Assembly Film Adhesives
Assembly adhesives in film format are an increasing topic of interest. They have similar formulations to traditional die attach pastes and assembly pastes but they come in sheets with custom dimensions that can be applied directly on the die or substrate. These flat and even conductive and non conductive die attach films ensure perfect uniformity and a very controlled bond line thickness. Additionally, there’s minimal overflow during assembly and custom die-cut designs can also be produced.
Industry trends for electronic devices can be summarized as Miniaturization, High power dissipation, Higher reliability, Thinner devices. All these trends have certain drawbacks and challenges for die attach and assembly pastes. Miniaturiazation means that it is easier to contaminate the adjacent wirebond pads by flow and bleed from the adhesive. Higher reliability faces difficulties because of the difficult set-up and process maintenance that can lead to incomplete coverage, uneven fillet height, suck back, and other issues. In addition to that, the warpage of the die makes dies harder to stack, while contamination of the die surface from the adhesive is a possibility. Finally, thinner devices are prone to inconsistent fillets that can reduce reliability. The position accuracy is very important to avoid tilt while the contamination of the wire bonding pads by flow and bleed from the adhesive still lurks. All of the above problems can be resolved by assembly adhesives due to their controlled flow.
LOCTITE ABLESTIK 566K
- Extremely flexible film
- Bond disimilar materials
- Thermally conductive
- 8 - 12 weeks
LOCTITE ABLESTIK 5025E
- Thin, uniform bondline control
- Electrically conductive in x,y,z axes
- Excellent electrical and thermal conductivity
- 8 - 12 weeks
LOCTITE ABLESTIK ECF 563
- Electrically conductive
- Thin uniform bondline control
- Passes NASA ougassing
- 8 - 12 weeks
LOCTITE ABLESTIK ECF 564A
- Electrically conductive
- Excellent thermal conductivity
- Passes Mil 5011 and NASA outgassing
- 8 - 12 weeks
LOCTITE ABLESTIK ECF 564AHF
- High flow version of 564A
- Excellent thermal conductivity
- Passes Mil 5011 and NASA outgassing
- 8 - 12 weeks
ITO-125 | 125 μm Indium Tin Oxide film
- 85% Light transmittance
- 125um thickness
- Ease of processing
- 6 - 8 weeks
ITO-175 | 175 μm Indium Tin Oxide film
- 85% Light transmittance
- 175um thickness
- Ease of processing
- 6 - 8 weeks
Product Selector Guide
Product | CVCM (%) | TML (%) | TC(W/mK) | Resistivity (Ohms*cm) | Glass transition temperature (°C) | CTE a1 | CTE a2 | Recommended cure | Attributes |
---|---|---|---|---|---|---|---|---|---|
LOCTITE ABLESTIK 5025E | 0.06 | 0.3 | 6.5 | 5x10-4 | 90 | 65 | 150 | 30min @150°C | Hot devices and PC on heatsinks. NASA |
LOCTITE ABLESTIK CF3350 | 0.03 | 0.16 | 7 | 2x10-4 | 90 | 65 | 150 | 30min @150°C | PC, Backplanes, Heatsinks on fluoropolymer, ceramic, copper, kovar, Al |
LOCTITE ABLESTIK ECF563 | 0.02 | 0.21 | 1 | 1x10-3 | 88 | 60 | 250 | 30min @150°C | RF/EMI shielding. Microwave substrate in packages |
LOCTITE ABLESTIK ECF564A | 0.01 | 0.3 | 2.2 | 4x10-4 | 150 | 30 | - | 2hours@150°C | Ultra low outgassing. MIL |
LOCTITE ABLESTIK ECF564AHF | 0.01 | 0.3 | 3 | 4x10-4 | 122 | 80 | 330 | 2hours@150°C | High flow version of 564A |
Product | CVCM (%) | TML (%) | TC(W/mK) | Resistivity (Ohms*cm) | Glass transition temperature (°C) | CTE a1 | CTE a2 | Recommended cure | Attributes |
