Fiber Felts
Fiber Felts, are a versatile industrial solution for diverse applications. These three-dimensional structures of arranged fibers are offered in two variations: Sintered and Non-Sintered. Sintered Fiber Felts excel in high-temperature, high-purity settings, offering precision and durability. Non-Sintered Fiber Felts, economical options, are suited for applications without extreme temperature demands.
Sintered Fiber Felts excel in extreme environments. Crafted from materials like titanium, nickel, stainless steel alloys (including 316), and graphite, these felts offer high-temperature resistance, making them ideal for applications in petrochemicals, water treatment, and metallurgy. Their intricate, sintered structures deliver excellent filtration quality, ensuring your processes run smoothly.
Non-Sintered Fiber Felts, on the other hand, provide a cost-effective filtration solution for less demanding conditions. Their versatility and compatibility with various materials make them suitable for a wide range of applications, from air purification to electrolysis.
You can choose Fiber Felts in various materials: titanium, nickel, stainless steel alloys (like 316), and graphite, tailored to distinct applications. Industries such as petrochemicals, water treatment, and metallurgy rely on Fiber Felts for their efficient particle control, high-purity filtration, and reliability.
LINQCELL GFP2000 | Graphite Felt
- 2.00 mm - 2000 µm - 78 mil
- High chemical resistance, electrical conductivity, and open porosity
- Electrode materials for high-temperature batteries
- 6 - 8 weeks
TFP1200 | 1200um Titanium Fiber Paper
- 1.20mm - 1200um - 47.2mil
- 50 - 60% Porosity
- Electrode and Support structure
- 8 - 12 weeks
TPP500 | 500um Sintered Titanium Powder
- 0.50mm - 500um - 20mil
- 30–40% Porosity
- Gas Diffusion and Porous Transport Layer for PEM Water Electrolyzers and Fuel Cells
- In stock
LINQCELL GFP3000 | Graphite Felt
- 3 mm - 3000 µm - 118 mil
- High chemical resistance, electrical conductivity, and open porosity
- Electrode materials for high-temperature batteries
- 6 - 8 weeks
LINQCELL GFP6500 | Graphite Felt
- 6.5 mm - 6500 µm - 255 mil
- High chemical resistance, electrical conductivity, and open porosity
- Electrode materials for high-temperature batteries
- 6 - 8 weeks
LINQCELL NFP 250 | Nickel Sintered Fiber Felt
- 0.25mm - 250um - 9.8mil
- Ni200 and Ni201 alloys
- Excellent catalyst support
- 4 - 6 weeks
LINQCELL NFP 500 | Nickel Sintered Fiber Felt
- 0.5mm - 500um - 19.6mil
- Ni200 and Ni201 alloys
- AEM and Alkaline Water Electrolysis
- 4 - 6 weeks
LINQCELL SFP 250 | Stainless Steel Sintered Fiber Felt
- 0.25mm - 250um - 9.8mils
- Durable and reliable
- Prefiltration support
- 4 - 6 weeks
LINQCELL SFP 600 | Stainless Steel Sintered Fiber Felt
- 0.6mm - 600um - 23.6 mil
- Superior filtration
- Purification and dust collection
- 4 - 6 weeks
LINQCELL SFP 1000 | Stainless Steel Sintered Fiber Felt
- 1mm - 1000um - 39.3mil
- 304, 304L, 316, 316L, 310s
- Filter membrane Support
- 4 - 6 weeks
LINQCELL TFP250 | 250um Titanium Fiber Paper
- 0.25mm - 250um - 9.8mil
- 50 - 60% Porosity
- Electrode and Support structure
- 6 - 8 weeks
LINQCELL TFP250S | 250um Titanium Fiber Paper
- 0.25mm - 250um - 9.8mil
- 60 - 70% Porosity
- Electrode and Support structure
- 6 - 8 weeks
LINQCELL TFP400 | 400um Titanium Fiber Paper
- 0.40mm - 400um - 15.8mil
- 50 - 60% Porosity
- Electrode and Support structure
- 6 - 8 weeks
LINQCELL TFP400S | 400um Titanium Fiber Paper
- 0.40mm - 400um - 15.8mil
- 60 - 70% Porosity
- Electrode and Support structure
- 6 - 8 weeks
LINQCELL TFP 500 | 500um Titanium Sintered Fiber Felt
- 0.5mm - 500um - 19.6mil
- Variable Porosity
- Electrode and Support structure
- 4 - 6 weeks
LINQCELL TFP600 | 600um Titanium Fiber Paper
- 0.60mm - 600um - 23.6mil
- 50 - 60% Porosity
- Electrode and Support structure
- 6 - 8 weeks
LINQCELL TFP600S | 600um Titanium Fiber Paper
- 0.60mm - 600um - 23.6mil
- 60 - 70% Porosity
- Electrode and Support structure
- 6 - 8 weeks
LINQCELL TFP800 | 800um Titanium Fiber Paper
- 0.80mm - 800um - 31.5mil
- 50 - 60% Porosity
- Electrode and Support structure
- 6 - 8 weeks
LINQCELL TFP800S | 800um Titanium Fiber Paper
- 0.80mm - 800um - 31.5mil
- 60 - 70% Porosity
- Electrode and Support structure
- 6 - 8 weeks
LINQCELL TPP1500 | 1500um Sintered Titanium Powder
- 1.5mm - 1500um - 59.1mil
- 30–40% Porosity
- Gas Diffusion and Porous Transport Layer for PEM Water Electrolyzers and Fuel Cells
