MCP-5260 | Motor Coating Powder
- Light Green Color
- Good Edge Coverage
- Insulation Class F
Product Description
LINQSOL MCP-5260 is a Class F (155°C) coating powder suitable for motor and rotor coating. It is ideal for improving the efficiency and productivity of small, lightweight parts.
LINQSOL MCP-5260 has high hardness, good edge coverage (45%), excellent thermal conductivity, and is able to increase the product's reliability by keeping the temperature low while the part rotates. It can be applied through an electrostatic fluidized bed, hotbed dipping, and thermal spraying.
Key Features:
- Insulation Class F (155°C)
- Excellent Thermal Conductivity
- No cracking from 180 °C to room temperature
- Application methods include: electrostatic fluidized bed, hotbed dipping, and thermal spraying
- Energy Efficient
Recommended coating Temperature:
- 180-200 °C x 30-60 min
Technical Specifications
General Properties | |||||
Color Color The color | Light Green | ||||
| |||||
Electrical Properties | |||||
Breakdown Voltage Breakdown Voltage Breakdown voltage is the minimum voltage necessary to force an insulator to conduct some amount of electricity. It is the point at which a material ceases to be an insulator and becomes a resistor that conducts electricity at some proportion of the total current. After dielectric breakdown, the material may or may not behave as an insulator any more because of the molecular structure alteration. The current flow tend to create a localised puncture that totally alters the dielectric properties of the material. This electrical property is thickness dependent and is the maximum amount of voltage that a dielectric material can withstand before breaking down. The breakdown voltage is calculated by multiplying the dielectric strength of the material times the thickness of the film. | 30,000 V | ||||
Volume Resistivity Volume Resistivity Volume resistivity, also called volume resistance, bulk resistance or bulk resistivity is a thickness dependent measurement of the resistivity of a material perpendicular to the plane of the surface. | 1.0x1013 Ohms⋅cm | ||||
Mechanical Properties | |||||
Edge Coverage | 45 % | ||||
Impact Strength | 450 kg mm | ||||
Thermal Properties | |||||
| |||||
| |||||
Specific Heat Capacity Specific Heat Capacity Specific heat capacity is the amount of heat energy required to raise the temperature of a substance per unit of mass. The specific heat capacity of a material is a physical property. It is also an example of an extensive property since its value is proportional to the size of the system being examined. | 1.1 - 1.4 J/(g⋅°C) | ||||
Thermal Conductivity Thermal Conductivity Thermal conductivity describes the ability of a material to conduct heat. It is required by power packages in order to dissipate heat and maintain stable electrical performance. Thermal conductivity units are [W/(m K)] in the SI system and [Btu/(hr ft °F)] in the Imperial system. | 0.3 - 0.4 W/m.K |
Additional Information
Technical Specifications | MCP-5000 | MCP-5260 |
Insulation Class | B (130°C) | F (155°C) |
Coating Temperature | 200 °C x 15 min | 180-200 °C x 30-60 min |
Breakdown Voltage (V) | 25,000 | 30,000 |
Volume Resistivity (Ohms⋅cm) | 1.0 x 1016 | 1.0x1013 |
Edge Coverage (%) | 55 | 45 |
Gel Time (sec) | 120 @ 160°C | 20-60 @ 180°C |
Melting Temperature (°C) | 58-65 | 98-110 |
Application Methods | Electrostatic Fluidized Bed | Electrostatic Fluidized Bed, Hotbed Dipping, Thermal Spraying |
How to use MCP-5260:
To begin, the surface of the substrate should always be clean, dry, and contaminant free. If the substrate is not prepared correctly, failure can occur. For the electrostatic fluidized bed application, the air pressure is adjusted to fluidize the powder in the tank. Then the powder is charged, and the part is rotated on a screw conveyance belt until it reaches the required coating thickness. Any undesired powder can be brushed off, then the part moves to the oven for curing. For the hotbed coating/thermal spraying application, the part is preheated to 180-200 °C, then submerged into the powder bed. After 3-5 seconds it is removed, excess powder shaked off, and redipped. This process is repeated until desired coating thickness is achieved. Finally, the part is cured in an oven.
Industrial motors include power tools, home appliances and industrial motors. In automotive, motors are used for enclosures, windshield wipers, seat adjusters, window lifts, and fuel pumps, quality cars can have up to 130 motors. An electric motor is made by wrapping an electric current around a magnetic core, and these two must be insulated from each other. This can be done by using insulating epoxy coating powder. Epoxy coating powders are widely used due to the advantages of efficiency and reliability. Check our Application Page Slot Insulation for more details.
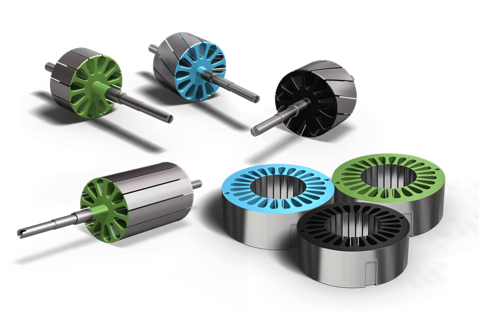
Insulation Epoxy Coating Powder Requirements
Great Performance
- Excellent edge coverage
- High cut-through resistance temperature (minimum 300°C)
- High service temperatures and insulation class
- Capability to provide a range of thermal conductivities
Great Manufacturing Productivity
- High build rate enables faster coating line speed
- Outstanding adhesion to metal and plastics
- Low thickness required to achieve max performance
- Both induction and oven cure chemistries
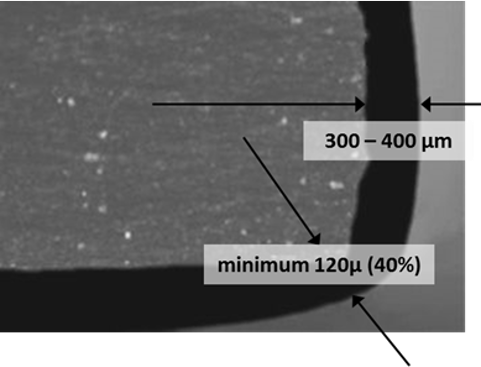
Epoxy coating powders are likely to be cut by copper wire at the edges. Minimum 300-400um coating thickness and 40% edge coverage ratio are required. MCP-5260 has an edge coverage of 45%.
MCP-5260 provides an even, consistent distribution of coating. This improves the motor balance, which in turn increases efficiency and decreases vibration and noise.
Lower temperature and faster cure plus great electrostatic pickup increase productivity and save money, MCP-5260 has a melting temperature of 98-110°C, which allows quick pick up.
Storage
Store in a ventilated, dry, and clean environment below 25°C. Keep away from fire and heat sources. It is strictly forbidden to store in outdoor environments. The product has a shelf life of 6 months under proper storage conditions.
Precautions
- Avoid long-term skin contact. Powder that touched the skin should be rinsed off quickly.
- During operation, dust-proof masks should be used to avoid inhalation.
- Keep the oven temperature stable, so as not to affect the color and quality of the coating due to excessive temperature deviation.
- The concentration of dust should be controlled within a safe range to avoid malfunctioning the coating equipment.