---|---|---|---|---|---|---|---|---|---|
LOCTITE ABLESTIK 5020 | 0.01 | 0.4 | 0.2 | 5x1014 | 100 | 60 | 200 | 1hour @150°C | Substrate attach. Seal packages. NASA |
LOCTITE ABLESTIK 5020K | 0.02 | 0.24 | 0.7 | 8X1015 | 109 | 45 | 270 | 1hour @150°C | Higher purity 5020 |
LOCTITE ABLESTIK 550K | - | - | 0.8 | 7.2x1012 | 102 | 50 | 300 | 30min @150°C | Heat sink bonding |
LOCTITE ABLESTIK 561 | - | - | 0.3 | 5x1012 | 50 | 85 | 300 | 30min @150°C | For mismatched CTEs |
LOCTITE ABLESTIK 561K | - | - | 0.9 | 9.1X1012 | 55 | 85 | 300 | 30min @150°C | Reworkable. NASA |
LOCTITE ABLESTIK 563K | 0.04 | 0.44 | 1.1 | - | 97 | 45 | 300 | 30min @150°C | Hot devices on heatsinks |
LOCTITE ABLESTIK 564A | 0.01 | 0.3 | 0.3 | 2x1015 | 140 | 35 | 15 | 2hours @150°C | High purity. Bond hybrid substrates |
LOCTITE ABLESTIK 566K | - | - | 0.8 | 1.4x1013 | 93 | 85 | 300 | 2hours @100°C | Low temp cure |
LOCTITE ABLESTIK 570K | - | - | 0.7 | 6x1014 | 135 | 50 | 35 | 3hours @150°C | High purity. Adhesion to Gold. Reliable |
Product | Adhesive | Adhesive thickness (µm) | Adhesion strength (Oz/in) | Operating temperature (°C) | Visible light transmission | Attributes |
---|---|---|---|---|---|---|
ITO-125 | - | - | - | - | >85% | - |
ITO-175 | - | - | - | - | >85% | - |
OCA | Acrylic | 10 | 70 | -40 ~ +110 | >92% | - |
Frequently Asked Questions
How does environmental exposure affect Assembly films for RF grounding?
Optimization of the cure schedule showed that improved performance was achieved after the use of increased temperature during cure. Exposure to high-temperature storage was shown to provide more stable temperature dependant adhesion strength.
Generally, the films maintain relatively good levels of temperature-dependent adhesion strength after 250 hrs of high-temperature exposure over the range of temperatures tested. Prolonged moisture soak (85ºC/85%RH) exposure was shown to have a minor effect in regards to mechanical and electrical performance. This suggests that for applications requiring both good resistance to high temperatures and moisture-rich environments, films may offer good performance. Read more in this paper.
What are the benefits of assembly films?
With increasing functionality and power requirements for electronic equipment, the need for thermal management is critical. The demand for uniformed bondline application as well as the avoidance of air inclusions across large areas make epoxy film adhesives essential for many applications in the aerospace, telecommunications, and electronics fields. Luckily, assembly films not only provide best-in-class electrical, thermal, and mechanical performance, but also lower total assembly costs through the elimination of inventory maintenance and/or third-party conversion.
Assembly films provide a proven solution for the most demanding applications requiring the highest reliability performance. Henkel’s epoxy film adhesives are perfectly suited for large bonding areas that also require uniformed bondlines and custom sizes and shapes. For this reason, we provide customized film preforms to precisely match highly-complexhighly complex printed circuit board shapes and patterns. This ensures an exact amount of void-free adhesive with a controlled bondline thickness in a specific area. We offer heat activated film adhesives that help reduce curing time and increase the efficiency of your work processes.