- 6 - 8 weeks
Product Selector Guide
Item | Porosity (%) | Thickness (um)* | Basis Weight (g) | Actual weight (g)** |
50 - 60 | 250 | 45.5 | 18.3 - 22.6 | |
60 - 70 | 250 | 45.5 | 13.7 - 18.1 | |
50 - 60 | 400 | 72.8 | 29 - 36.3 | |
60 - 70 | 400 | 72.8 | 22 - 29 | |
50-60 | 500 | - | - | |
50 - 60 | 600 | 109.3 | 44 - 54.5 | |
60 - 70 | 600 | 109.3 | 32.8 - 43.6 | |
50 - 60 | 800 | 145.7 | 58.3 - 72.9 | |
60 - 70 | 800 | 145.7 | 43.7 - 58.2 | |
50 - 60 | 1,200 | - | - | |
30 - 40 | 250 | - | - | |
30 - 40 | 500 | - | - | |
30 - 40 | 1500 | - | - |
All the standard sheet sizes are 20 x 20cm
*Thickness tolerance is ±150um for all grades.
**The actual weight of the sheet will depend on the final porosity. This is the expected range.
Item | Porosity (%) | Thickness (um)* | Basis Weight (g) | Actual weight (g)** |
- | 2000 | - | - | |
- | 3000 | - | - | |
- | 6500 | 590 | - |
Frequently Asked Questions
Frequently Asked Questions about Fiber Felts
What are Fiber Felts, and How Are They Used?
Fiber Felts are porous, three-dimensional materials used in various applications such as filtration, catalysis, electrode production, and more. They are prized for their unique structural properties and material choices, which make them highly adaptable to specific industrial requirements.
What Is the Difference Between Sintered and Non-Sintered Fiber Felts?
Sintering is a process where fibers are fused together at high temperatures to create a cohesive structure. Sintered Fiber Felts offer increased durability, temperature resistance, and precise pore control. Non-sintered Fiber Felts, on the other hand, are cost-effective and suitable for applications where these specific advantages are not required.
When Should I Choose Non-Sintered Fiber Felts?
Non-Sintered Fiber Felts are a cost-effective choice for applications where the advantages of sintering, such as high-temperature resistance and pore control, are not necessary. They are often used in applications where regular replacement is acceptable.
Frequently Asked Questions about Titanium fiber papers
What are the main advantages of using titanium fiber papers?
Titanium fiber papers offer several advantages, including high electrical conductivity, corrosion resistance, and mechanical strength. Their porous structure allows for efficient gas diffusion, making them suitable for applications requiring reactant distribution and electrolyte permeation. Additionally, titanium fiber papers are lightweight yet robust, making them ideal for aerospace applications where strength and weight reduction are critical.
How are titanium fiber papers utilized in electrochemical systems?
Titanium fiber papers are used in various roles within electrochemical systems. They can serve as gas diffusion layers, facilitating effective gas diffusion and reactant distribution in electrolyzers and fuel cells. Additionally, titanium fiber papers function as current collectors, providing a conductive pathway for electron transfer. Their porous structure aids in electrolyte flow and supports the overall structural integrity of the system.
What applications can benefit from the use of titanium fiber felt/papers?
Titanium fiber papers find applications in several industries. In electrochemical systems, they are vital for hydrogen production in electrolyzers and oxygen reduction in fuel cells. Their porous nature also makes them suitable for filtration processes, such as particle separation and removal of contaminants from fluids. Furthermore, the aerospace industry benefits from titanium fiber papers due to their lightweight and strong characteristics, enabling sound absorption, thermal management, and reinforcement in composite materials.
Can titanium fiber papers be customized for specific applications?
Yes, titanium papers can be customized to meet specific application requirements, they are both available as sintered fiber papers or as sintered metal powder papers. They can be tailored in terms of thickness, porosity, and surface modifications (double sides) to optimize their performance for desired outcomes. Additionally, different weaving or processing techniques can be employed to enhance their mechanical properties or surface characteristics. Collaborating with manufacturers and experts can help determine the most suitable customization options based on the intended use of titanium fiber papers.
What are the available grades of titanium felts/papers?
