Solder Pastes
Solder paste is a mixture of powdered solder and a flux, used in surface mount technology (SMT) to create electrical connections between components and a printed circuit board (PCB). The flux helps to clean and protect the metal surfaces during soldering, while the solder powder melts and creates a bond between the components and the board. It is applied on a PCB with the help of a stencil or a foil. The stencil accurately deposits the right amount of paste on the surface mount pads. It should be properly aligned on the circuit board. Solder paste application is one of the most important aspects of component mount process in PCB assembly.
At Caplinq, we understand the importance of reliable electrical connections in today's demanding electronics landscape. That's why we're proud to offer a comprehensive selection of best-in-class solder pastes, meticulously formulated to deliver exceptional performance and unwavering reliability. Solder paste is the cornerstone of surface mount technology (SMT), creating the critical electrical and mechanical connections between electronic components and printed circuit boards (PCBs).
Experience optimal printability with our precisely formulated pastes, featuring tailored viscosities and particle sizes for consistent, high-definition deposits. Achieve robust and reliable solder joints with our pastes' exceptional wetting characteristics, ensuring maximum contact area and electrical conductivity. Benefit from long-lasting performance with our high-quality alloys and advanced flux technology, delivering resilience in even the most demanding applications. Enjoy streamlined processes with our diverse range of solder paste options, including no-clean and clean formulations to optimize your production efficiency. Ready to elevate your SMT experience? Explore Caplinq's range of best-in-class solder pastes and discover the difference that comes with partnering with an adhesive expert.
LINQALLOY SP-Bi57Sn42Ag1 | Solder paste
- Sn42Bi57Ag1 Alloy
- 138°C Eutectic
- Powder size: T3 (25-45um) and T4 (20-38um)
- 8 - 12 weeks
LINQALLOY SP-SAC105 | Solder paste
- Pb-free Sn98.5–Ag1–Cu0.5 alloy
- Solder paste for surface mount technology
- RoHS compliant
- 6 - 8 weeks
LINQALLOY SP-PSA525 | No Clean Solder Paste
- Superior wetting
- Reliable clog-free dispensing
- High thermal fatigue resistance for power semiconductor applications
- 8 - 12 weeks
LINQALLOY SP-SAC305 | Solder paste
- Sn96.5Ag3.0Cu0.5
- 217°C Eutectic
- Powder size: T3 and T4
- 8 - 12 weeks
LINQALLOY SP-SAC307 | Solder paste
- Sn99Ag0.3Cu0.7 Alloy
- 217 - 228°C
- Powder size: T3, T4 and T5
- 6 - 8 weeks
LOCTITE HF 250DP
- 95.5%Sn: 3.8%Ag:0.7%Cu - 96SC Alloy
- Lead free Soldering
- Suitable for reflow in nitrogen
- 8 - 12 weeks
LOCTITE DA 100
- Sn91.5/Sb8.5 - Pb free 92A Alloy
- Semiconductor die attach
- Excellent dispense capabilities
- No longer available
Product Selector Guide
Product | Description | Alloy | Particle size distribution | Viscosity (mPA.s) | Melting temperature | Shelf life |
---|---|---|---|---|---|---|
Dispensable | ||||||
DA 100 | Tin antimony, dispense solder paste for Die attach | 92A | Type 4 | 300,000 | 242°C | 12 months at -20°C |
GC 50 | Room temp stable, Jet dispensable and fine particle paste for small components | SAC305 | Type 5 | 110,000 | 217°C | 180 days in RT |
Printable | ||||||
Loctite GC 10 | Room temp stable, Multi purpose solder paste for PCB assembly | SAC305 | Type 3, 4, 5 | 200,000 | 217°C | 12 months in RT |
Loctite GC 18 | Room temp stable, low voiding paste for large area components such as QFN with heat sink. | SAC305 | Type 4 | 250,000 | 217°C | 180 days in RT |
Loctite HF 212 | Refrigerated, Halogen-free, solder paste for PCB assembly | 90iSC 97SC | Type 4 | 175,000 | 205 - 218°C | 180 days at 0°C - 10°C |
Loctite LF 318 | Refrigerated, High reliability solder paste for PCB assembly. Both printable and dispensable versions. | 90iSC | Type 3 | 650,000 | 205 - 218°C | 180 days at 0°C - 10°C |
Product | Description | Alloy | Particle size distribution | Viscosity (mPA.s) | Melting temperature | Shelf life |
---|---|---|---|---|---|---|
