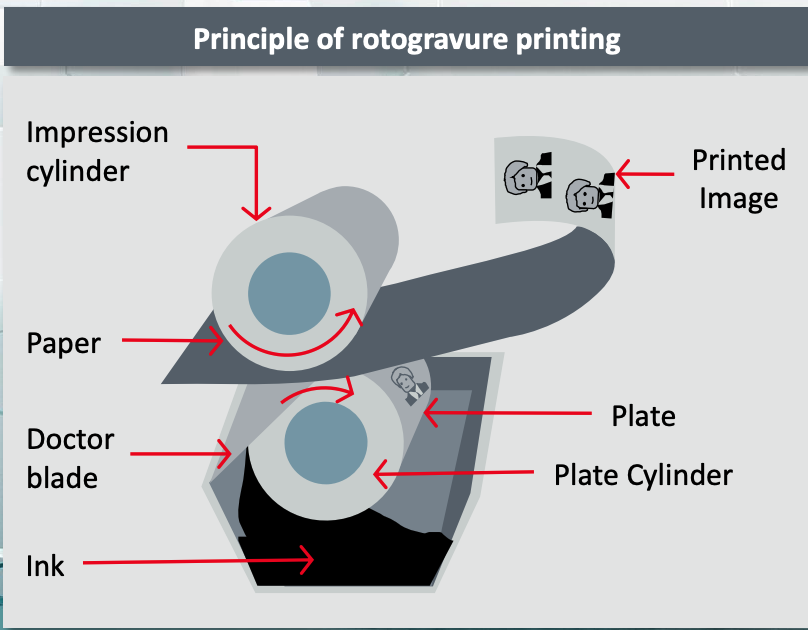
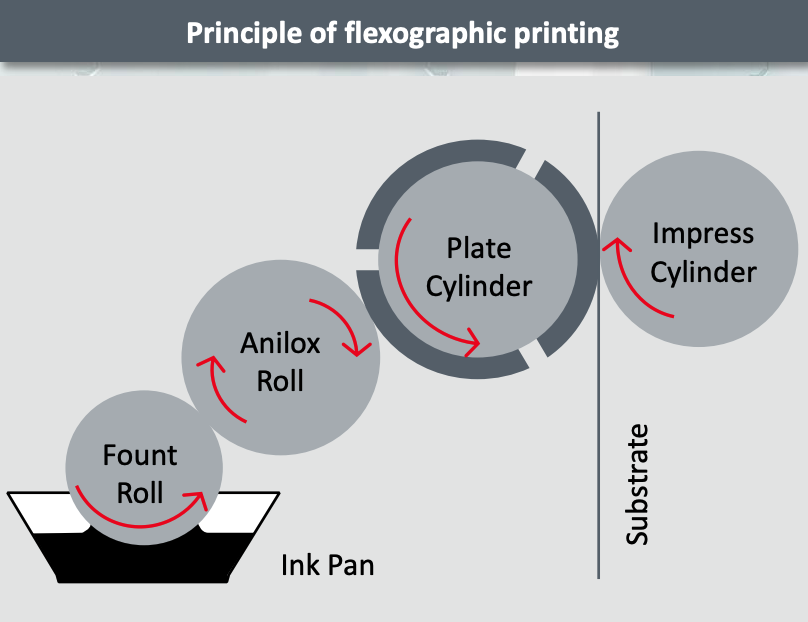
Flexographic printing
The principle of flexographic printing is almost similar. The fount roll is dipped in an ink pan. This roll touches an Anilox roll that doesn\'t contain the image yet but is mostly used as a "clean" ink transfer. A doctor blade scrapes the excess ink from the roll preparing it for the next step. The entire Anilox roll has ink that is being transferred to an engraved rubber sleeve mounted on a plate cylinder. Now you have the clean "inked" image ready to be pressed on the substrate. The final step is identical with rotography. The cylinder connects with the impression cylinder, pressing the substrate in between and leaving the image on top of it.
Rotogravure printing is a direct process while flexographic is an indirect process with the plate cylinder in between. The advantage of the flexo process is that it is a much, much cheaper option for single prints since you only need to create a rubber sleeve with the image and not remake the entire plate roll. The cost of making a rubber sleeve is almost 20-30 times lower than having to make a metal roll/mold from scratch, as you would for the Rotogravure process.
Screen printing
Screen printing is a printing technique that uses a woven mesh to support an inkblocking stencil. A squeegee is moved across the screen stencil forcing the ink past the threads of the woven mesh in the open areas. For screen printing you use this mesh acting like a driver between the paste and the substrate. After applying pressure with the squeegee the air pressure will press out the ink from the open area and onto the substrate to imprint the circuit.
Do not confuse Screen and Stencil printing. Stencil printing would be an option if you only wanted to print dots and small lines but not for a whole circuit. Typically metal stencils don\'t need a distance from the substrate and have a different operational "logic" even though they look and sound similar.
