OLS-1000HF | Liquid Encapsulant - Two part Epoxy
- Liquid epoxy encapsulant
- LED applications
- Low Halogen
Product Description
OPTOLINQ OLS-1000HF is a two-part (Part A & Part B), optically clear epoxy casting compound designed for the encapsulation of LED lamps and displays. It features excellent UV resistance, high optical transmittance, good adhesion to a range of substrates, and good thermal shock resistance. It is geared specifically for applications that will not be exposed to temperatures above 125 °C, and where the cost of the encapsulation material is a large percentage of the final part cost. The OLS-1000HF is the Low Halogen version of OLS-1000.
OPTOLINQ OLS-1000HF has been used extensively for low-power LED encapsulation, automatic LED casting, and potting of large optoelectronic modules. Each of these applications relies on the high clarity and other optical properties of the OLS-1000HF as well as its excellent mechanical properties. The OLS-1000 can be colored and diffused by the addition of specific dye concentrates and diffusant concentrates. This product is not made for SMD encapsulation but mainly for DIP packages.
Technical Specifications
General Properties | |||||||
Pot Life Pot Life Pot life is the amount of time it takes for the viscosity of a material to double (or quadruple for lower viscosity materials) in room temperature after a material is mixed. It is closely related to work life but it is not application dependent, less precise and more of a general indication of how fast a system is going to cure. | 4 hours | ||||||
Refractive index Refractive index The refractive index determines how much the path of light is bent, or refracted, when entering a material. It is calculated by taking into account the velocity of light in vacuum compared to the velocity of light in the material. The refractive index calculation can be affected by the wavelength of light and the temperature of the material. Even though it is usually reported on standard wavelengths it is advised to check the TDS for the precise test parameters. | 1.51 | ||||||
Chemical Properties | |||||||
Water Absorption | 0.3 % | ||||||
Electrical Properties | |||||||
Dielectric Strength Dielectric Strength Dielectric strength is measured in kV per mm and is calculated by the Breakdown voltage divided by the thickness of the tested material. Those two properties go hand in hand and while Breakdown voltage is always thickness dependent, dielectric strength is a general material property. As an example, the dielectric strength of Polyimide is 236 kV/mm. If we place 1mm of Polyimide between two electrodes, it will act as an insulator until the voltage between the electrodes reaches 236 kV. At this point it will start acting as a good conductor, causing sparks, potential punctures and current flow. | 20 kV/mm | ||||||
Visible Light Transmission | 98 % | ||||||
Volume Resistivity Volume Resistivity Volume resistivity, also called volume resistance, bulk resistance or bulk resistivity is a thickness dependent measurement of the resistivity of a material perpendicular to the plane of the surface. | 6.4x1015 Ohms⋅cm | ||||||
Mechanical Properties | |||||||
| |||||||
| |||||||
| |||||||
| |||||||
| |||||||
Thermal Properties | |||||||
| |||||||
| |||||||
Glass Transition Temperature (Tg) Glass Transition Temperature (Tg) The glass transition temperature for organic adhesives is a temperature region where the polymers change from glassy and brittle to soft and rubbery. Increasing the temperature further continues the softening process as the viscosity drops too. Temperatures between the glass transition temperature and below the decomposition point of the adhesive are the best region for bonding. The glass-transition temperature Tg of a material characterizes the range of temperatures over which this glass transition occurs. | 159 °C |
Additional Information
Processing Instructions
Pre-heat agent A at 45–60 °C for a maximum of 4 h, depending on the temperature and season.
Mix components A and B in a certain proportion and stir uniformly.
Defoam the mixture.
Curing conditions :
- Size Φ3: First cure at 130–135 °C/1 h, followed by post cure at 130–135 °C/6–8 h.
- Size Φ5: First cure at 125–130 °C/1 h, followed by post cure at 130–135 °C/6–8 h.
- Sizes Φ8, Φ10: First cure at 105–120 °C/1 h, followed by post cure at 130–135 °C/6–8 h.