Learn More
Assembly films for controlled flow
Assembly films - Application notes and Handling guide
Henkel epoxy based film products are designed for use in a variety of PCB or hybrid applications. This includes such applications as basic heatsink attach, die attach, coining, and grounding for gigahertz frequency RF parts. All Henkel film products are prepared into a dry “B-staged” state where they can be easily handled with minimal need for tools or equipment. Products are available in three basic categories: Electrically Conductive, Thermally Enhanced, or Non-Filled films. Electrically Conductive Films: Conductive films are specially designed to maximize electrical conductivity while giving a variety of other options such as: low temperature cure, high flexibility, superior adhesion, and/or high thermal stability. LOCTITE® ABLESTIK CF 3350, the core product in this line, combines high conductivity and flexibility with superb adhesion and homogeneity to make it an excellent choice for most mid or high-end applications.
Electrically Conductive Films: Conductive films are specially designed to maximize electrical conductivity while giving a variety of other options such as: low temperature cure, high flexibility, superior adhesion, and/or high thermal stability. LOCTITE® ABLESTIK CF 3350, the core product in this line, combines high conductivity and flexibility with superb adhesion and homogeneity to make it an excellent choice for most mid or high-end applications. Thermally Enhanced Films: Henkel
Thermally Enhanced Film products offer the perfect blend of high thermal conductivity with varying degrees of flexibility and adhesion specially formulated for heatsinking or thermal dissipation applications.
Non-Filled Films: Non-Filled Film Products may be used for various applications including electrical isolation, liquid crystal displays, solvent resistant bonding, or basic substrate assembly.
Application Techniques
Substrates: Film products provide excellent adhesion to a large variety of substrate materials, including most metals, ceramics, and PWB materials.
Cutting and Custom Preforms: For most applications, the most convenient and cost-effective cutting solution is to obtain die cut preforms prepared directly from customer supplied CAD drawings. For prototype or low volume applications, cutting sheet stock with a razor blade or scissors may suffice. Tacky films may require that the release liner be left on for this step. For larger volume applications, selected products are available in reel format for in-situ cutting as part of the assembly process.
Cleaning & Handling: Product is ready to use upon removal of polyester or silicone paper release liners, and green plastic interleaf layers. While cleaning of substrates is not mandatory, an organic solvent wipe is recommended to remove any oils that might interfere with the bonding process or electrical interface. Plasma cleaning is also recommended, though it may enhance film flow. Substrates and film product may easily be assembled by hand as desired. While not required, the use of gloves is recommended to reduce the chance of contamination.
Storage & Handling: All film products have a recommended set of storage conditions. Check the Technical Data Sheet for conditions specific to each product. Most films recommend storage from - 40 to 0°C. It is best to leave sheets or preforms bagged until use. Thawing time varies depending on quantity of film removed, but may be as little as a few minutes for a single sheet. Once thawed, it is not recommended to restore back to the freezer.
Pre-Tacking: In some small area applications such as die attach, it may be desirable to pre-tack the substrates into place. Most products will develop a moderate amount of tack when heated to temperatures in the range of 40 – 60°C. After preheating one substrate to this temperature, the film may be gently applied and tacked into place by either sandwiching it between the release Liner and substrate, or between both substrates being attached*. From here, parts may be cooled to room temperature before exposing to the final cure profile. It is possible to cure very small parts without applied pressure if they are adequately pre-tacked.
Cleaning & Handling: Product is ready to use upon removal of polyester or silicone paper release liners, and green plastic interleaf layers. While cleaning of substrates is not mandatory, an organic solvent wipe is recommended to remove any oils that might interfere with the bonding process or electrical interface. Plasma cleaning is also recommended, though it may enhance film flow. Substrates and film product may easily be assembled by hand as desired. While not required, the use of gloves is recommended to reduce the chance of contamination.