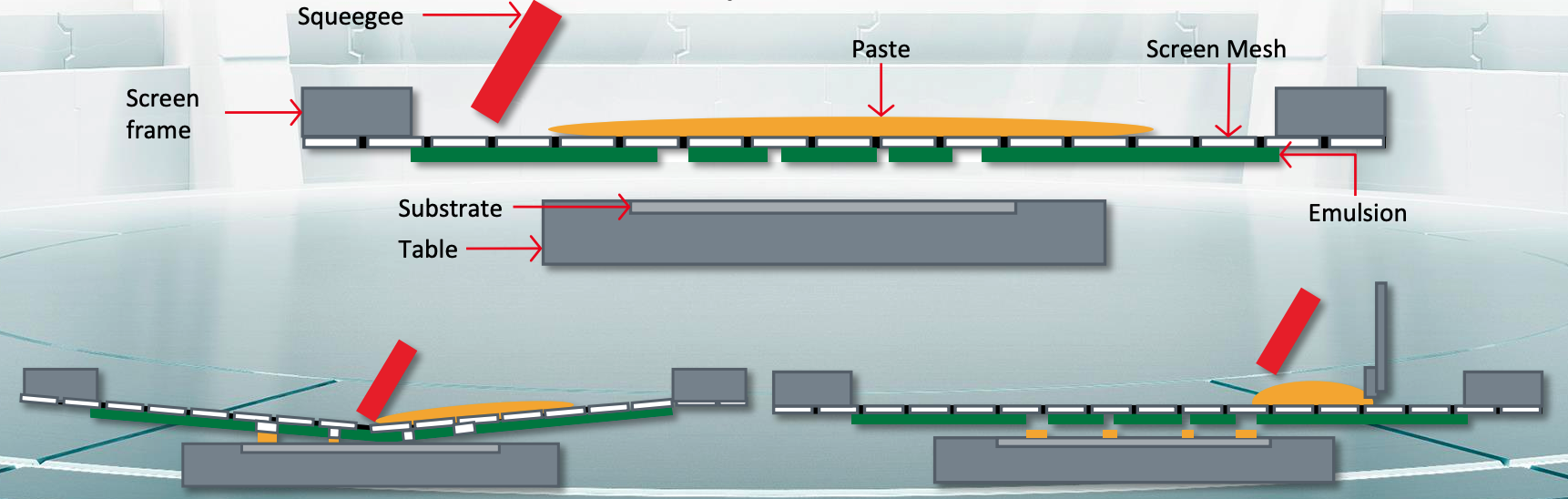
Dispenser printing
In dispenser printing, an ink nozzle continuously sprays ink slurries onto a substrate under pneumatic pressure. The substrate is moved by an x-y stage, typically under computer control, to create the desired design topology. Conformal writing with feature sizes as small as 250 nm can be accomplished by adjusting the ink rheology, stage movement speed, and distance between nozzle and substrate. Moreover, dispenser printing is capable of printing very thick films up to 200 µm.
Inkjet printing
Inkjet printing is a derivative of dispenser printing where ink drops exit the nozzle by a dynamic process. Inkjet printing is generally categorized into the continuous inkjet and the drop-on-demand (DoD) method. Due to its material relevance for thermoelectric device fabrication, we will primarily focus on DoD printing. By controlling the contraction expansion of the piezoelectric actuator, individual ink droplets can be jetted out from the nozzle forming the desired pattern on the substrate. The printed pattern can be easily modifed by changing the digital file that controls the actuator. The printability depends on the nozzle radius and viscosity, density and surface tension of the ink.
Aerosol jet and Spray Printing
Aerosol jet printing is another popular method for printable electronics. In this method, an atomizer aerosolizes the ink into liquid particles of size ranging from 20 nm to 5 mm. Inert gas or compressed airfow is used to transfer the ink particle to the substrate. The main advantage of spray printing is the higher allowable distance between print head and substrate making it possible to print on non-flat and non smooth substrates. The achievable resolution is higher than inkjet printing. However, edge sharpness in lower and localized crystallization caused by the sheath gas can detrimentally affect the bonding layer quality.
Drying and Curing
Proper drying and curing is very important to obtain the required coating performance. Drying refers to the solvent evaporation while curing refers to the active binders and resins that crosslink. While printing is a very important part of the process, drying is as important.
- Products are applied wet onto the substrate
- The drying/curing process removes the solvent from the coating and drives the crosslinking of the resin matrix (thermosetting systems)
- Coating shrinks and interparticle contacts generate the functionality (conductivity)
Solvent needs to be "removed" from the initial layer during the drying step, something that will cause a shrinkage of ~50-70% of the thickness and result in inter-particle contacts that will give the final functionality and conductivity of the coating.
There are multiple solvents that can be used that depend on the processes and how fast or slow we want to the product to dry. For example for the fast drying solvents of flexo/gravure printable inks, solvents can be propyl acetates while for screen printing where we need a proper "open" screen time and slower drying, "solvents" used are carbitol acetate, butyl glycol acetate and such.
It is crucial to notice that "dry" to touch does not mean cured. You should make sure that you follow the instructions on the technical sheets in order to achieve the final properties and keep in mind that drying below 60°C (at least for screen printable inks) is not possible.
The drying mechanism is different when a product is UV curable since there\'s no solvent involved and the drying/curing process does not exist in the same sense. UV curable inks are a blend of monomers and oligomers that react together when exposed to UV light. In this case there\'s hardly any shrinkage or weight loss and exposure to UV light "just" propagates or polymerises the film, resulting in the final properties.