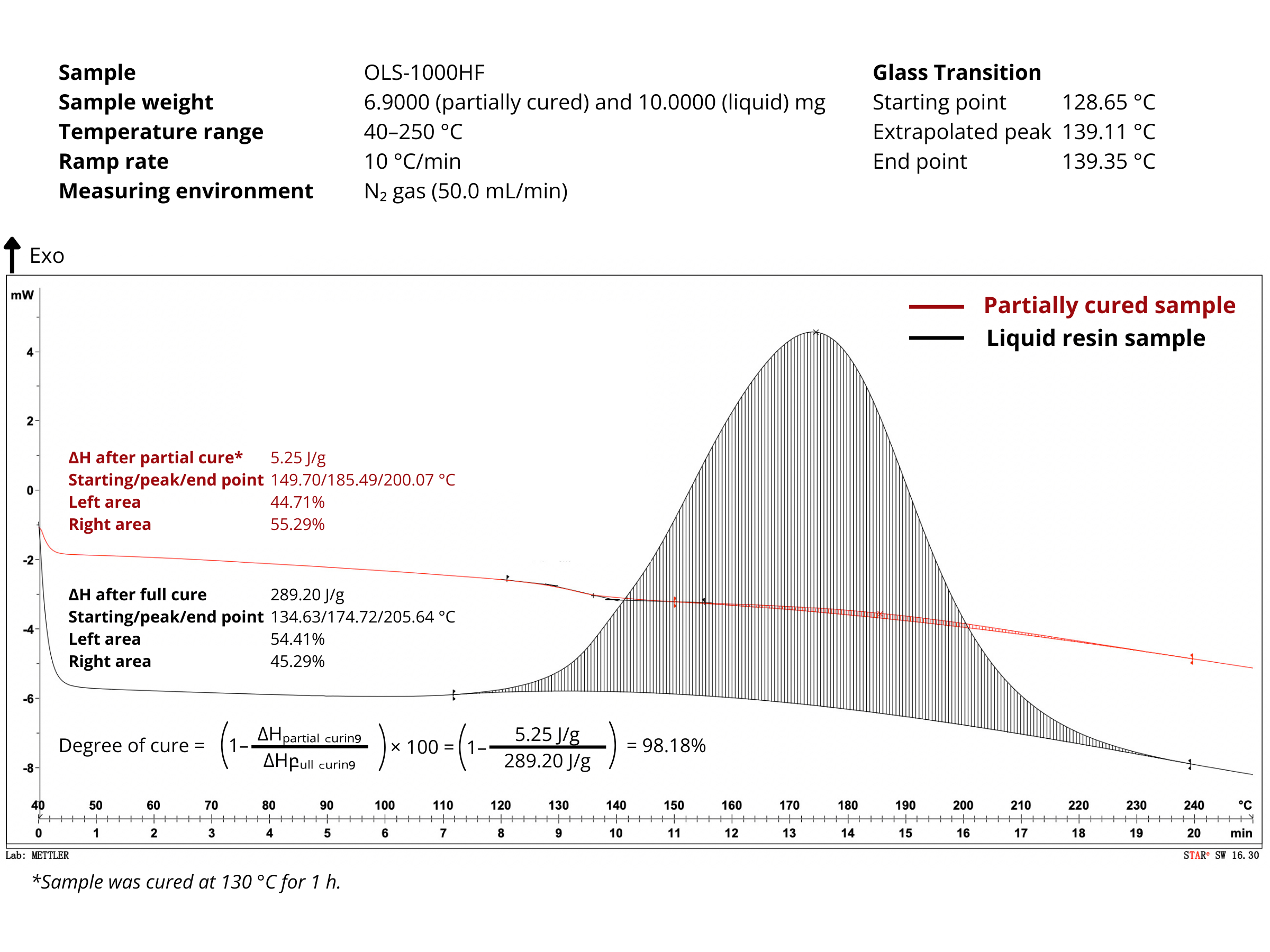
