Ion Exchange Membranes & Polymers
Porous composite separators are traditional materials commonly used in mature electrochemical technologies such as alkaline water electrolyzers and fuel cells. These separators play a crucial role in maintaining the physical separation between electrodes while enabling efficient ion transport through their porous structure. Made from a combination of polymers and inorganic materials, porous composite separators offer a balance of mechanical strength, ion conductivity, and thermal stability.
Ion exchange membranes and polymers enable the development of next-generation environmental technologies. These materials have a hydrocarbon backbone, which enables performance and life cycle improvements across the industry in fuel cells and hydrogen electrolysis, while making them far less impactful on the environment than common fluorinated materials. By using advanced stabilization techniques, they are able to compete with the most robust of alternatives.
Hydrocarbon membranes are significantly tougher than competitive products leading to a longer service life and reduced lifetime cost. Unlike their proton exchange counterparts, alkaline based anion exchange membrane systems can operate without the use of precious metals such as platinum and iridium, making them way more cost effective and environmentally friendly. Caplinq is proud to present the ONLY High performance non-fluorinated material in the market.
PEMION - PF1-HLF8-15
- PFAS-free Proton Exchange Membrane with Hydrocarbon reinforcement
- 15 µm thickness
- Optimized for heavy duty fuel cell applications
- 4 - 6 weeks
AEMION+™-AF3-HWC9-70
- Water Electrolysis
- Acid Recovery and Salt Splitting
- 70 micron thick membrane with woven PEEK reinforcement
- 4 - 6 weeks
VRB-MEM50 | 50μm VRB membrane
- Designed as cation (proton) exchange membranes for redox flow batteries
- High acid capacity and conductivity for improved performance
- Extended service life
- 6 - 8 weeks
VRB-MEM75 | 75μm VRB membrane
- Designed as cation (proton) exchange membranes for redox flow batteries
- High acid capacity and conductivity for improved performance
- Extended service life
- 6 - 8 weeks
LINQCELL ALK-PCS500
- Low internal resistance
- High gas barrier properties
- Optimized separator for large-scale and high-pressure alkaline water electrolyzers
- 8 - 12 weeks
LINQCELL VRB-AEM50
- 50um - Low ohmic resistance
- Excellent oxidative stability and chlorine resistance
- Designed as ion exchange membranes for redox flow batteries
- 8 - 12 weeks
LINQCELL VRB-AEM30
- 30um - Ultra low ohmic resistance
- Excellent oxidative stability and chlorine resistance
- Designed as ion exchange membranes for redox flow batteries
- 8 - 12 weeks
AEMION+™ - AF3-HWK9-75
- Water Electrolysis
- Acid Recovery and Salt Splitting
- 75 micron thick membrane with woven PEEK reinforcement
- 4 - 6 weeks
PEMION+™ - PP1-HNN8-00
- High conductivity binder and coating material
- High concentration of functional groups
- Chemical and oxidative stability
- 4 - 6 weeks
AEMION+™ - AP3-HNN9-00
- Enabling precious metal free systems
- High conductivity
- Catalyst layer ionomer
- 4 - 6 weeks
Product Selector Guide
Product | Type | Thickness (um) | Tensile strength (MPa) | Young's Modulus (MPa) | Elongation (%) | Water uptake (%) | Max. Recommended Operating Conditions | Reinforcement | Application |
---|---|---|---|---|---|---|---|---|---|
AF3- CLF9-25 | Anion | 25 | > 85 | > 480 | > 80 | <15 | 0.1–2 M KOH ≤ 90 °C | NW PTFE | Carbon dioxide electrolyzers |
AF3- CLF9-50 | Anion | 50 | > 80 | > 450 | 80 - 120 | <15 | 5 M KOH, 95 °C | NW PTFE | Carbon dioxide electrolyzers |
AF3-HWK9-75 | Anion | 75 | > 57 | > 630 | 27 | <15 | 0.1–2 M KOH ≤ 90 °C | Woven PEEK | AEM water electrolyzers, Acid recovery, Salt splitting |
PF1- HLF8-15 | Proton | 15 | > 50 | > 600 | > 50 | 150 - 190 | 110 °C | Hydrocarbon | PEM fuel cells |
VRB-MEM50 | Proton | 50 | 38 | 600 | > 160 | 49 | - | - | Redox flow batteries |
VRB-MEM75 | Proton | 75 | 38 | 600 | > 160 | 49 | - | - | Redox flow batteries |
VRB-AEM30 | Anion | 30 | >35 | >800 | >200 | - | Acidic to neutral environment, 40 °C | - | Redox flow batteries |
VRB-AEM50 | Anion | 50 | >30 | >750 | - | - | Acidic to neutral environment, 40 °C | - | Redox flow batteries |
Product | Material | Thickness (µm) | Porosity (%) | Average Pore Diameter (nm) | Bubble Point (bar) | Operating Temperature (℃) |
---|---|---|---|---|---|---|
ALK-PCS500 | PPS Composite | 500 | 55 | <150 | 3-5 | 110 |
Product | Type | IEC (meq/g) | Conductivity (mS/cm) | Water uptake OH- % | Density (g/cm3) | Solubility |
---|---|---|---|---|---|---|
AP3-HNN9-00 | Anion | 1.9 - 2.7 | 4 - 9 | 20 - 50 | - | - |
PP1-HNN8-00 | Proton | 2.8 - 3.1 | - | - | 1.2 | Alcohols/Water |
- IEC in the hydroxide (OH-) counter-ion form.