LINQALLOY Sn42Bi57Ag1 | Low eutectic solder paste for LED Assembly | Sn42Bi57Ag1 | Type 3, 4 | - | 138°C | 6 months at 5°C |
LINQALLOY SP-SAC105 | Pb-free solder paste designed for Surface Mount Technology (SMT) | SAC105 | Type 3, 4, 5 | 200 | 223°C | 6 months at 5°C |
LINQALLOY SP-PSA525 | High lead solder paste designed for clog-free dispensing die attach processes | Pb92.5Sn5Ag2.5 | Type 3, 4, 5 | 130 - 170 | 287°C | 6 months at 5°C |
LINQALLOY SP-SAC305 | Pb-free solder paste designed for Surface Mount Technology (SMT) | SAC305 | Type 3, 4 | 160 - 230 | 217°C | 6 months at 5°C |
LINQALLOY SP-SAC307 | Pb-free solder paste designed for Surface Mount Technology (SMT) | SAC307 | Type 3, 4, 5 | 190 - 230 | 220°C | 6 months at 5°C |
Frequently Asked Questions
Frequently asked questions about Soldering Materials
What is Solder Paste Reflow?
Solder paste reflow is the process of heating the PCB with the applied solder paste to melt the solder and create electrical connections between the components and the PCB. The reflow profile, which includes the temperature ramp-up, dwell time, and cooling rate, is crucial for achieving good solder joint quality.
What is the difference between IR reflow and conventional reflow?
Both conventional oven reflow and infrared (IR) reflow are common methods for soldering surface mount components (SMCs) to printed circuit boards (PCBs). Conventional ovens use hot air to heat the board, while IR reflow uses infrared radiation. Conventional ovens are cheaper, widely available, and suitable for various PCB sizes and component densities, but they can be slower and have uneven heating. IR reflow offers faster heating, more uniform temperatures, and less thermal shock to components, but it's generally more expensive.
What is Solder Paste Printing?
Solder paste printing is the process of applying solder paste to a PCB using a stencil and a squeegee. The squeegee applies pressure to the paste, forcing it through the openings in the stencil onto the PCB pads. The stencil's thickness and the openings' size and shape are critical factors in achieving consistent and precise solder paste placement. The printing process is critical for achieving consistent and accurate solder paste placement.
What is the Role of Flux Activity in Solder Paste?
Flux activity refers to the chemical reactivity of the flux in the paste. A more active flux can clean surfaces more effectively but may also be more corrosive. The choice of flux activity depends on the specific application and the materials being soldered.
Do the flux residue need to be removed?
The need to remove flux residue after an SMT process depends on the type of flux used.
No-clean flux: These fluxes are designed to leave a non-corrosive residue that does not require cleaning. They are often preferred in applications where cleaning can be time-consuming or introduce contamination risks.
Water-soluble flux: These fluxes require cleaning with water or a water-based cleaning solution to remove the residue. They are often used when the residue could potentially cause corrosion or interfere with subsequent processes.
Solvent-soluble flux: These fluxes require cleaning with a solvent-based cleaning solution. They are less commonly used due to environmental concerns and the potential for solvent residues to remain on the PCB.
How Does Particle Size Affect Solder Paste?
Particle size refers to the average diameter of the solder powder particles in the paste. Smaller particles can provide finer detail and better wetting, but they may also be more susceptible to oxidation and require more careful handling. Larger particles, on the other hand, can be easier to handle but may not provide the same level of detail.
What is the Viscosity of Solder Paste?
Viscosity measures the resistance of a fluid to flow. In solder paste, it's a crucial property that affects how the paste spreads and flows during application through the stencil apertures. Higher viscosity pastes are thicker and may require more pressure to apply, while lower viscosity pastes are thinner and flow more easily. The viscosity range of printing solder paste is about 100-200Pa.s, which is required to adjust for different scenarios.
What is Solder Paste Inspection (SPI)?