The titanium fiber felts for PTL (Proton Exchange Membrane Electrolysis) applications are available in several grades to accommodate various requirements. These grades include TA0, TA1, TA2, TA7, and TA9. TA0, TA1, TA2 are commercially pure titanium grades with varying levels of impurities, TA7 and TA9 are titanium alloy grades containing aluminum and vanadium, offering enhanced mechanical properties suitable for high-performance applications. Each grade offers specific properties and characteristics suited for different operating conditions and performance demands, ensuring versatility and reliability in diverse electrolysis applications.
Why should Titanium fiber felts/papers be coated?
Untreated titanium porous transfer will not be consumed like a carbon Gas Diffusion Layer (GDL) will. However, the presence of oxygen does have an impact if the electrolyzer is being operated at high pressures (1 bar to 3 bars). The untreated titanium surface will quickly form an electrically insulated oxide layer (TiO2) on the surface of the of the small-diameter fibers under high O2 pressures. This oxide coating will eventually affect the efficiency of the overall system acting as an electrical insulator and it will increase the interfacial resistance in the cell, lowering the electrochemical performance. To prevent the formation of this detrimental oxide coating, applying a gold or platinum coating is recommended. Surface platinization of titanium creates a conductive and chemically stable coating that withstands regular electrolysis conditions. This coating extends the lifetime of the titanium, making it well-suited for applications requiring both high performance and long-term reliability. By preventing the formation of TiO2, stability in the electrochemical performance of the electrolyzer or intended electrochemical device is greatly enhanced, ensuring consistent and efficient operation over its lifespan.
What are the available sizes?
The titanium papers are offered in different sizes to suit different applications. The thicknesses available range from 0.25mm to 1.25mm. Additionally, our titanium fiber felts come in a variety of dimensions, with lengths and widths starting at 100x100mm and extending up to 1200x1200mm. This wide selection of sizes ensures that our titanium fiber felts can be tailored to fit specific project requirements, offering flexibility and adaptability for a diverse range of applications.
Frequently Asked Questions about Sintered Stainless Steel Fiber Felts
What are Sintered Stainless Steel Fiber Felts?
Sintered stainless steel fiber felts are non-woven filter media constructed from randomly laid short stainless steel fibers. These fibers are then sintered, or fused, together to form a porous and robust filtration material. These felts have fine and consistent pore sizes, excellent resistance to high temperatures, corrosion resistance, and are highly durable. They also exhibit low electrical heat resistance, making them suitable for filtration of hot materials and electrical applications.
What Thickness Options are There for Sintered Stainless Steel Fiber Felts?
These felts come in various thicknesses, typically ranging from 0.25mm to 1.2mm, providing versatility for different filtration applications. Stainless steel fiber felts can also be cleaned and reused, making them a cost-effective filtration solution in applications where sustainability is a concern.
What are the Applications of Sintered Stainless Steel Fiber Felts?
They are used in a wide range of applications, including purification of polymers and polyester melt, pre-filtration in ultrafiltration processes, filtration in refining operations, and electronic dust collection for high-temperature gases. They also find use in protection filters for vacuum pumps, support for filter membranes, and in various industrial applications.
Are These Felts Suitable for High-Pressure and High-Temperature Environments?
Yes, sintered stainless steel fiber felts are well-suited for applications operating under very high pressure, high temperature, and corrosive conditions due to their robust and corrosion-resistant nature. They offer finer and more consistent pore sizes compared to woven wire mesh, making them efficient in deep and sub-micron filtration. They are also highly durable, corrosion-resistant, and ideal for applications that require resistance to high temperatures
Frequently Asked Questions about Sintered Nickel Fiber Felts
Learn More
Sintered Fiber Felt as a Porous Metal Material
Porous metal materials, characterized by their porous structures, are innovative engineering materials that offer impressive strength while being light. These materials are used across different industries, including aerospace, metallurgy, mechanics, petrochemicals, energy, pharmaceuticals, architecture, and transportation. Their unique properties make them suitable for specialized applications, such as in life support systems, energy storage, hydrogen generation, and filtration systems.
Porous metal materials can be categorized into three types:
- Metal Foams. Metal foams are lightweight cellular structures composed of a solid base metal with gas-filled pores, inspired by natural materials like wood, bones, and sea sponges. This design gives metal foams high strength-to-weight ratios and excellent energy absorption properties, making them ideal for use in diverse industries such as aerospace and automotive applications.
- Sintered Metal Powder. Sintered metal powder is a porous material produced by sintering, a process wherein the metallic powder is compressed and then heated at temperatures below its melting point. Sintering causes the particles to bond into a solid piece with small pores. Typically, sintered metal powders have a high solid volume fraction, ranging from 0.35 to 0.65; thus, this type of porous material is commonly used in applications where good mechanical strength is required.
