Bonding wires
Wire bonding is a solid phase welding process where the bonding wire and the pad surface are brought into contact under a combination of heat, pressure and potentially ultrasonic energy. Caplinq offers its own product line of high quality Bonding wires for capillary (ball) and wedge bonding used in LED, Sensor and chip to chip die bonding applications.
We offer Copper, Aluminum, Silver, Gold, Palladium, Palladium & Copper and Gold - Palladium - Copper bonding wires that are suitable for wedge and ball/crescent interconnects. They can be used for thermosonic, ultrasonic or thermo-compression inter metal processes and can be easily handled and threaded to the bond head.
Our bonding wires come into various diameters ranging from 18 and to 25 microns and are packaged in 1000m rolls .
Interested in protecting your wire bonded chip? Take a look at our Encapsulant and Underfills product category that includes a wide range of glob top and dam and fill encapsulation materials.
Au-Pd-Cu | Linqalloy Bonding wire
- 0.01 - 0.2% Gold Flash (Au)
- 1.2 - 2.5% Palladium Coating (Pd)
- Copper (Cu) Balance
- 4 - 6 weeks
Ag96 | Linqalloy Silver Bonding wire
- ±1% Gold Flash (Au)
- ±3% Palladium Coating (Pd)
- Silver (Ag) 96% Balance
- 4 - 6 weeks
Product Selector Guide
Alloy | Melting temperature (°C) | Elongation (%) | Diameter | |||
---|---|---|---|---|---|---|
18um -0.7mil | 20um -0.8mil | 23um -0.9mil | 25um -1mil | |||
Ag88 | - | - | ![]() | ![]() | ![]() | ![]() |
Ag94 | - | - | ![]() | ![]() | ![]() | ![]() |
Ag95 | - | - | ![]() | ![]() | ![]() | ![]() |
Ag96 | 980 - 1030 | 10 - 20 | ![]() | ![]() | ![]() | ![]() |
Ag99 | - | - | ![]() | ![]() | ![]() | ![]() |
PdCu | - | - | ![]() | ![]() | ![]() | ![]() |
AuPdCu | 1084 | 5 - 17 | ![]() | ![]() | ![]() | ![]() |
Cu99.99 | - | - | ![]() | ![]() | ![]() | ![]() |
Au76 | - | - | ![]() | ![]() | ![]() | ![]() |
Frequently Asked Questions
What are the most important aspects of wire bonding?
Proper threading is crucial to make sure that the process goes smoothly. Reverse, Tail, Tear, Search speed, search delay and force settings need to be optimised to make a reliable and lasting bond. If the substrate is not plated then cleaning and dehydrating the substrate by exposing it to high temperatures is important to achieve good metal adhesion.
The correct settings will also ensure that we can achieve high speed, economical, strong bonds that will allow for the maximum loops per second that our equipment allows.
What is the difference between the three major wirebonding methods?
Thermo compression
Thermocompression requires High pressure and an operating temperature ranging from 300-500°C. It is not compatible with ultrasonic energy, uses mostly Gold Wire and requires either a Gold or an Aluminium pad surface
Ultrasonic
Ultrasonic wire bonding requires low pressure and can operate in a temperature less than 80°C. It is compatible with ultrasonic energy, uses Aluminium bonding wires and can be applied in both Gold and Aluminium pads.
Thermosonic
Thermosonic process is the midlle ground. It operates in low pressure and in a temperature ranging from 100-150°C. As the name applies it is also compatible with Ultrasonic energy, used mostly Gold bonding wires and can also operate on both Aluminium and Gold pad substrates.
Learn More
A typical wirebonding process consists of the following steps:
- Formation of a Free Air Ball (FAB) with some pressure at the edge of the wire.
- Pressing this FAB onto the substrate to create
- Retreat of the head to the appropriate neck length
- Bending the wire and applying heat and pressure upon contact with the connection point
- Retracting the clamp and breaking the wire to finish the connection
Stand off stitch bonding
Standoff stitch bonding(SSB) bonds first to the substrate’s bond finger and second to a gold stud(previously applied with a separate wire bonding operation) on the chip’s bond pad. SSB enables < 100 um loops without damaging bonding wires. Wire breakage happen with low modulus DA when the wire passes through the DA/MC interface.
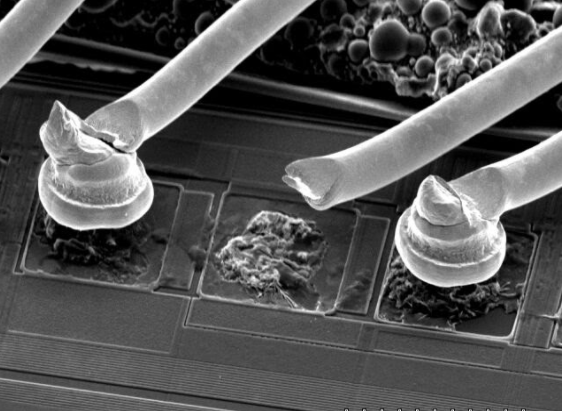
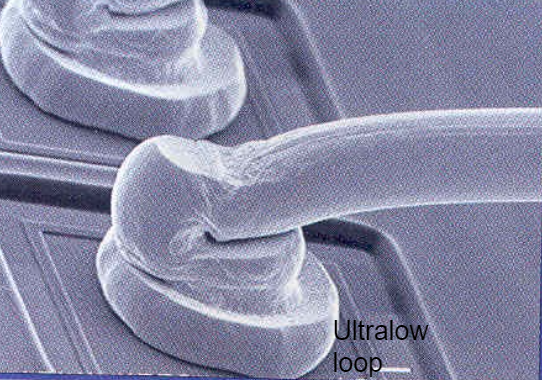
Ultralow loop
Ultralow loop bonding can achieve wire loops < 75 um without ball neck damage by using current ball bonding technology with a different wire trajectory tool. This method enables equipment productivity and long wire spans that are similar to conventional wire bonding. No wire breakage were reported even with low modulus DA because of stronger ball neck.g.
Annealed bonding wire micro-structure
Annealing is a heat treatment process that affects the microstructure of a given material in order to enhance its mechanical and chemical properties. It is mainly done to reduce the microhardness of a material in order to increase its ductility and make it more malleable and workable. It is being done by heating and keeping the material heated close its recrystalization temperature and then cooling it down.
In the image above we can see how the micro-structure of a 20um Copper bonding wire changes with temperature over the span of 1 hour. In these cross sections we can see the column and equiaxed grains and how they change with temperature, resulting in changes in microhardness, tensile strength, stress and elongation.
These are very important aspects since they directly affect the reliabiity and the failure rate of a device as you can see in the image below