- Approximate swelling properties when cast into membrane form at 25 - 50 μm
These are prototype materials only intended to be used for early development activities and not intended for production items. Product information is to be used as a guide only, subject to change at any time.
Frequently Asked Questions
Separators and Ion Exchange Membranes and Polymers
How do ion exchange membranes differ from traditional separators?
Ion exchange membranes are polymer materials specifically designed to allow the selective transport of certain ions (e.g., protons or hydroxide ions), whereas traditional separators primarily prevent physical contact between electrodes and may not have the same level of ionic selectivity. Ion exchange membranes are typically thinner. In contrast, separators are often composite materials and are thicker, focusing on mechanical strength and preventing short circuits without necessarily providing selective ionic conduction.
What are ion exchange polymers?
Ion exchange polymers are materials with functional groups that facilitate ion exchange with surrounding solutions. In catalyst ink formulations, they improve ion conduction within the catalyst layer. These polymers are typically the same material as ion exchange membranes but are in powder form, which is dispersed in a solvent for easy integration into catalyst layers of electrochemical devices like fuel cells and electrolyzers.
Are there any environmental concerns with using ion exchange membranes?
Yes, certain ion exchange membranes, such as those based on perfluorosulfonic acids, have raised environmental concerns due to their persistence in the environment and potential toxicity. Research is ongoing to develop more sustainable and eco-friendly ion exchange polymers to mitigate these issues while maintaining performance in electrochemical applications.