Solder paste inspection is the process of examining the applied solder paste for defects such as voids, bridging, and insufficient volume. Visual inspection and automated optical inspection (AOI) are common methods for solder paste inspection. Refer to the full PCB Assembly Process Flow to understand more about the solder paste inspection.
How Does Solder Paste Temperature Affect Solder Joint Quality?
The temperature at which the solder paste is reflowed is critical for achieving good solder joint quality. If the temperature is too low, the solder may not melt completely, resulting in weak or incomplete joints. If the temperature is too high, the solder may become overly fluid, leading to excessive wetting or bridging.
Learn More
How many types of Solder Paste are there?
Solder paste can be broadly classified into three main groups, based on the flux particle size, based on the flux and according to the material alloy factor.
By Solder Paste Particle Size
Particle size is a critical factor in solder paste, affecting its printability, wetting characteristics, and overall soldering performance. Smaller particles can provide finer detail and better wetting, but they may also be more susceptible to oxidation. Larger particles, on the other hand, can be easier to handle but may not provide the same level of detail. Choosing the appropriate particle size for a specific application depends on factors such as:
Component size and pitch: Smaller components and finer pitches generally require finer-particle pastes. The type of solder paste you are using can influence stencil thickness. Fine-pitch solder pastes with smaller powder sizes may work well with thinner stencils, while coarser solder pastes may require thicker stencils to achieve proper paste release.
PCB design: Complex PCBs with intricate circuitry may benefit from finer-particle pastes. The PCB design, including pad sizes, spacing, and component orientation, can impact stencil thickness requirements. Ensure that the stencil thickness matches the PCB layout and pad designs.
Soldering process: The reflow profile and other soldering parameters can influence the choice of particle size. Thicker stencils may offer more forgiving printing processes by reducing the risk of bridging between fine-pitch components, while thinner stencils may require more precise setup and control.
Reliability requirements: Applications requiring high reliability may benefit from finer-particle pastes due to their improved wetting characteristics.
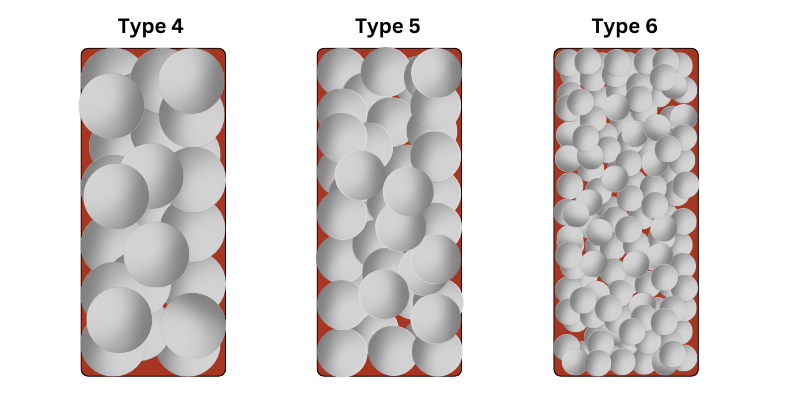
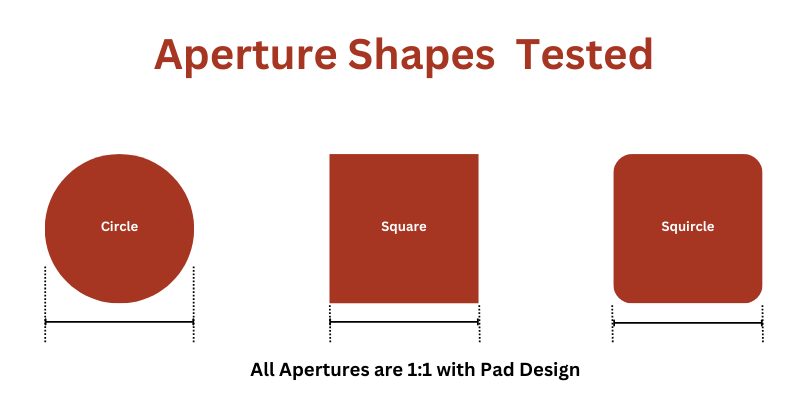
The image showcases three common aperture shapes used in stencil printing: Circle, Square, and Squircle. These apertures are openings in the stencil through which solder paste is dispensed onto the printed circuit board (PCB). Circle: A classic and widely used shape, offering a clean and symmetrical solder deposit. Square: Often used for larger components or when a more rectangular pad shape is required. Squircle: A hybrid shape between a circle and a square, balancing circular and square characteristics.