- Sintered Fiber Felts. Advancements in fiber-pullout techniques have led to the development of sintered metal fiber felt, a non-woven, porous material made of long metallic fibers typically over 1.5 µm in diameter. These fiber felts are used in structural applications, such as the core of sandwich panels, as well as in functional applications like anodic gas diffusion layers, catalyst supports, and filtration nets.
Manufacturing Sintered Metal Powders vs. Sintered Metal Fiber Felts
Unlike metal foams, which are typically created through a foaming process that introduces gas into metallic melts, sintered metal powders and fiber felts are formed by sintering compacted powders or laminated fibers, respectively.
Sintering is the key step in the production of both sintered metal powders and sintered metal fibers. It is a manufacturing process where metal raw materials are heated to high temperatures, just below their melting point. This causes the particles to fuse together, forming a solid mass. During sintering, several changes occur in the metal powder particles, improving various properties like strength, ductility, corrosion resistance, conductivity, and magnetic permeability. These changes are vital for different applications, as they determine the material's porosity, strength, and overall performance. Therefore, sintering plays a major role in achieving the properties needed for specific uses.
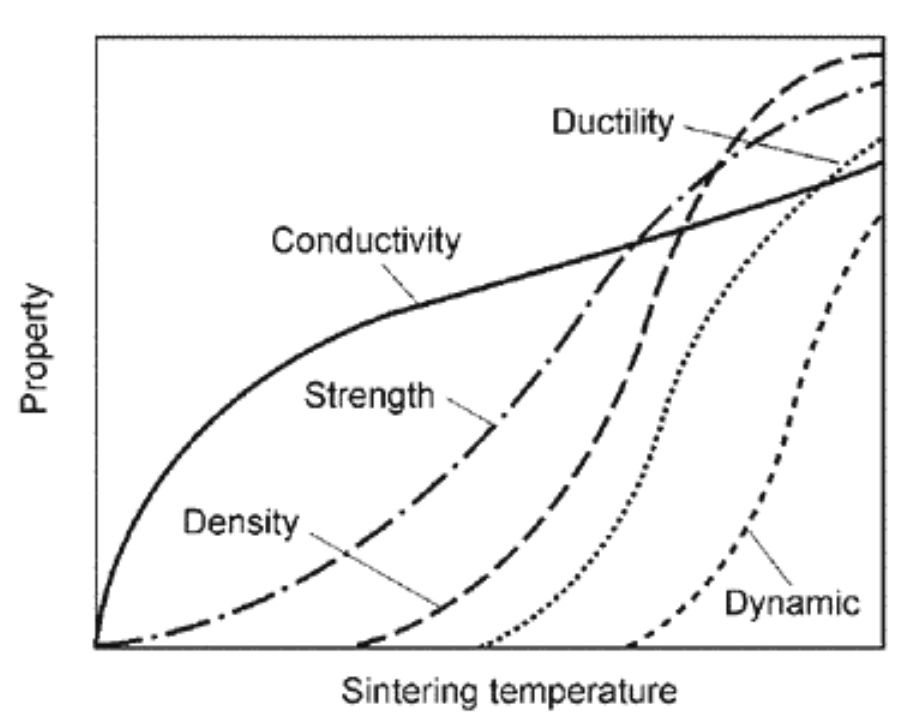
Reference: Samal, Prasan K. Newkirk, Joseph W.. (2015). ASM Handbook, Volume 07 - Powder Metallurgy (2015) - 34.2 Improved Mechanical Properties.(pp. 332). ASM International.
Sintering Mechanism in Metal Powders
The different sintering stages show how loose metal powders transform into a solid object:
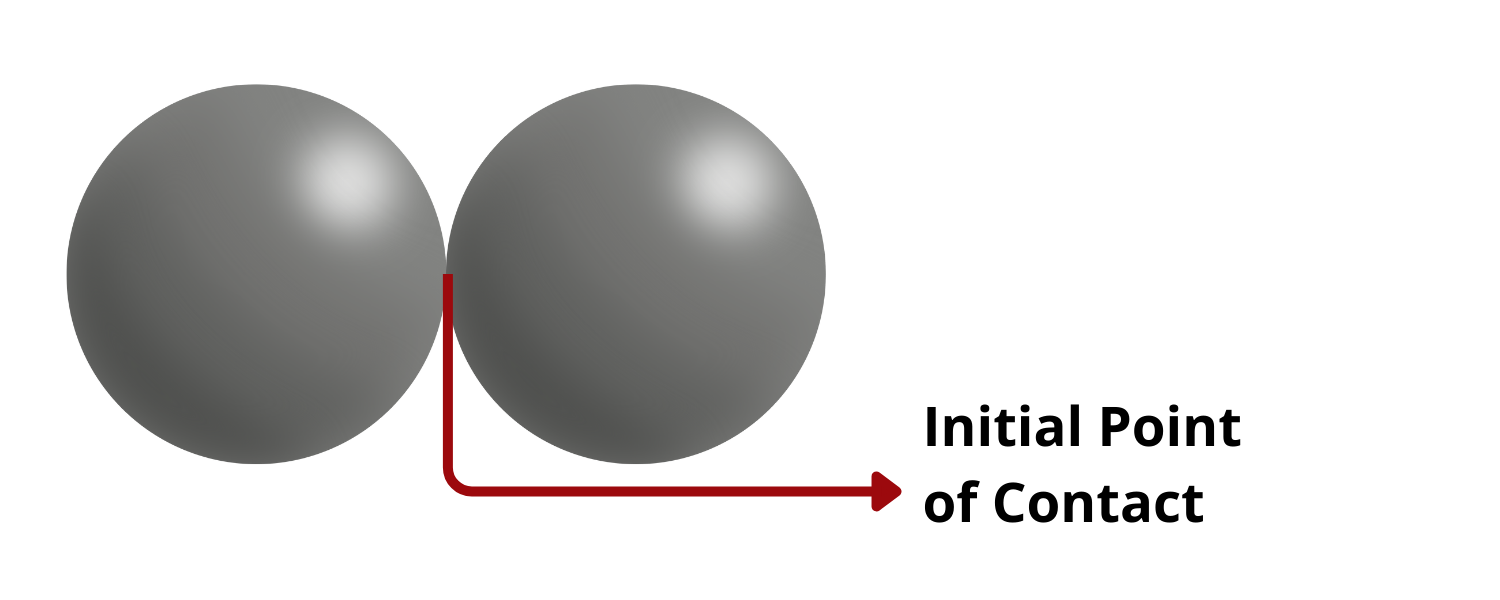
At the initial stage of sintering, particles start sticking together due to weak forces, like van der Waals' forces. At higher temperatures, they rearrange and pack together, sometimes rotating and twisting to achieve lower energy states in terms of their arrangement.
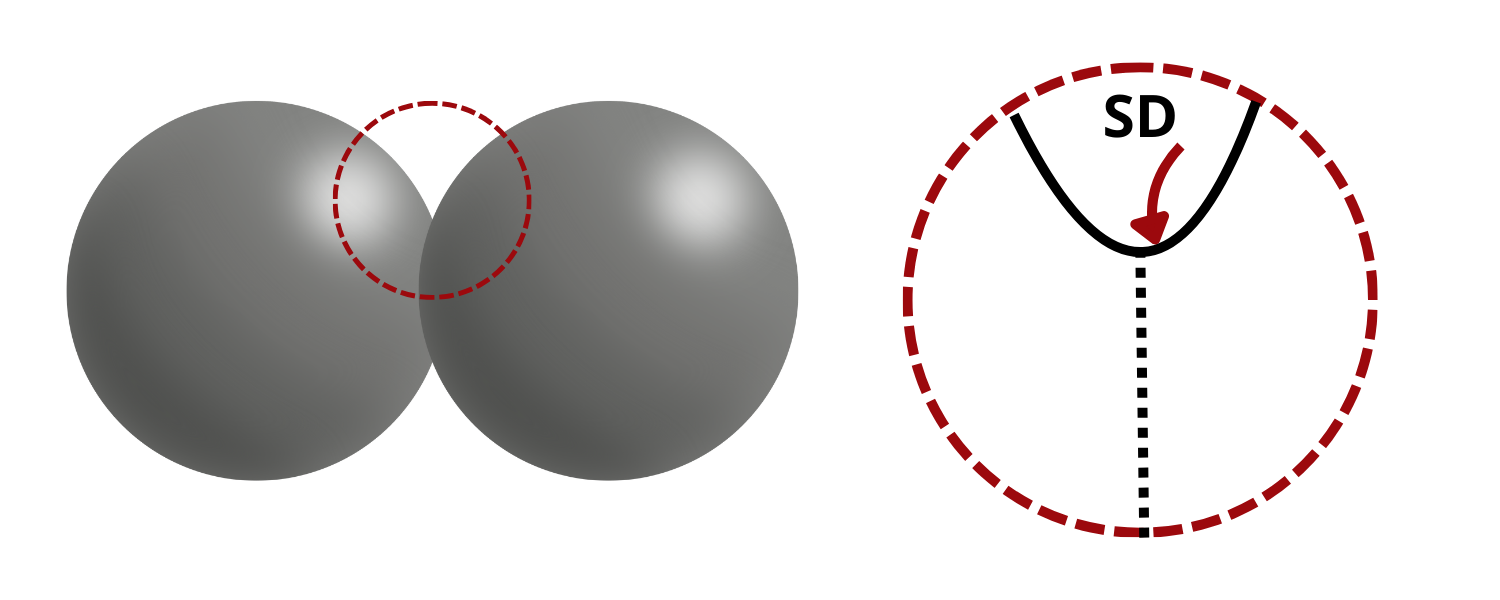
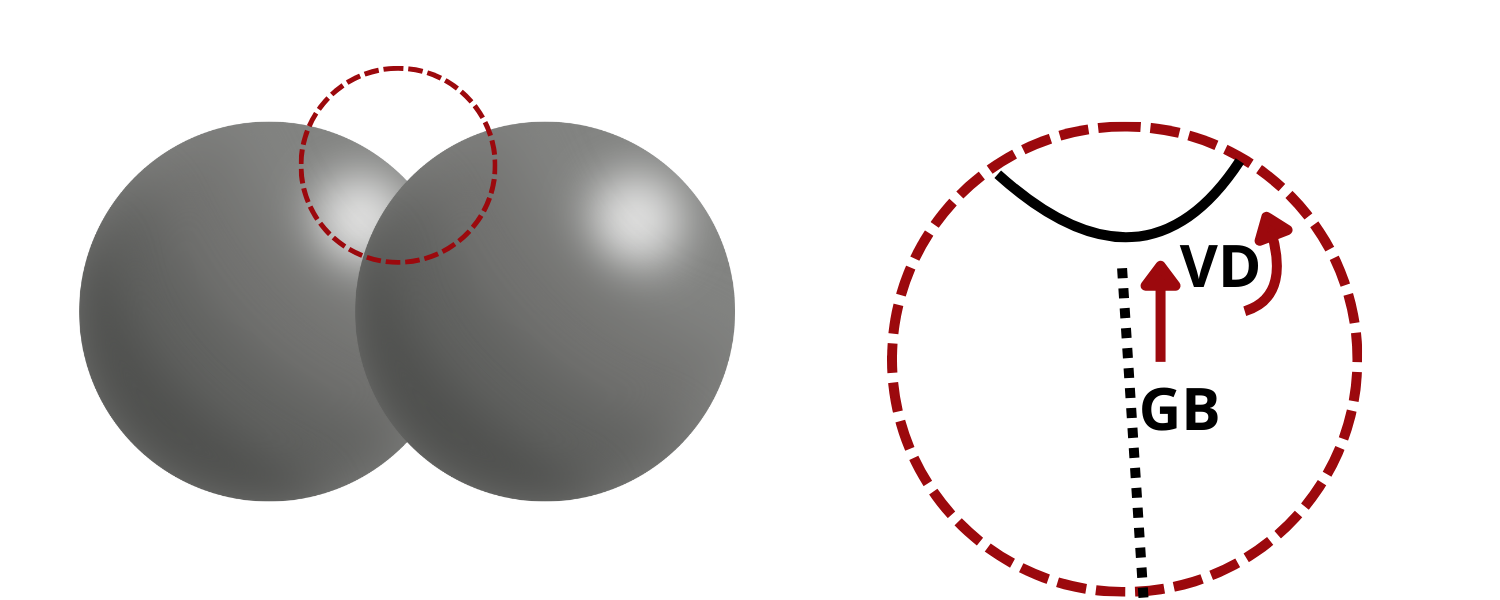
This stage is followed by the intermediate stage, where neck growth occurs, leading to densification. During this phase, the necks lose their distinct identities, and the pores become rounded but remain interconnected. At this point, the centers of the two spheres start to get closer, resulting in shrinkage. Bulk transport mechanisms predominate, facilitating neck growth and the elimination of pores.
In the final stage of sintering, interconnected open pores close and turn into isolated closed pores. As this happens, grain growth occurs, which slows down the surface and bulk diffusion processes. Consequently, this stage becomes the slowest, as densification increases from 95% to 99%.
(SD: Surface Diffusion, VD: Vacancy Diffusion, GB: Grain Boundary Diffusion)
Sintering Mechanism in Metal Fiber Felts
Throughout the sintering process of fiber felts, several transformations occur, such as the development of necks between fibers, the enlargement of grains within fibers, and changes in porosity. Similar to powder sintering, sintering of fiber metal felts involves six modes of material transport. Three of these modes lead to sintering without densification: vapor transport, surface diffusion, and lattice diffusion from the surface. Conversely, the other three modes lead to densification: boundary diffusion, lattice diffusion from the grain boundary, and lattice diffusion from dislocation.
To predict the sintering conditions necessary to achieve desired properties, sintering diagrams have been developed for different powders and wires. Originally, these diagrams were based on simple models, like the two-sphere model, which worked well for powders and wires. However, fiber felts, with their complex geometry, require a different approach.