What are the key properties to consider when selecting ion exchange membranes for electrochemical applications?
When selecting ion exchange polymers for electrochemical applications, key properties to consider include ionic conductivity, chemical stability, mechanical strength, thermal stability, and resistance to degradation. These properties ensure that the polymer will perform efficiently and last under the demanding conditions typical of fuel cells, electrolyzers, and batteries.
Learn More
Porous Composite Separators
Porous separators are composite membranes made of inorganic (ceramic) nanoparticles dispersed in a polymer. The polymer binder creates a highly interconnected inorganic–organic porous structure, while the ceramic nanoparticles provide hydrophilicity, improving ion conduction within the separator.
In addition to these main components, polymer mesh reinforcements are incorporated into the porous composite separator to increase mechanical strength and improve processability for mass production.
Porous Separators in Alkaline Water Electrolyzers
Porous separators are widely used in commercial alkaline water electrolyzers to physically separate the anode and cathode, preventing the crossover and mixing of the product gases, H₂ and O₂, while still allowing ionic contact between the electrodes.
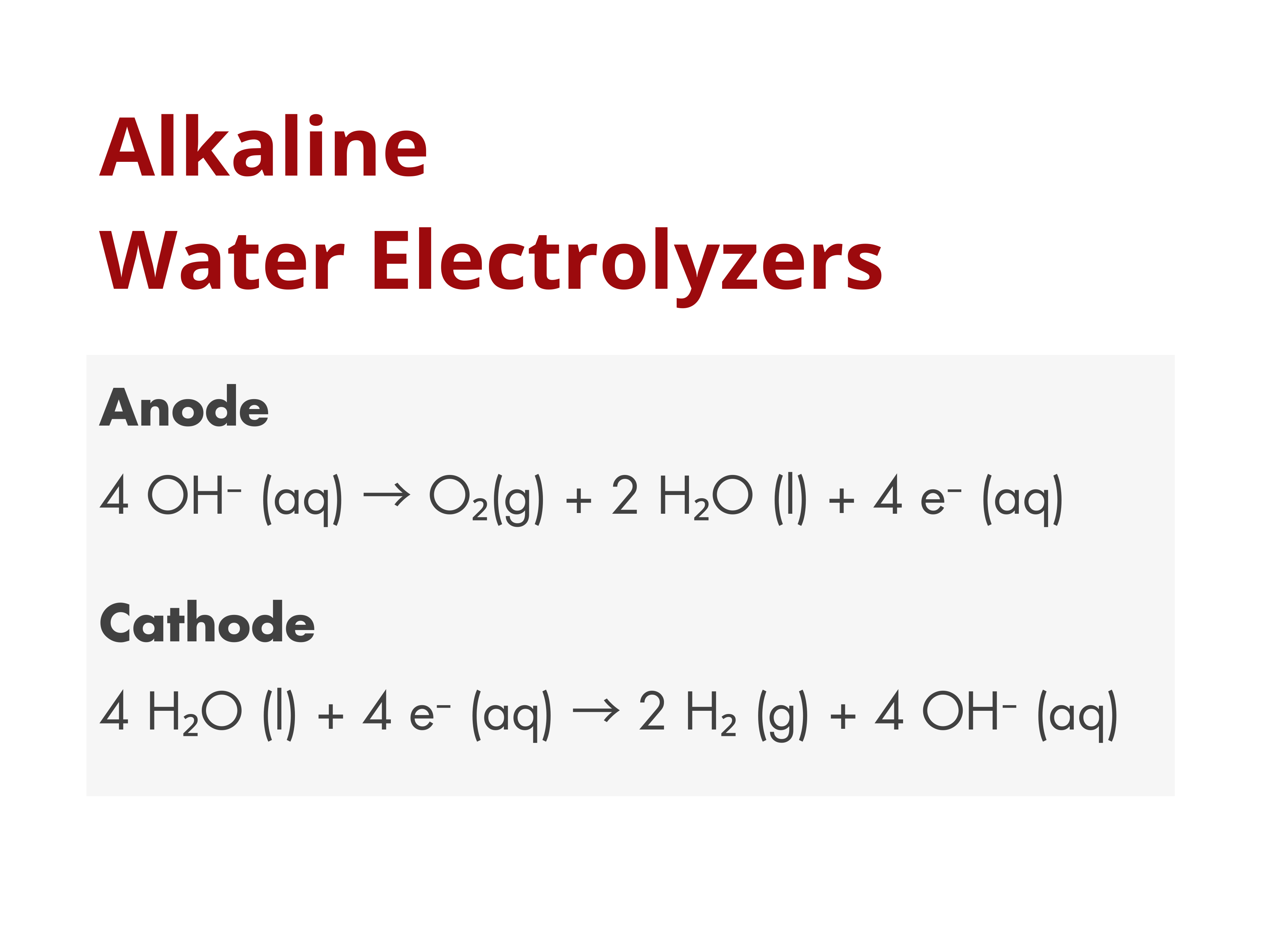
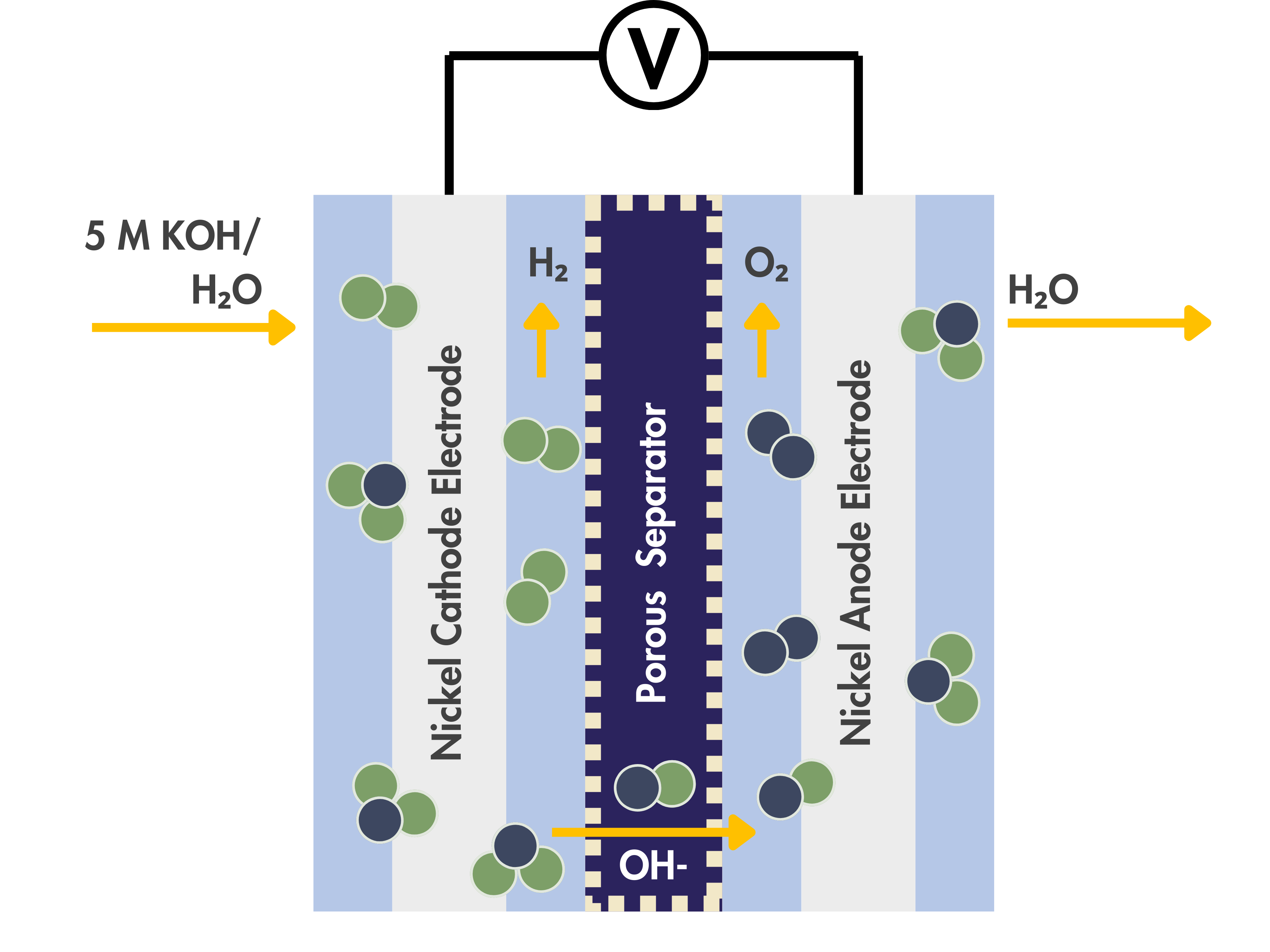
Property Requirements for Porous Separators in Alkaline Water Electrolyzers
When used for electrolysis, porous separators need to meet these two performance requirements:
LOW OHMIC RESISTANCE
They must have low ohmic resistance to facilitate ion transport across the electrodes and maintain electroneutrality between the cathode and anode.
HIGH BUBBLE POINT PRESSURE
They must have high bubble point pressure or the minimum pressure of gas to penetrate the separator to avoid the crossing over and mixing of product gases.
