Permasil 909C | Carnauba Wax Mold Release Spray
- Carnauba wax Mold Release Spray
- Solvent-based, non-flammable
- Compatible with Epoxy Mold Compound
Product Description
PRODUCT UPDATE! MJGordon #909C is no longer supplied.
MJGordon have stopped supplying Permasil #909C. Fortunately, CAPLINQ has an alternative product: Chemlinq MRE-C909
GORDON'S PERMASIL #909C (Green Label) Non-Flammable Solvent-Based (Green Label), 100% Non-Ozone Depleting 539gr Can Carnauba Wax Aerosol Spray, Industrial, and Automotive Applications. By far the most popular grade with more than 90% of this grade in use, this version uses a non-flammable solvent to suspend the carnauba particles making an easy choice for manufacturers.
CAPLINQ Europe BV is the exclusive distributor for MJ Gordon #909C in Europe
Technical Specifications
Additional Information
Additional information
Carnauba Wax Aerosol Spray will set your products free
GORDON'S PERMASIL #909C (Green Label) Non-Flammable Solvent-Based (Green Label), 100% Non-Ozone Depleting 539gr Can Carnauba Wax Aerosol Spray, Industrial, and Automotive Applications. By far the most popular grade with more than 90% of this grade in use, this version uses a non-flammable solvent to suspend the carnauba particles making an easy choice for manufacturers.
CAPLINQ Europe BV is the exclusive distributor for MJ Gordon #909C in Europe
Carnauba wax itself is nothing new. Carnauba is a natural wax derived from the carnauba palm, a palm tree native to the northeastern Brazil. It is used in a wide variety of applications including automotive waxes, shoe polishes, dental floss coatings, and paper coatings, the last of which is its most common application in the United States.
What makes this product so attractive is that it contains no silicone or Teflon® (DuPont trademark for the generic polytetrafluoroethylene or PTFE). While these ingredients may be well-suited for the release of rubber molds or to coat anti-stick surfaces, they rarely have a place when working liquid epoxy, epoxy molding compounds (EMC) and some other plastic types. Most semiconductor manufacturers know this of course, and use chunks of carnauba wax to break in new epoxy molds or to release the plunger when it sticks. Carnauba wax is compatible with epoxies and generally enhances its properties along with those of most other engineering plastics.
M.J. Gordon's Carnauba Wax Mold Release is dubbed as the "World's Finest Carnauba Wax Mold Release". What is unique about M.J Gordon's Carnauba Wax Release is the patented process of making it available in aerosol spray form. Typically, carnauba wax is only available in flakes, powder or clumps. These clumps are the same ones typically used by semiconductor manufacturers. What M.J. Gordon's aerosol spray version allows is uniformity, control, and the convenience of an aerosol spray.
"Unconditional Guarantee that every can will operate from its first spray until completely emptied without fail or the entire case of 12 cans will be replaced at no product nor freight cost to the customer."
Used worldwide by the leading manufacturers of semiconductors, capacitors, resistors, transformers, inductors, relays, electro-medical equipment and more, M.J. Gordon Mold Release Aerosol Formulas ensure that regardless of the product manufactured or the type of molding process performed, these quality products improve these operations. Not only do they offer the uniformity, control, and convenience of an aerosol spray, they actually enhance the Tensile Strength and Displacement Properties of highly engineered plastic resins as tested by an ISO9002 Certified Laboratory. Results of the tests are available upon request.
Many customers who have used other sprays in the past, whether it be Teflon® or silicone are amazed by the results they obtain after testing the carnauba wax aerosols. Semiconductor manufacturers in particular use this product regularly to break in new molds and after multiple shots of the epoxy mold compound. The carnauba wax prevents the epoxy mold compound from sticking in the mold-chase, rust-proofs the mold-chase and allows for easy release of the product from the chase once molded.
Current Commercial Applications:
- Epoxy Molding Compound Mold Release for Active Semiconductors (ICs, TQFPs, BGAs, etc.)
- Epoxy Molding Compound Mold Release for Passive Semiconductors (resistors, capacitors)
- Mold Release Agent for transformers, inductors, relays, and electro-medical applications
- New Mold Break-In
- Incomparable Part Release Characteristics
- Outstanding Rust Proofing Characteristics
Product Range of Carnauba Wax Aerosol Spray
There are only three versions of the solvent-suspended carnauba wax aerosol spray and by a long margin, the "Non-Flammable Green-Label" product is the most popular. This is due to its non-flammable solvent which makes it easier to ship internationally and makes is easier for customers to accept.