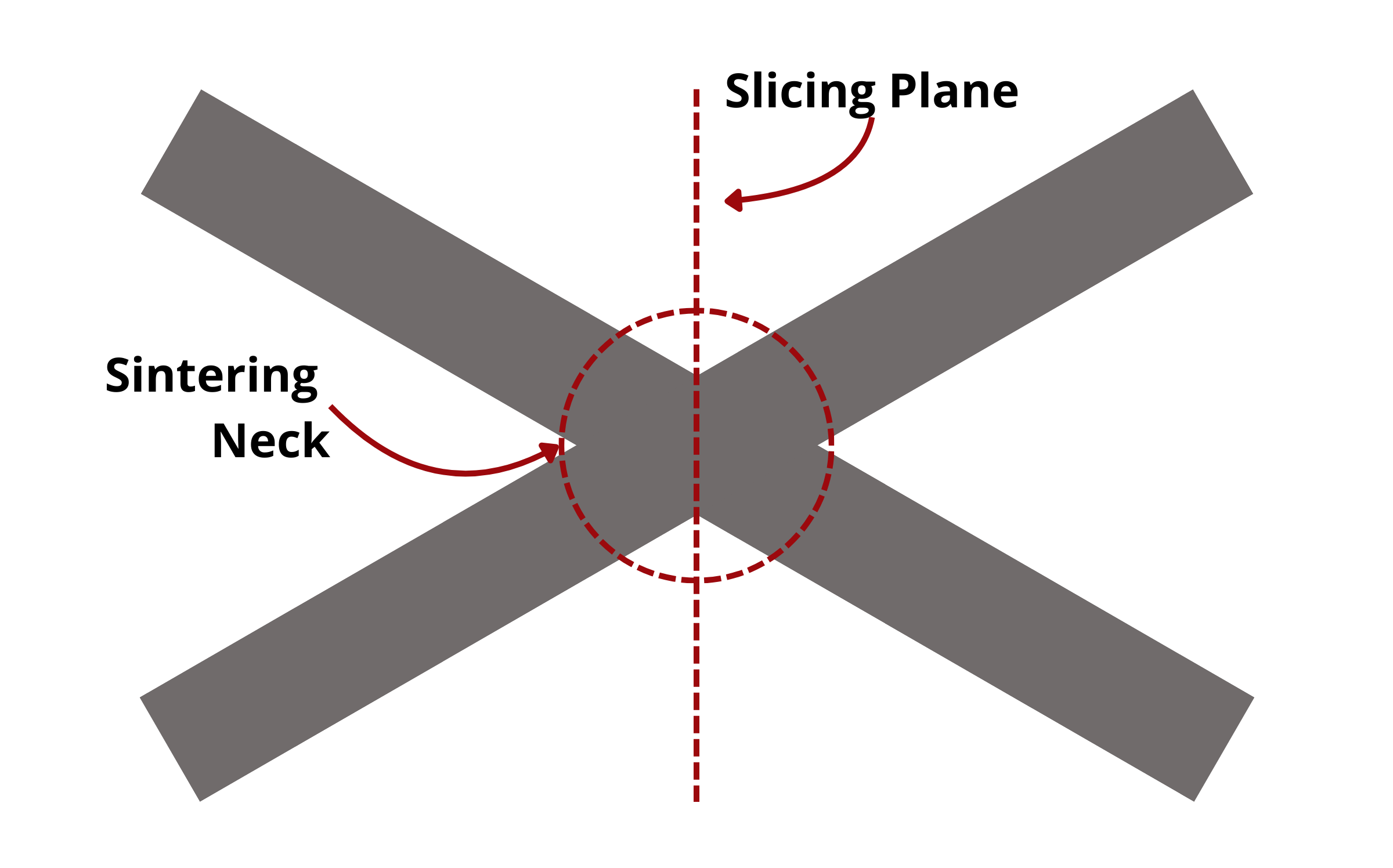
Unlike in powders, where sintering occurs between particles bonded by van der Waals forces, sintering in fiber felts takes place in the joints between adjacent fibers at random angles. During the pressing or shaping of fibers, sintering joints primarily develop at points where fibers make contact. Under pressure, fibers interlock, forming many contact areas. These contact regions can be categorized as either fiber-to-fiber contact joints or fiber-to-fiber mechanical meshing.
During sintering, material migrates in fiber-to-fiber contact joints or mechanical meshing to reduce surface energy. Initially, sintering begins on microstructures' surfaces, forming contact points between fibers, which then strengthen. This process continues across the fiber network, forming a mesh-like structure. In comparison to sintering powders, sintering metal fiber felts undergo less densification. This is because surface processes, grain growth, and neck growth mechanisms dominate over densification processes like grain boundary diffusion.
Contact Regions in Sintered Fiber Felts: Fiber-to-fiber (a) contact joints and (b) mechanical meshing
(Image Source: Tang, Y. et al. (2010) ‘An Innovative Fabrication Process of Porous Metal Fiber Sintered Felts with Three-Dimensional Reticulated Structure’, Materials and Manufacturing Processes, 25(7), pp. 565–571.)