Of course, these two requirements only touch the surface. In reality, a lot of property interplays are at work. For example, the wettability of the separator is also important because it affects not only the gas permeability of the separator but also its ionic conductivity.
When the membrane is highly wettable by polar liquids, the electrolyte can effectively fill the pores of the separator, giving it hydration for ionic conduction. On the other hand, a lack of wettability leads to several issues. First, gas bubbles can stick to the surface of a dry separator easily, filling the voids with gas rather than the electrolyte. This disrupts electrolyte flow and increases ohmic resistance. Then, the accumulation of gas bubbles within the pore structure of the separator can lead to increased gas diffusion, resulting in the mixing of hydrogen and oxygen, which reduces efficiency in electrochemical processes and raises safety concerns.
The stability of the separator is another important consideration. In alkaline water electrolyzers, the feed is a very concentrated KOH solution (>20 wt% KOH or 5 to 7 M KOH). Such high concentrations of alkaline solution can degrade the separator. Over time, this can lead to the breakdown of the separator’s structure, which compromises both its mechanical integrity and its ability to facilitate ion transport effectively.
Questions to ask when Choosing Separators for Alkaline Water Electrolyzers
✅ What is the ion conductivity of the separator?
✅What is the separator's bubble point pressure?
✅Is the separator chemically stable in concentrated KOH solutions?
✅How does the separator perform at temperatures around 80 °C?
✅What is the separator’s pore size distribution?
✅Is the separator hydrophilic enough?
✅Is the separator mechanically strong enough to withstand operating pressures?
✅How long is the expected lifespan of the separator under typical operating conditions?
Ion Exchange Membranes
An ion exchange membrane (IEM) is a thin barrier that allows the selective passage of specific ions from one compartment to another of devices. Depending on the membrane's electric charge, they allow certain ions to pass through while blocking others.
Types of Ion Exchange Membranes according to Ion-exchange Functionality
Ion exchange membranes (IEMs) can be classified into different categories based on various criteria, such as ion-exchange functionality, chemical composition, and intended applications.
In terms of ion-exchange functionality, IEMs can be broadly categorized as:
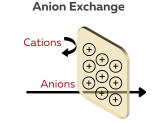
Anion Exchange Membranes (AEMs)
AEMs selectively allow the passage of negatively charged ions (anions) while blocking positively charged ions (cations). They are made of a polymer material that contains functional groups with a negative charge, such as sulfonic acid or carboxylic acid. These functional groups are capable of exchanging anions in electrochemical processes. The structure of the membrane and the type of functional group can affect the properties and characteristics of the AEM, including its ion exchange capacity, selectivity, and stability.
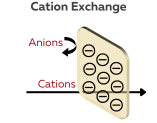
Cation Exchange Membranes (CEMs)
CEMs are polymeric materials that can exchange cations (positively charged ions) with the surrounding solution. These membranes are designed to selectively allow the passage of cations while blocking anions (negatively charged ions). The selective ion transport is achieved through the presence of negatively charged functional groups, such as sulfonic acid (–SO₃H) and carboxyl (–COOH) groups.
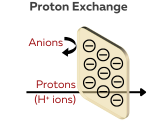
Proton Exchange Membranes (PEMs)
PEMs are specifically designed to selectively allow protons (H⁺) to pass through while blocking other ions such as anions and other cations, such as K⁺, Na⁺, and Li⁺. This makes them highly suitable for applications that require proton conduction, such as fuel cells and electrolysis.
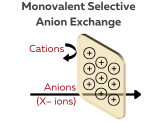
Monovalent Selective Anion Exchange Membrane
A monovalent selective anion exchange membrane is specifically designed to allow the selective transport of monovalent anions such as Cl⁻, Br⁻, OH⁻, F⁻, and I⁻, across the membrane, while blocking the passage of divalent anions (e.g., SO₄²⁻, CO₃²⁻) and cations (e.g., Na⁺, K⁺).
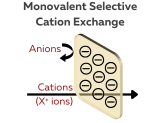
Monovalent Selective Cation Exchange Membrane
A monovalent selective cation exchange membrane (CEM) is designed to selectively allow the passage of monovalent cations (such as Na⁺, Li⁺, K⁺, Ag⁺) while preventing the passage of other ions, particularly divalent cations (such as Ca²⁺, Mg²⁺) and anions (e.g., Cl⁻, SO₄²⁻).
Key Properties of Ion Exchange Membranes
Generally, the properties of IEMs are determined by the properties of the polymer backbone and fixed charges that make up their structures. Particularly, the density, wettability (hydrophobicity or hydrophilicity), and morphology of the polymer matrix, as well as the type and concentration of the charged functional groups, affect the resulting properties of the IEMs. The mechanical, chemical, and thermal properties of IEMs are primarily influenced by the polymer backbone, whereas the electrochemical properties, conductivity, and permselectivity are determined by the concentration of the fixed charges.
Ion Exchange Capacity. IEC is the concentration of the fixed charged species measured as milliequivalent per gram (meq (fixed charge)/g (dry IEM)). The IEC of most commercially available IEMs varies from 1–3 meq/g. IEC is an important material property because it affects other IEM properties, such as ionic conductivity, swelling ratio, water uptake, and fluid permeability.
