Slot insulation
Motors In Cars
Industrial motors include power tools, home appliances and industrial motors. In automotive, motors are used for enclosures, windshield wipers, seat adjusters, window lifts and fuel pumps, quality cars can have up to 130 motors. See the figure below.
Motor Armature Insulation Classes
The motor’s insulation class is the maximum (hot spot) temperature at which the insulation can be operated and still have an average life of 20,000 hours. The Rule of Thumb is that a 10°C rise cuts the insulation's useful life in half and a 10°C decrease doubles the insulation's life. Depending on where the motor is going to be used, Class B should be sufficient for 95% of the applications. There are some applications such as ABS motors or Power closure motors that require Class H insulation but these are the exception to the rule.
Insulation System Class | Maximum Hot Spot Temperature |
A | 105 °C |
B | 130 °C |
C | 155 °C |
D | 180 °C |
Epoxy Coating Powders for Slot Insulation of Motor Armatures
An electric motor is made by wrapping an electric current around a magnetic core, and these two must be insulated from each other. This can be done in two ways: (1) Using slot liners and plastic casting; (2) Using insulating epoxy coating powder. Compared with slot liners and plastic casting method, epoxy coating powders owns the advantages of efficiency and reliability as:
- Allows to use up to 25% more copper wire, making the motors 15%~20% more efficient.
- Provides a more even consistent distribution, which improves the balancing, efficiency and life time of the motors. It also makes it much quieter.
- Epoxy powders is 10 times more conductive than air, which dissipates more heat from the motor, increasing operating lifetime.
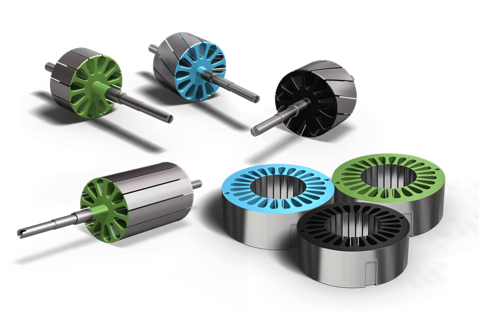
Great Performance
- Excellent edge coverage
- High cut through resistance temperature (minimum 300°C)
- High service temperatures and insulation class
- Capability to provide a range of thermal conductivities
Great Manufacturing Productivity
- High build rate enables faster coating line speed
- Outstanding adhesion to metal and plastics
- Low thickness required to achieve max performance
- Both induction and oven cure chemistries
Properties Matrix Of Epoxy Coating Powders
While selecting epoxy coating powder solutions for your motor application, there are many properties we may take into considerations. The following matrix shows how epoxy coating powder properties would effect your application performance. Contact us with your application needs for the optimal solutions!
Product Recommendation
Product | Insulation Class | Color | Breakdown Voltage | Impact Strength | Edge Coverage | Shear Adhesion Strength |
MCP-5000 | Class B (130°C) | Green | 25 kV/mm | > 500mm, 500g*1/16 inch | >55% | Fe-Fe, >30 Mpa (JIS K6850 Method) |
MCP-5260 | Class F (155°C) | Green | 30 kV/mm | ?450 kg/mm | 45% |