All apertures in this image are 1:1 with the pad design, meaning their dimensions match the corresponding pad on the PCB. This ensures optimal solder paste placement and reduces the risk of defects like bridging or voids.
The 5-ball rule is a simple guideline used in electronics manufacturing to estimate the optimal particle size of solder paste for a given stencil aperture. It states that the diameter of the solder paste particles should be approximately 5 times smaller than the smallest dimension of the stencil aperture. It will certainly help in preventing solder bridging, improve soldering print quality and enhance wetting.
The 5-ball rule is a valuable tool for manufacturers as it provides a quick and easy way to estimate the appropriate solder paste particle size for a given PCB design. However, it's important to note that this is a general guideline, and there may be exceptions depending on specific factors such as component density, stencil thickness, and soldering process. While the 5-ball rule is a useful starting point, manufacturers should also consider conducting experiments and testing different particle sizes to determine the best fit for their specific application.
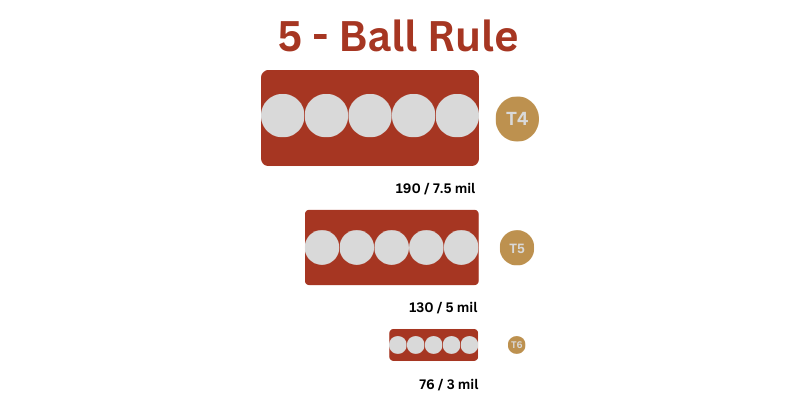
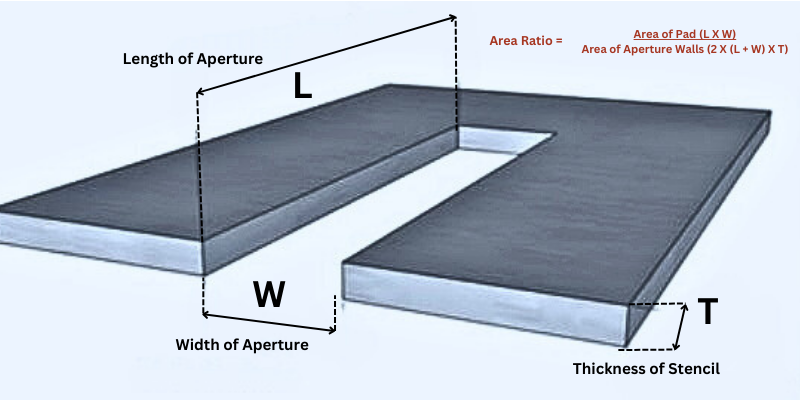
Area Ratio = Area of Pad (L x W) / Area of Aperture Walls (2 x (L + W) x T)
Where:
- L = Length of the aperture
- W = Width of the aperture
- T = Thickness of the stencil
A higher area ratio means a larger volume of solder paste will be deposited on the pad, which can be beneficial for larger components or thicker PCB layers. On the contrary, a higher area ratio can also increase the stress on the stencil, leading to faster wear and tear. A lower area ratio can result in a thinner layer of solder paste, which may be desirable for fine-pitch components or when reducing solder volume is important. The area ratio can influence the quality of the solder print, affecting factors like bridging, voids, and overall component placement accuracy.
Manufacturers use area ratio as a guideline to optimize stencil design for specific applications. By carefully considering the desired solder paste volume, print quality, and stencil wear, they can select or design apertures with appropriate area ratios.