Ionic conductivity. Ionic conductivity is a quantitative measure of the electric-field induced transport of ions across the IEM. It is the inverse of the membrane specific resistivity, which is an intrinsic IEM property that can be used for the comparison of the inherent efficiency of different IEMs. To put it simply, ionic conductivity tells how well the membrane can facilitate the transport of the counter-ions across. It is related to the IEC of the membrane. Higher IEC means that there are more functional groups in the polymer backbone that can participate in the ion transport, which potentially increases the ionic conductivity of the IEM. In turn, this higher ionic conductivity reduces the overpotentials and improves the performance and efficiency of the water electrolysis and fuel cells. While it is affected by the IEC, ionic conductivity is also influenced by other factors, such as membrane morphology, water content, and membrane thickness.
Permselectivity. Permselectivity is one of the most important properties of IEMs. It refers to the ability of the membrane to selectively allow the transport of the counter-ions while blocking the passage of the co-ions. Permselectivity values range from 0 to 1. For example, a perfectly selective PEM (with a permselectivity of 1) will only allow the diffusion of protons (H+ ions) across the membrane, completely disabling the transport of negatively charged species. On the other hand, permselectivity <1 implies that the IEM allows the passage of some co-ions. Highly permselective IEMs ensures that (1) the required ions for the electrochemical reactions are transported with greater efficiency, (2) the crossing over of species at the anode and cathode is minimized. The crossing over of reactants and products between the electrodes decreases the overall efficiency of the electrochemical device as less reactant is supplied at the site at which it is needed. Another thing, the crossover of ions can yield chemical reactions that cause corrosion or degradation of the IEM and other components. Highly permselective membranes are desired to achieve high performance, maintain product purity, ensure operational safety, and extend the longevity of the electrochemical device.
Dimensional stability (Membrane swelling and water uptake). IEMs are used to transport counter-ions while disabling the diffusion of co-ions and other redox-active species in electrochemical energy storage technologies. At the same time, IEMs must regulate the water (or other solvent) transport, keeping in mind that IEMs need to be hydrated to function properly. Dehydration can lead to the loss of ion conductivity, membrane shrinkage, and a decrease in overall performance. Proper hydration helps prevent these issues and ensures the long-term stability of the membrane. But, a striking balance between membrane hydration and water removal must be achieved. Too much water uptake (or water content) in the IEM might lead to membrane swelling, which affects the dimensional stability of the IEM. Flooding can ensue in which the excess water can block the transport pathways.