Storage & Handling: All film products have a recommended set of storage conditions. Check the Technical Data Sheet for conditions specific to each product. Most films recommend storage from - 40 to 0°C. It is best to leave sheets or preforms bagged until use. Thawing time varies depending on quantity of film removed, but may be as little as a few minutes for a single sheet. Once thawed, it is not recommended to restore back to the freezer.
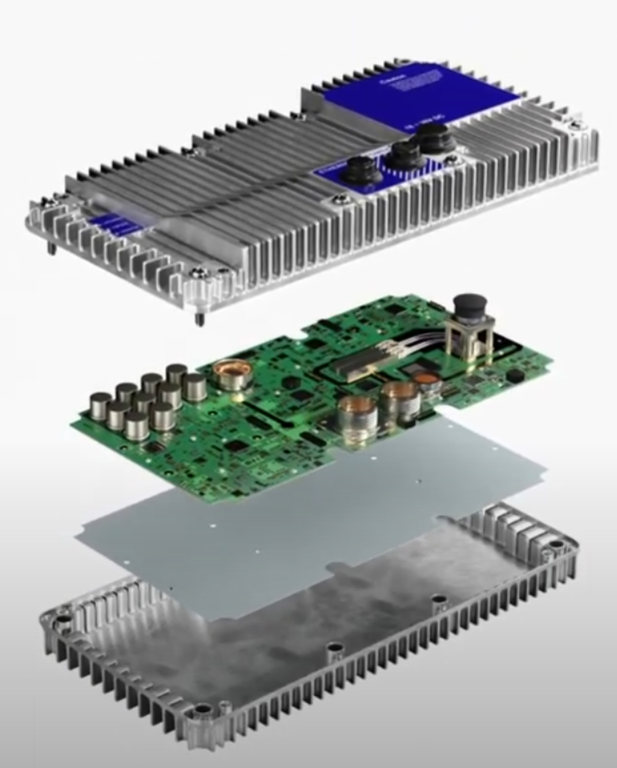
Pre-Tacking: In some small area applications such as die attach, it may be desirable to pre-tack the substrates into place. Most products will develop a moderate amount of tack when heated to temperatures in the range of 40 – 60°C. After preheating one substrate to this temperature, the film may be gently applied and tacked into place by either sandwiching it between the release Liner and substrate, or between both substrates being attached*. From here, parts may be cooled to room temperature before exposing to the final cure profile. It is possible to cure very small parts without applied pressure if they are adequately pre-tacked.
Curing
Time & Temperature: All products have at least one recommended cure profile as listed on the Technical Data Sheet for that product. It is highly recommended to stay to these conditions as curing at different temperatures may cause the film to wet the substrate poorly, or possibly not fully cure. If a different cure temperature is needed, consult customer support for possible advice on this or consider an alternative product that will better fit the application. Most products list cure profiles at 150°C with an alternative cure at 125°C. It is also important to note that cure times are listed as a minimum temperature exposure at the bondline. Larger metal parts may take a significant amount of time to reach peak temperature and will therefore need longer to bond properly. Most products may be safely cured for times longer than needed with negligible adverse effects.
Cure Pressure: Adequate pressure is needed to ensure that the film fully wets substrate surfaces during the cure profile. The following chart gives recommended** cure pressures for most major products.
Troubleshooting
Pressure Application: Films need applied pressure during cure to promote proper wetting of substrate surfaces. Henkel recommends the use of spring clamps, lamination presses, or vacuum bagging to achieve even and predictable pressure during the cure process. No matter what method is used, it is important to evenly distribute pressure over the entire contact area to ensure even wetting and a uniform bondline. Conformable pads such as silicone rubber may be used to help distribute pressure. Screw clamps are not generally recommended. Weights are effective for small parts but become cumbersome for larger boards.
Vacuum Cure Option: Vacuum bag or Vacuum lamination press curing may be beneficial for some applications. Curing under vacuum can significantly reduce the risk of entrapping air in the bondline, thus helping to ensure the best thermal and/or electrical properties attainable. Less pressure may be required, as curing under a vacuum has been known to increase flow and substrate wet-out.