Difference between Sintered Metal Powder and Sintered Metal Fiber Felt
Compared to sintered metal powder, sintered metal fiber felts are less dense, resulting in higher porosity and permeability. Sintered metal powders typically have porosities lower than 50%, whereas sintered metal fibers can achieve porosities higher than 50%. For instance, sintered titanium fiber felts can have porosities as high as 98%, with pore sizes smaller than 10 µm. Additionally, sintered metal fiber felts exhibit a three-dimensional reticulated structure. This structure not only provides well-defined conductive paths but also offers controlled electrical conductivity-temperature characteristics. The high porosity and decreased electrical resistivity due to the rupture of joint fiber contacts after sintering make sintered metal Fiber Felt an excellent material for applications such as water electrolyzers and fuel cells.
Scanning Electron Microscopy Images of Sintered Titanium (Left) Powder and (Right) Fiber Felt
(Image Source: Omrani, Reza & Shabani, Bahman. (2019). Gas Diffusion Layers in Fuel Cells and Electrolysers: A Novel Semi-Empirical Model to Predict Electrical Conductivity of Sintered Metal Fibres. Energies. 12. 855.)
Sintered Titanium Fiber Felts
Titanium fiber papers represent a specialized category of materials known for their unique properties and applications in various industries. These papers are composed of titanium fibers intricately woven together to form a porous and conductive structure. With their exceptional characteristics, titanium fiber papers find utility in diverse fields, ranging from electrochemical systems to filtration and aerospace applications.
Titanium fiber papers serve as versatile components in electrochemical systems, such as proton exchange membrane (PEM) electrolyzers and solid oxide electrolyzers. They function as critical elements in these devices, playing roles as gas diffusion layers, current collectors, and support structures. Their high electrical conductivity and corrosion resistance ensure efficient electron and ion transport, while the porous structure allows for effective gas diffusion, aiding in reactant distribution and facilitating electrolyte permeation.
Beyond electrochemical applications, titanium fiber papers find use in filtration processes, where their porous nature enables effective separation of particles and contaminants from fluids. They are often employed as filter media in industries such as pharmaceuticals, wastewater treatment, and air purification. Additionally, titanium fiber papers have gained traction in the aerospace sector for their lightweight yet strong characteristics, making them suitable for applications such as sound absorption, thermal management, and composite reinforcement.
Titanium fiber paper manufacturing process and properties
Titanium fiber paper is produced from titanium fibers through a laying process that involves lamination and lapping. The laminated titanium fibers are then sintered at high temperature, thereby creating a strong and porous three-dimensional fiber network. This three-dimensional structure endows titanium fiber papers with high surface area-to-volume ratio, high porosity, and high permeability. On top of these properties, titanium fiber papers are also known to be electrically conductive, workable (i.e., fiber papers can be rolled and processed), and highly resistant to corrosion and thermal stress.
Titanium fiber felt applications
Titanium fiber papers are used in a wide array of applications including aerospace, medical, military, and filtration. Recently, they have been employed as flow field and anodic distributors in fuel cell and electrolysis stacks.
Titanium fiber paper vs. carbon fiber paper
At the cathode side, carbon paper is the predominantly used porous transport layer. On the other hand, at the oxygen (anode) side of fuel cells, the environment is much more corrosive because of usage of pure oxygen and application of potentials as high as 2 V. The highly oxidative environment at the anode corrodes the carbon-based LGDLs, thereby forming CO2 (Eqn. 1) and carbonate ions (Eqn. 2) in acidic and basic media, respectively. Carbon corrosion drastically reduces the the activity and stability of the anode during galvanic or electrolytic operations. For these reasons, metal-based PTLs, specifically titanium fiber papers, are used at the anode of fuel cells and water electrolyzers.
| Carbon Fiber Paper | Titanium Fiber Paper |
Application | Cathode PTL | Anode PTL |
Advantages | High porosity and permeability | High electrical conductivity |
Disadvantages | Prone to corrosion at oxidative environments and high applied potentials | Prone to hydrogen embrittlement |
Titanium-based PTLs exhibit good corrosion resistance even when subjected to highly oxidative potentials. In the Pourbaix diagram of the titanium–water system, we can see that titanium forms a passivation layer under the operating conditions of PEM water electrolyzers. This layer prevents the direct contact between the titanium PTL and the corrosive electrolyte, thereby reducing the likelihood of corrosion. The passivation layer also stabilizes the titanium PTL surface and reduces the concentration of surface defects, which can serve as initiation sites for corrosive reactions. By minimizing the competing side reactions, the overall performance and durability of the electrochemical device improves substantially.
Titanium fiber paper as anode LGDLs in fuel cells and electrolyzers
As the anode GDL in fuel cells, titanium fiber papers serve as a porous media for the efficient and uniform delivery of gaseous reactants to the catalyst layer (CL). They also provide pathways that facilitate electron transport from the anode to the cathode, in which electrons are being used up during the reduction reaction. In addition to these, titanium GDLs also serve as water diffusion layers to avoid flooding and manage water build up in the anode of alkaline fuel cell stacks.