Membrane swelling measures the degree at which the membrane expands or its volume increases as the IEM absorbs water. Water uptake, on the other hand, measures the amount of water that an IEM can absorb under specific conditions. Optimal levels of membrane swelling and water uptake is required for effective water management in the device.
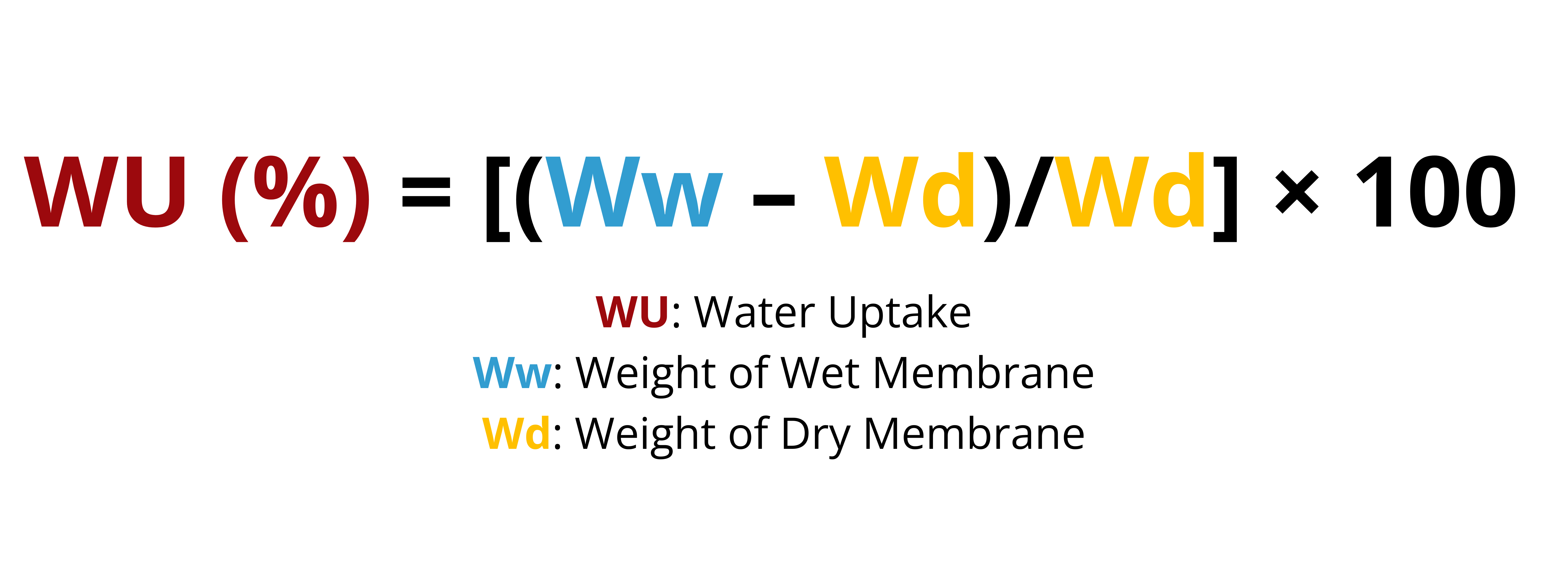
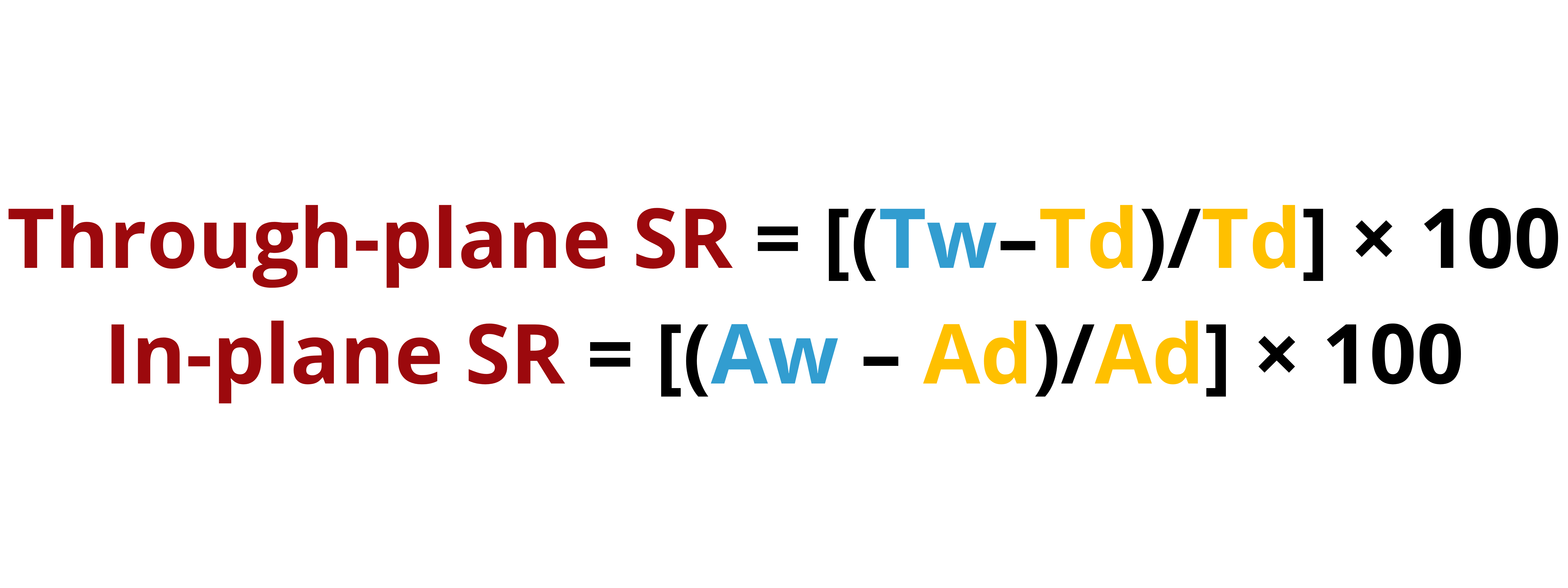
Chemical, mechanical, and thermal stability. Aside from performance-related properties, the chemical, mechanical, and thermal stability of IEMs are equally important to ensure the durability and long-term performance of fuel cells and water electrolyzers. Chemical stability is important to prevent membrane degradation as they are subjected to very aggressive conditions during operation. Mechanical stability ensures that the membrane will not fail in response to the compressive force applied to produce the stack. Lastly, thermal stability ensures that the IEM can continue to perform and not fail due to temperature effects.
Applications of Ion Exchange Membranes
Ion exchange membranes play a key role in electrochemical devices, like water electrolyzers, fuel cells, carbon dioxide electrolyzers, and redox flow batteries:
Hydrogen Generation through Water Electrolysis
Water electrolysis is the process of splitting water into hydrogen and oxygen gases using electricity. An electrolyzer is used to carry out this reaction. Electrolyzers come in a wide range of sizes, from compact, appliance-sized equipment ideal for small-scale distributed hydrogen production to large-scale, central production facilities that can be seamlessly integrated with renewable or other environmentally-friendly power generation sources.
Ion exchange membranes are used in both anion exchange membrane (AEM) water electrolyzers and proton exchange membrane (PEM) water electrolyzers, but their ion transport mechanisms differ:
- In AEM water electrolysis, the membrane selectively transports OH⁻ ions from the cathode, where they are produced alongside H₂ during the hydrogen evolution reaction, to the anode, where they participate in the oxygen evolution reaction.
- In PEM water electrolysis, the membrane facilitates the selective transport of protons (H⁺ ions) from the anode, where oxygen is evolved, to the cathode, where they combine with electrons to form hydrogen gas.
This difference in ion transport impacts the choice of materials, operating conditions, and overall system efficiency for each type of water electrolyzer.