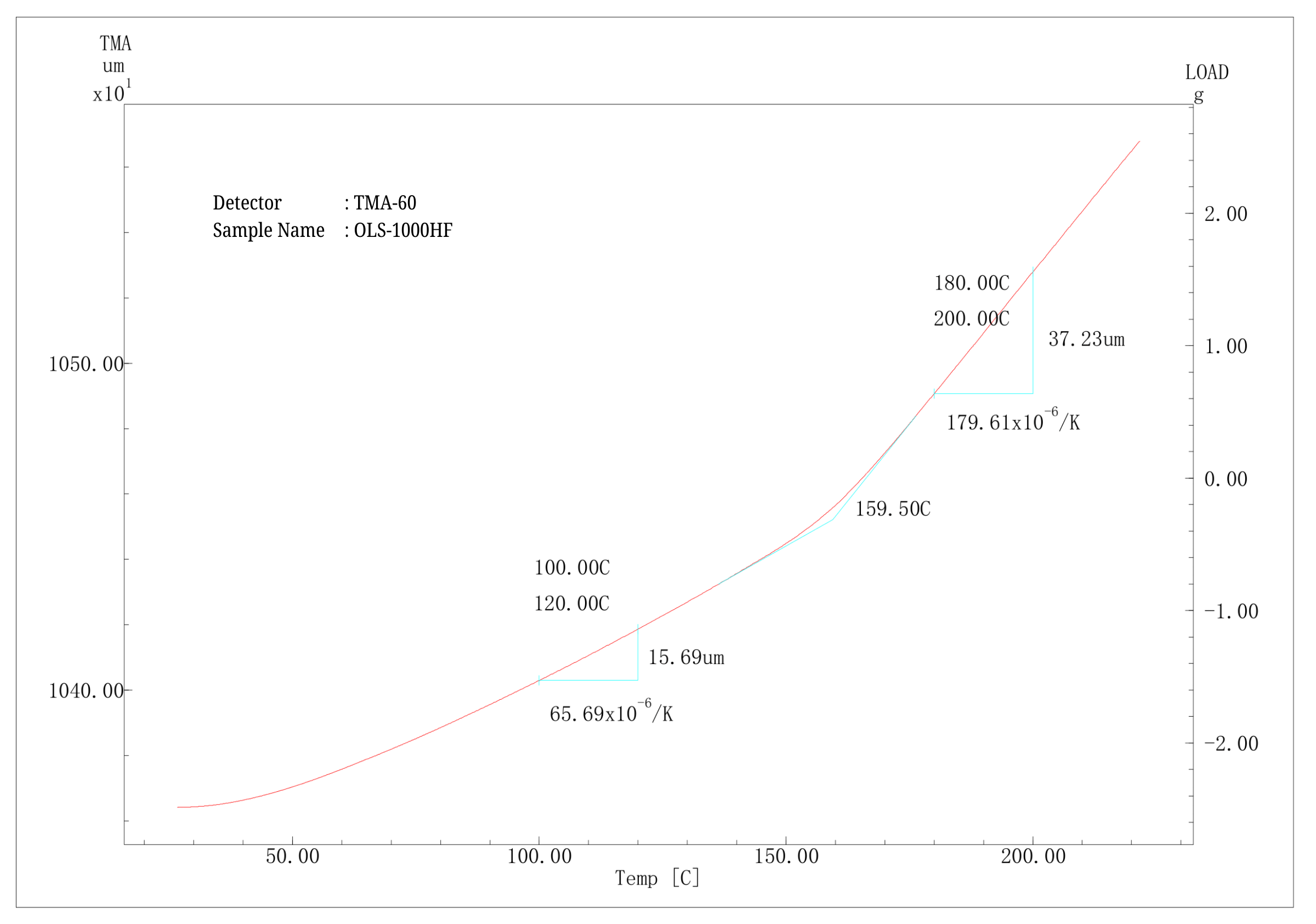