Controlling Flow: In the case of excessive resin flow or bleed, try one of the following alternatives:
- Use a lower cure pressure
- Have preforms made with edge cutback
- Use a faster oven ramp rate
Poor Electrical Contact: In the case of poor electrical contact or grounding, an acoustic scan can verify if bonding is poor. If a poor interface is suspected, try these alteration to the cure profile:
- Use a higher cure pressure
- Use vacuum cure to prevent entrapped air
- Ensure even distribution of pressure to eliminate any pinching or areas of low compression.
If after adjusting, grounding requirements are still not met, it may be necessary to try a more conductive product. Films without a fiberglass support, such as LOCTITE® ABLESTIK CF 3350 or LOCTITE® ABLESTIK 5025E, are generally more conductive.
Exposing to Solder Reflow: While exposing a cured application to solder reflow temperatures is not generally recommended, it is often necessary. In these situations, please follow the guidelines listed below for the best outcome. The following chart lists products that show minimal degradation at listed peak temperatures. Exposure time is expected to be around 30 seconds. Products may withstand higher temp exposures if the duration is kept short.
Temperature Range | Products |
Low (Below 200°C) | 561, 561K, 566, 566K, 5662, 506, ECF561, ECF561E |
Mid (Up to 230°C) | 563K, ECF563, CF3350, 5025E, CF3352 |
High (Up to 270°C) | ECF568, 550K, CF3366 |
Exposing film to solder reflow temperatures may result in weakening of the bond an/or reduction in electrical and thermal conductivity. Slower ramp rates may help reduce complications as will the use of smaller boards.
High Frequency Applications: Proper grounding for high frequency RF applications may require special film characteristics. For this type of application, LOCTITE® ABLESTIK CF 3350 or LOCTITE® ABLESTIK 5025E are highly recommended for their uniformity and high conductivities.
Common Applications for Assembly adhesive films
High-reliability film adhesive solutions for aerospace electronics in planes, helicopters, and unmanned aerial vehicles (UAVs) including engines, turbines, sensors, guidance systems, and navigation systems.
Proven and trusted epoxy film adhesive solutions supporting high-reliability radar and sonar assemblies including antennas, phase shifters, T/R modules, power modules, transmitters, and sensors.
High-reliability film adhesives supporting satellite assembly including directed energy, communication, guidance, navigation, and control systems.
Optically clear assembly films
CAPLINQ's ITO (Indium Tin Oxide) film and OCA (Optically Clear Adhesive) are designed for use in a variety of optically clear applications. ITO and OCA films are a critical part for modern electronic devices, providing transparent and conductive solutions.
Indium Tin Oxide films: ITO conductive film, constructed on a PET substrate, is formulated by depositing Indium Tin Oxide with the rare metal Indium as the primary raw material onto a PET film. Functioning as an n-type semiconductor material, ITO conductive film exhibits a remarkable combination of high self-carrier concentration (low resistivity), wide band gap, and superior light transmittance within the visible spectral region. This unique set of properties makes ITO conductive film indispensable in numerous applications, prominently in flat panel display devices and solar cells.
Optically Clear Adhesive films: Optically Clear Adhesive serves as a specialized bonding agent for transparent optical components like touchscreens and lenses. This adhesive is designed to meet specific criteria, including transparency, a light transmittance exceeding 90%, robust bonding strength, room-temperature or medium-temperature curing, and minimal curing shrinkage. OCA is a fundamental raw material for touch screens, particularly as a double-sided adhesive tape with matrix-free material. The matrix-free construction involves transforming acrylic glue into a matrix-free form and subsequently attaching a release film to the upper and lower layers. Notably, optically clear adhesive is categorized into resistive OCA and capacitive OCA, each tailored for specific applications.