By Solder Paste Flux
Flux is used to remove oxidizing metals, seal out air to prevent oxidization and enhance the wetting characteristics of the substrate to improve amalgamation. The IPC J-STD-004C classification system provides a standardized way to categorize solder paste fluxes based on their composition, activity, and halogen content. Fluxes are classified into three main types: rosin-based, resin-based, and organic-based. The activity level of a flux determines its cleaning and wetting properties, while the halogen content indicates whether it contains harmful substances. The complete designator for a flux combines these three elements to provide a unique identifier. By understanding this classification system, you can more easily select the appropriate solder paste flux for your specific application and ensure compliance with industry standards.
Soldering materials that contain flux are divided into Clean (often called Water Soluble) and No Clean materials. Flux can be corrosive so the Clean (meaning Clean it) category needs cleaning while the No Clean category suggests that it can be used without the extra cleaning step.For "No Clean" flux, this is indeed the case for most applications since they leave little to no residue that doesn't affect the circuits. There are some specific application environments though where even though the residue is minimal, it can potentially interfere with testing or other accompanying processes. So for high clock speed electronics, to improve the substrate adhesion of packages that will be underfilled and for cosmetic reasons, assemblers tend to go against the grain and clean the "no clean". Halide containing, "Clean" fluxes, while leaving more residues, are easier to clean within a short wash cycle. Ironically enough the halide-free "No clean" flux chemistry makes it harder to remove so a proper saponified solution must be used.
Flux Composition | Partial Designator | Flux Activity | Partial Designator | Complete Designator Containing Halides | Complete Designator No Halides |
---|---|---|---|---|---|
ROsin | RO | Low | ROL | ROL1 | ROL0 |
Moderate | ROM | ROM1 | ROM0 | ||
High | ROH | ROH1 | ROH0 | ||
REsin | RE | Low | REL | REL1 | REL0 |
Moderate | REM | REM1 | REM0 | ||
High | REH | REH1 | REH0 | ||
Organic | OR | Low | ORL | ORL1 | ORL0 |
Moderate | ORM | ORM1 | ORM0 | ||
High | ORH | ORH1 | ORH0 | ||
In-Organic | IN | Low | INL | INL1 | INL0 |
Moderate | INM | INM1 | INM0 | ||
High | INH | INH1 | INH0 |
General Understanding on Fluxes
By Solder Paste Material
Solder paste can be classified based on its material composition, primarily into lead-containing and lead-free types.
What is a Lead Solder?
Lead solder is a metallic alloy primarily composed of lead (Pb) and tin (Sn), often with small amounts of other elements like antimony (Sb) or copper (Cu). Historically, solder has been melted and solidified between the joined pieces using these alloys to unite metals. Compared to other metal alternatives, lead solder cools more slowly. This lessens the chance of the joint breaking and is effective in wetting joints. Lead solder has a lower and precise melting point, unlike many other metals. This makes it easier to control in the automated PCB assembly and less likely to damage electronic components during the soldering process.
What is a Lead-Free Solder?
Lead-free solder is a metallic alloy used for joining metals that do not contain lead (Pb). It's made without harmful lead and uses metals like tin, copper, silver, bismuth, or antimony. These alloys are designed to replace traditional lead-based solders due to the environmental and health concerns associated with lead.
Compared to lead-based solders, lead-free solders typically have higher melting temperatures, requiring adjustments in soldering processes. Lead-free solders often exhibit different mechanical properties, such as higher strength and hardness, compared to lead-based solders.
Some common lead-free combination includes Tin-Silver-Copper [SnAgCu] alloy, Tin-Copper [SnCu] alloy and Tin-Bismuth [SnBi] alloy. Choosing the right lead-free solder depends on the specific needs of the electronic product. Factors like component compatibility, thermal cycling requirements, and joint reliability need to be carefully considered when selecting a lead-free solder.
What is the Reflow Profile of a Solder?
A reflow profile is a specific temperature sequence that a PCB with applied solder paste is subjected to in order to melt the solder and create electrical connections between components and the PCB. The standard reflow profile has four zones: preheat, soak, reflow and cooling. The profile in the picture above will serve as a typical reference [benchmarking SAC305 solder paste reflow profile] and describe the ideal temperature curve of the top layer of the PCB.