Power Generation using Fuel Cells
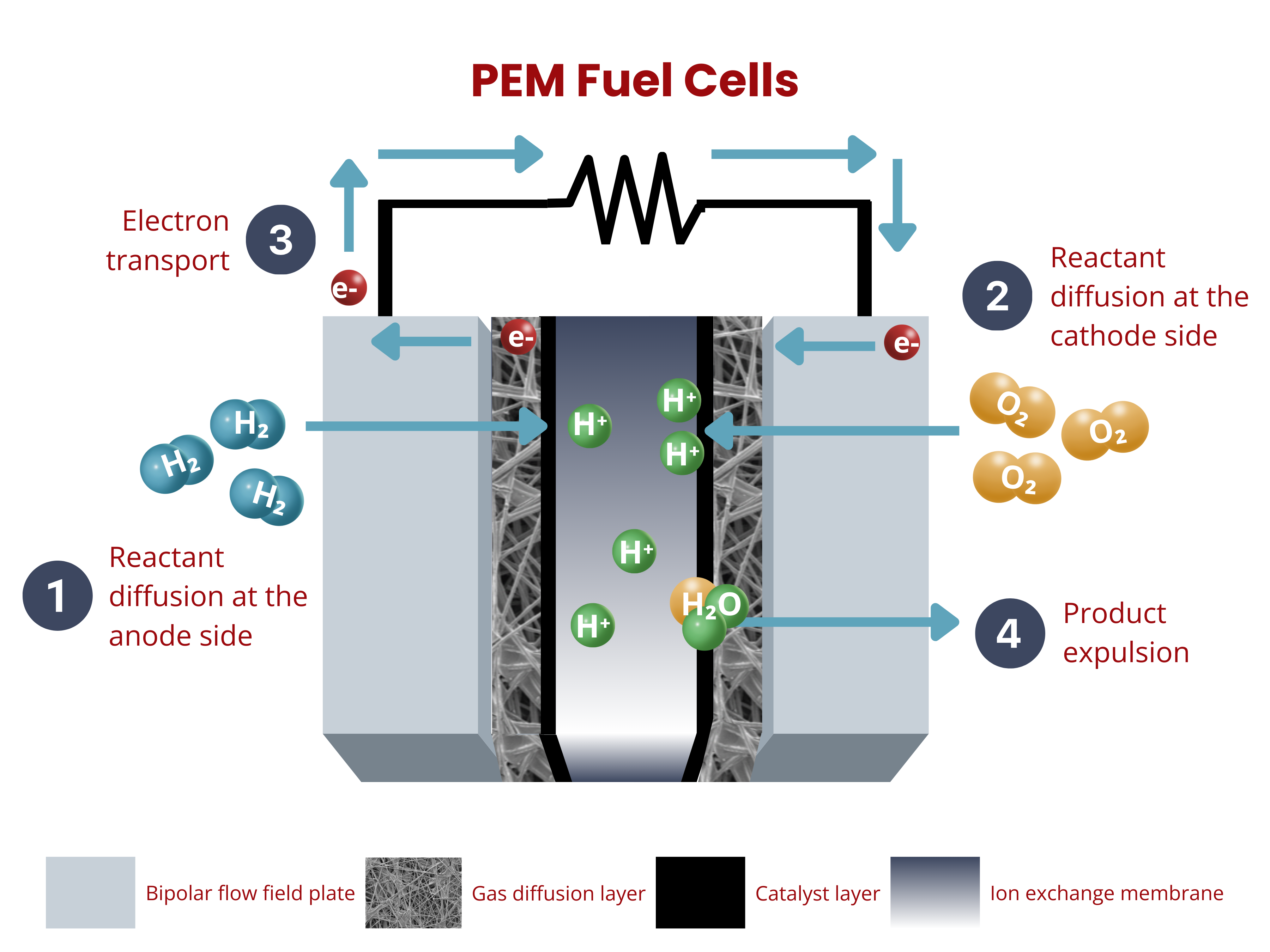
Fuel cells are electrochemical devices that convert chemical energy from a fuel, typically hydrogen, into electricity. They operate by combining hydrogen and oxygen in a controlled reaction to produce electricity, water, and heat as byproducts.
In simple terms, fuel cells are the reverse of water electrolyzers:
Water electrolyzers use electricity to split water into hydrogen and oxygen.
Fuel cells use hydrogen and oxygen to generate electricity and produce water as a byproduct.
Similar to water electrolyzers, ion exchange membranes in fuel cells are key components of the membrane–electrode assembly (MEA), enabling selective ion transport. In proton exchange membrane (PEM) fuel cells, the membrane allows protons (H⁺) to pass from the anode to the cathode while blocking electrons, which flow through an external circuit to generate electricity.
Carbon Dioxide Utilization using Carbon Dioxide Electrolyzers
Electrochemical CO2 reduction reaction (CO2R) turns CO2 into chemicals and fuels using only water and renewable electricity. If CO2 is captured from the air, CO2R can help close the carbon cycle. It produces chemicals like ethylene or methanol in one step, unlike traditional methods that require multiple reactions. CO2 electrolysis operates at lower temperatures and pressures, using renewable energy sources like solar or wind, making it more energy-efficient than conventional processes. It also has no moving parts, allowing easy separation of products and making it ideal for mass production and automated maintenance. These features make CO2R a scalable, sustainable, and potentially carbon-negative solution for reducing CO2 emissions.