Common Applications for Optically Clear Assembly Adhesive Films
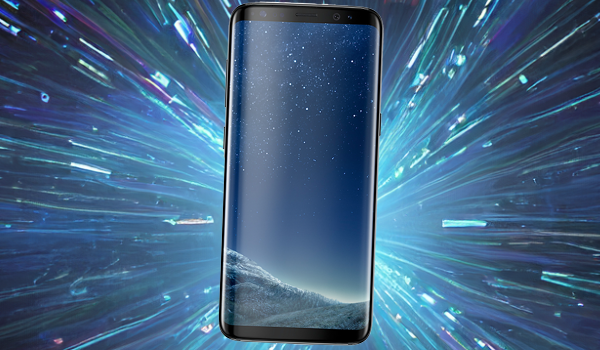
ITO conductive film's exceptional conductivity and transparency make it a cornerstone in the manufacturing of high-quality displays for devices like smartphones, tablets, and monitors.
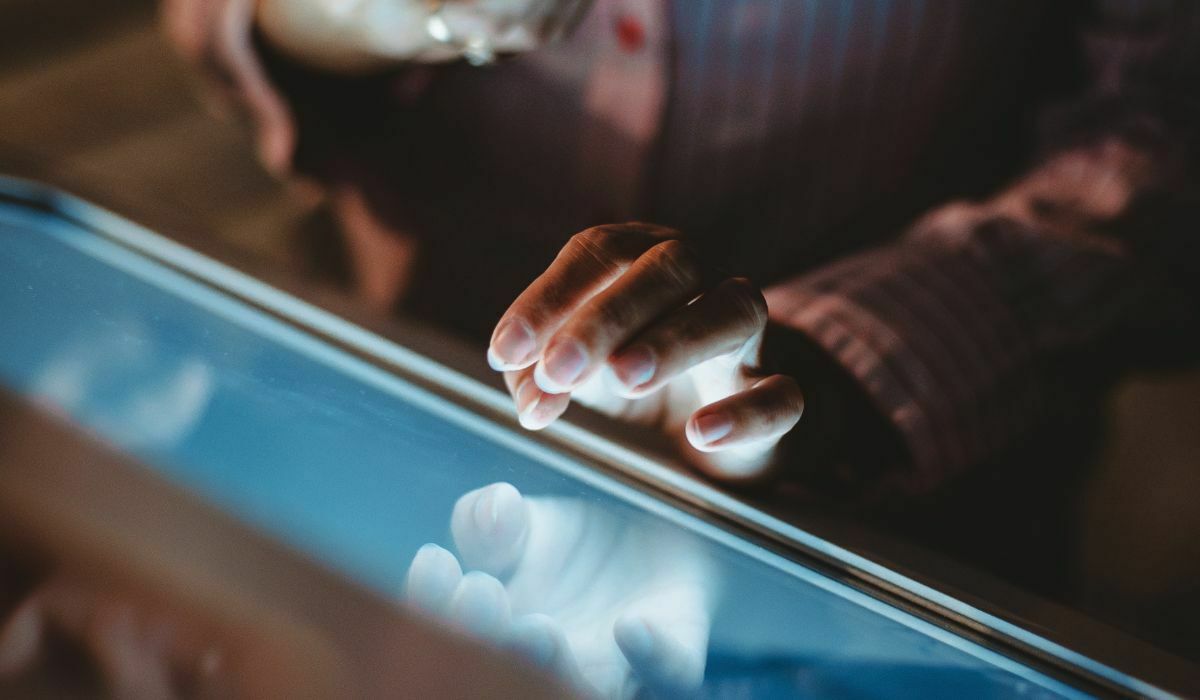
OCA, as a critical component in touchscreens, ensures seamless bonding of transparent layers, enabling responsive and clear touch functionality.