Preheat Stage
The PCB is initially at the room temperature. It cannot be exposed to high heat abruptly because of the possibility of thermal shock, which can result in flaws including component cracking and solder paste spattering, leading to solder balls during reflow. The PCB is preheated to lessen the thermal shock and eliminate any trapped moisture by gradually heating it to a warming-up temperature, which is usually between 150 and 180°C at a maximum rate of 3 °C/s. In addition, preheating enables the flux to be activated, which improves its ability to clean the surfaces that need to be soldered and encourages excellent wetting between the solder and the components.
Soak Stage
Before moving on to the reflow stage, this phase's goal is to make sure every component is at the proper temperature. The average soak time is 60 to 120 seconds, depending on the assembly's "mass differential" and the kinds of components used. The more efficient the heat transfer during the soak phase the less time is needed. Shorter soak times are associated with higher heat transfer efficiency.
The soak zone brings the temperature of all components and board areas to an equal level before the rapid temperature increase begins. This prevents thermal shock and reduces the risk of component damage. Components do not heat up at the same rate due to variations in thermal inertia; this is particularly true when it comes to infrared heating, as components absorb infrared radiation at different rates.
Reflow Stage
Temperature increases in the reflow zone reach a temperature above the melting point (the temperature above liquidus, or TAL) at a rate of about 2 °C. The peak temperature for the reflow zone is at least 25 °C above TAL, to ensure proper wetting and component contact, thereby creating better joints. This is important for lead-free solders (such as SAC305), because this solder is less effective at wetting than leaded solders.
The solder paste is now melting and forming a liquid due to the temperature inside the reflow oven being raised over its melting point. To provide proper "wetting" between components and PCB, solder must be kept above its melting point (time above liquidus). The TAL (temperature above liquidus) should be held for 30 to 40 seconds (varies depending on alloy composition), so that an intermetallic compound (IMC) is able to form. Controlling the peak temperature during the reflow phase is crucial because too much heat can cause some components to fail.
Cooling Stage
This is merely the phase in which the assembly is cooled; nevertheless, it is crucial to avoid cooling the assembly too quickly; typically, a rate of cooling no more than 4 ºC/second is advised. As the PCB cools down, the molten solder solidifies, forming strong and reliable electrical connections between the components and the PCB.
One important element that is vital to the soldering process is the cooling zone in a reflow oven. The printed circuit board (PCB) is intended to be progressively cooled down once the solder has melted and poured into the joints. Rapid cooling can induce thermal stress on the components and the PCB, potentially leading to cracks or delamination. The cooling zone helps to reduce thermal stress by gradually lowering the temperature, allowing the materials to cool down evenly.
Solder Alloys Properties
There are multiple types of Alloys that can be used for a wide variety of applications. Different companies tend to use different codes and abbreviations for the same alloy but at the end of the day it all comes down to the alloy composition. So don\'t get confused by the branding and tradenames and just focus on the metal content and the end properties. In the following table you can see the codes Henkel is using for some popular alloys.
Code | Alloy | Melting point (°C) | Density point (g/cm3) | Electrical resistivity | Thermal conductivity (W/m-K) |
---|---|---|---|---|---|
2.5S | Pb92.5/Sn05/Ag2.5 | 287-296 | 11.02 | 0.2 | 44 |
90iSC (High-Reliability) | SAC387/Bi3/Sb1.5/Ni0.02 | 209-217 | 7.38 | 0.132 | 58 |
92A | Sn91.5/Sb8.5 | 235-243 | 7.25 | 0.145 | 28 |
95A | Sn95/Sb5 | 236-240 | 7.25 | 0.145 | 28 |
96S | Sn96.5/Ag3.5 | 221 | 7.37 | 0.123 | 55 |
SAC0307 | Sn99/0.7Cu/0.3Ag | 217-228 | 7.33 | 0.15 | 64 |
SAC305* | SAC305 or Sn96.5/Ag3.0/Cu0.5 | 217 | 7.338 | 0.132 | 58 |
SAC387** | SAC387 or Sn95.5/Ag3.8/Cu0.7 | 217 | 7.44 | 0.132 | 60 |