For all M.J. Gordon's products however, the above mentioned unconditional guarantee applies.
Permasil #909C: Non-Flammable, Solvent-Based (Green Label)
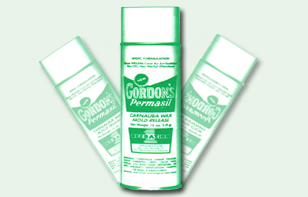
Permasil #909C: 539gr Can Carnauba Wax Aerosol Spray
By far the most popular grade with more than 80% of this grade in use, this version uses a non-flammable solvent to suspend the carnauba particles making an easy choice for manufacturers.
Permasil #808: Non-Flammable, Water-Based (Blue Label)
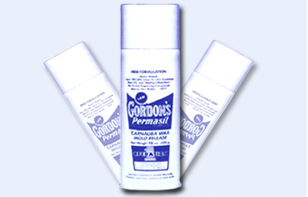
Permasil #808: 425gr Can Carnauba Wax Aerosol Spray
Taking up the majority of second place's demand, this grade is for use in applications where a water-based version must be used.
Permasil#909D: Flammable, Solvent-Based (Red Label)
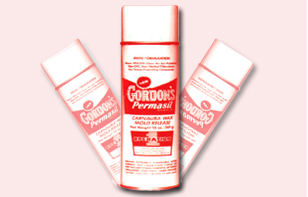
Permasil#909D: 369gr Can Carnauba Wax Aerosol Spray
With far less than 5% of market share, this product is only ever used when manufacturers' specifications require it. Otherwise, this product has been entirely superseded by the other two grades.
Alternatives
Having a hard time getting MJGordon#909C?CAPLINQ has spent several years developing an alternative to the industry standard MJ Gordon#909C. This alternative is still a Carnauba Wax based mold release agent but uses ingredients that take it off the SVHC list and can therefore be used as an excellent alternative for the MJ Gordon #909C. |
Material Compatibility
Material | #909 "C" SOLVENT BASED NON-FLAMMABLE (Green Label) | #808 "Aqueous" WATER BASED NON-FLAMMABLE (Blue Label) | #909 "D" SOLVENT BASED FLAMMABLE (Red Label) | |||
Tensile Strength | Maximum Displacement | Tensile Strength | Maximum Displacement | Tensile Strength | Maximum Displacement | |
ABS | A | A | A | A | A | A |
Acetal | A | A | A | A | A | A |
Acrylic | B | C | A | C | C | C |
Epoxy | A | A | A | A | A | A |
PEI | A | B | A | B | A | B |
PET | A | A | A | A | A | A |
Polycarbonate | A | C | C | C | A | C |
Polethylene | A | B | A | A | B | A |
Polypropylene | A | C | A | C | A | C |
PPO | A | C | A | C | B | C |
PPS | A | A | A | A | A | A |
SBR Rubber | A | C | A | C | A | B |
*A - Material Property Retention of 90-100+% .......................Highly Compatible | ||||||
*B - Material Property Retention of 80-89+% ........................Moderately Compatible | ||||||
*C - Material Property Retention of Less than 80% ................Not Compatible | ||||||
1. The products herein are for industrial use only; suggestions for use are made without warranty expressed or implied | ||||||
2. These data are intended as a guide; specific applicability must be ascertained through product testing within particular manufacturing conditions and parameters. | ||||||
3. Prior to use ALL LABEL WARNINGS as well as those within the Material Safety Data Sheet (MSDS.) must be read and understood. | ||||||
4. The testing was completed at an independent ISO 9002 certified laboratory. | ||||||
5. Additional Test Data as well as methodology available upon request. |
Troubleshooting
Defect Description | Try the following |
---|---|
Blistering, heavy section |
|
Thick Flash |
|
Porosity (not filled out in every section) |
|
Mold sticking |
|
Dull surface |
|
Orange peel (rough, pimply surface) |
|
Pitted surface |
|
Clouded or segregated surface. |
|
Dimpled surface |
|
Warped piece |
|
Cracking after molding |
|
Poor electrical properties |
|
Weak Mechanically |
|
Pimpling |
|
Burn Marks |
|