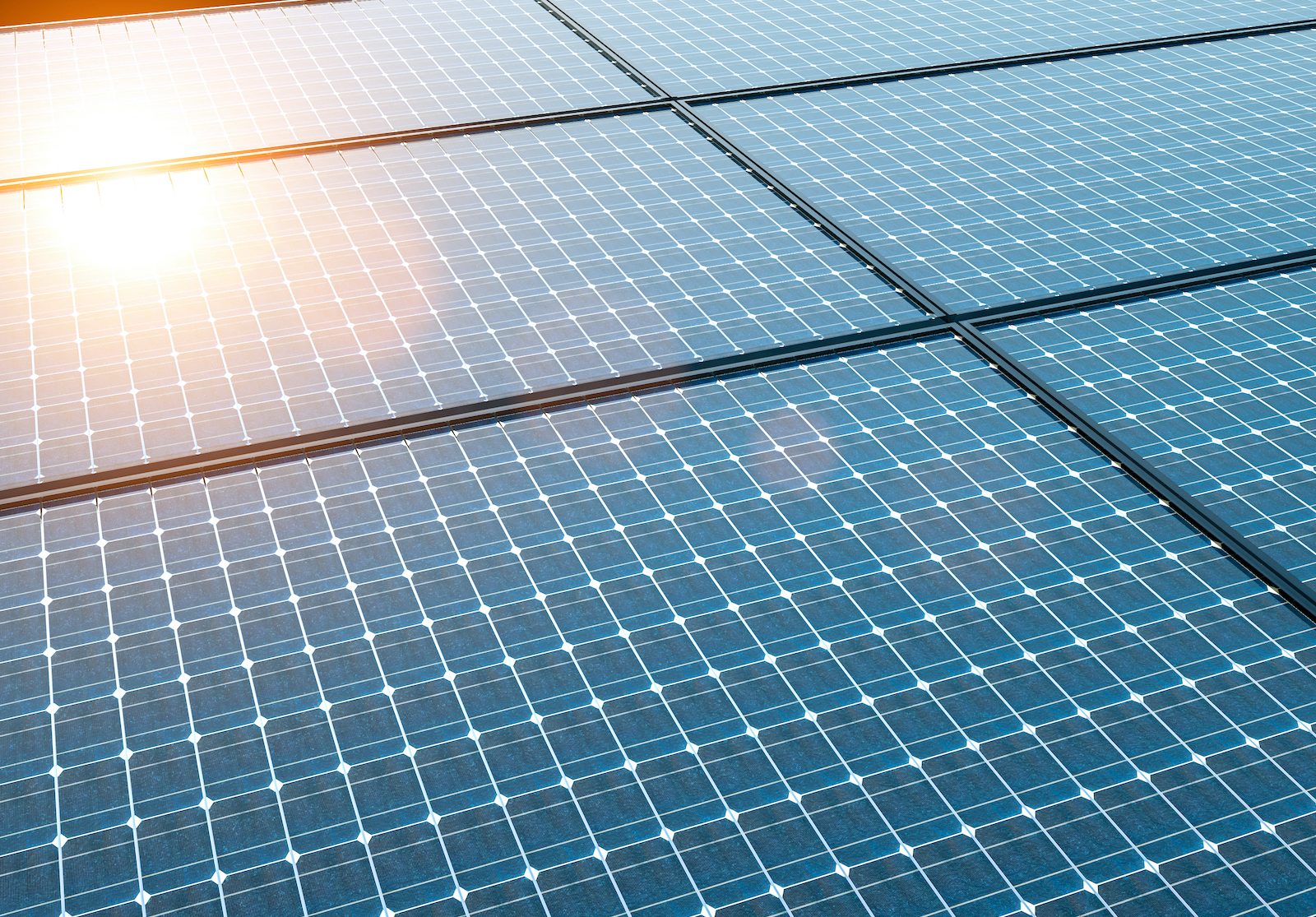
The utilization of ITO conductive film in solar cells contributes to efficient light transmittance and electrical conductivity, enhancing the overall performance of solar energy conversion.