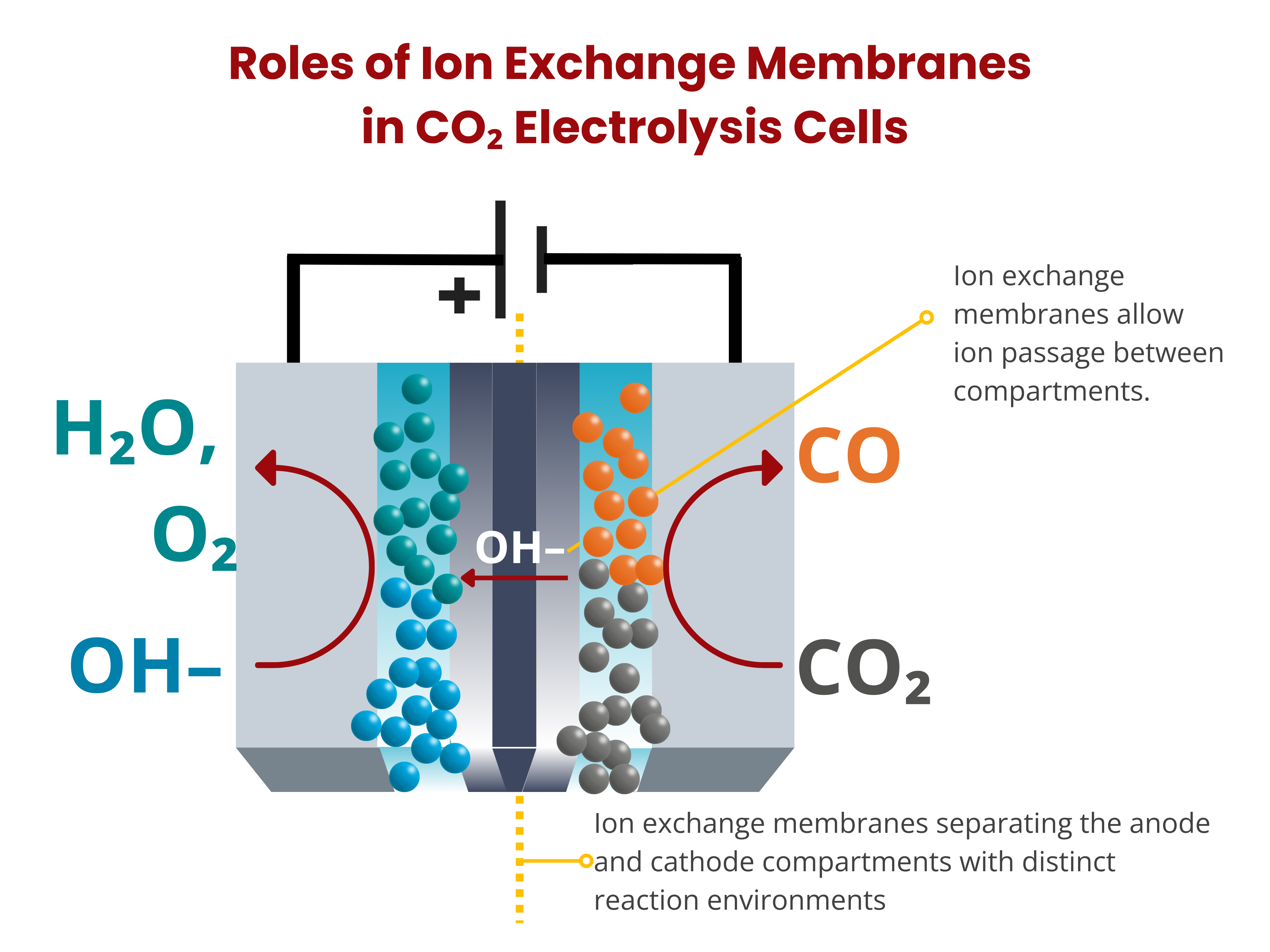
Ion exchange membranes play a crucial role in carbon dioxide electrolyzers by separating the anode and cathode compartments with distinct reaction environments. This separation prevents the crossover of products and their reoxidation to CO2, effectively enhancing CO2 utilization and conversion efficiency. Additionally, these membranes facilitate the completion of the electrical circuit, ensuring electroneutrality by allowing ion passage between compartments. Similar to those used in fuel cells and water electrolyzers, ion exchange membranes are an important component of CO2RR electrochemical cells that affect the cell voltage and the overall energy efficiency of the device.
What are ionomer powders?
Ionomer powders are a type of thermoplastic material that are widely used in several applications across various industries. These materials are characterized by their ability to conduct ions and offer a combination of mechanical and electrical properties, making them ideal for use in a variety of applications, such as:
Fuel Cells: Ionomer powders are used as a key component in the membrane electrode assembly (MEA) of fuel cells. The ionomer acts as a binder to hold the catalyst particles in place and also provides an ion-conducting path between the electrodes.
Battery Separators: Ionomer powders are used as separators in rechargeable batteries to prevent the electrodes from coming into direct contact, which would cause a short circuit. The ionomer's electrical conductivity and ability to conduct ions make it an ideal material for this application.
Coatings: Ionomer powders are used as a binder in coatings to improve adhesion, toughness, and abrasion resistance. These materials are commonly used in the coating of golf balls, where they provide an ideal balance between durability and softness.
Medical Devices: Ionomer powders are used in medical devices such as implants and sutures to improve strength, toughness, and biocompatibility. The materials are also used as coatings on medical devices to improve their biocompatibility and reduce the risk of adverse reactions.
Packaging Films: Ionomer powders are used in packaging films to improve strength, toughness, and heat resistance. These materials are commonly used in the production of shrink wrap and stretch wrap, where they provide an ideal balance between flexibility and durability.
In conclusion, ionomer powders have a wide range of applications, making them an essential component in several industries. Their combination of mechanical, electrical, and ion-conducting properties make them ideal for use in fuel cells, battery separators, coatings, medical devices, and packaging films.
Presentations
Related Blogs

Choosing the Right Ion Exchange Membrane for Your Water Electrolyzer and Fuel Cell Applications
This blog explores how to choose the right ion exchange membrane for water electrolyzers and fuel cells