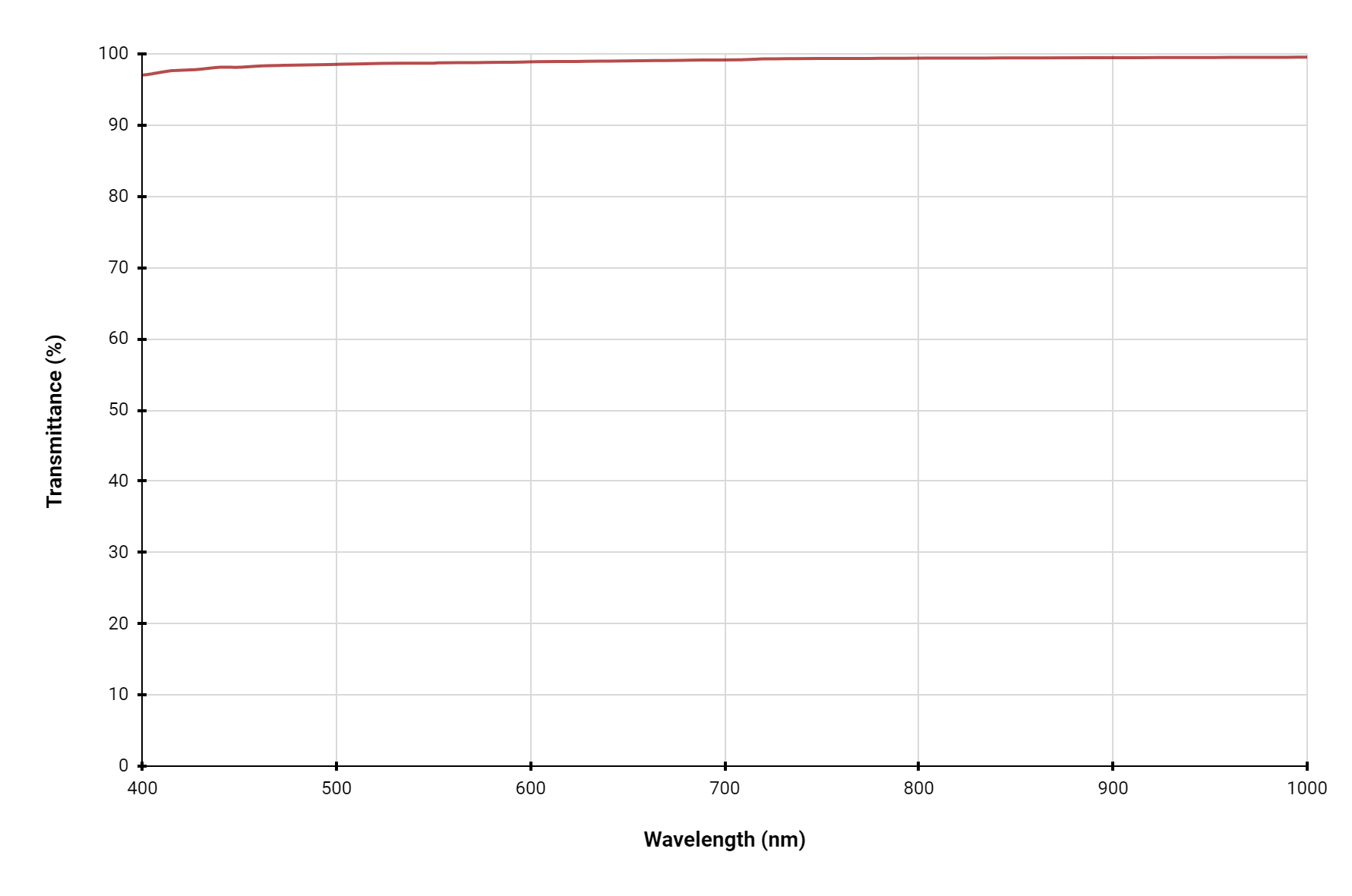
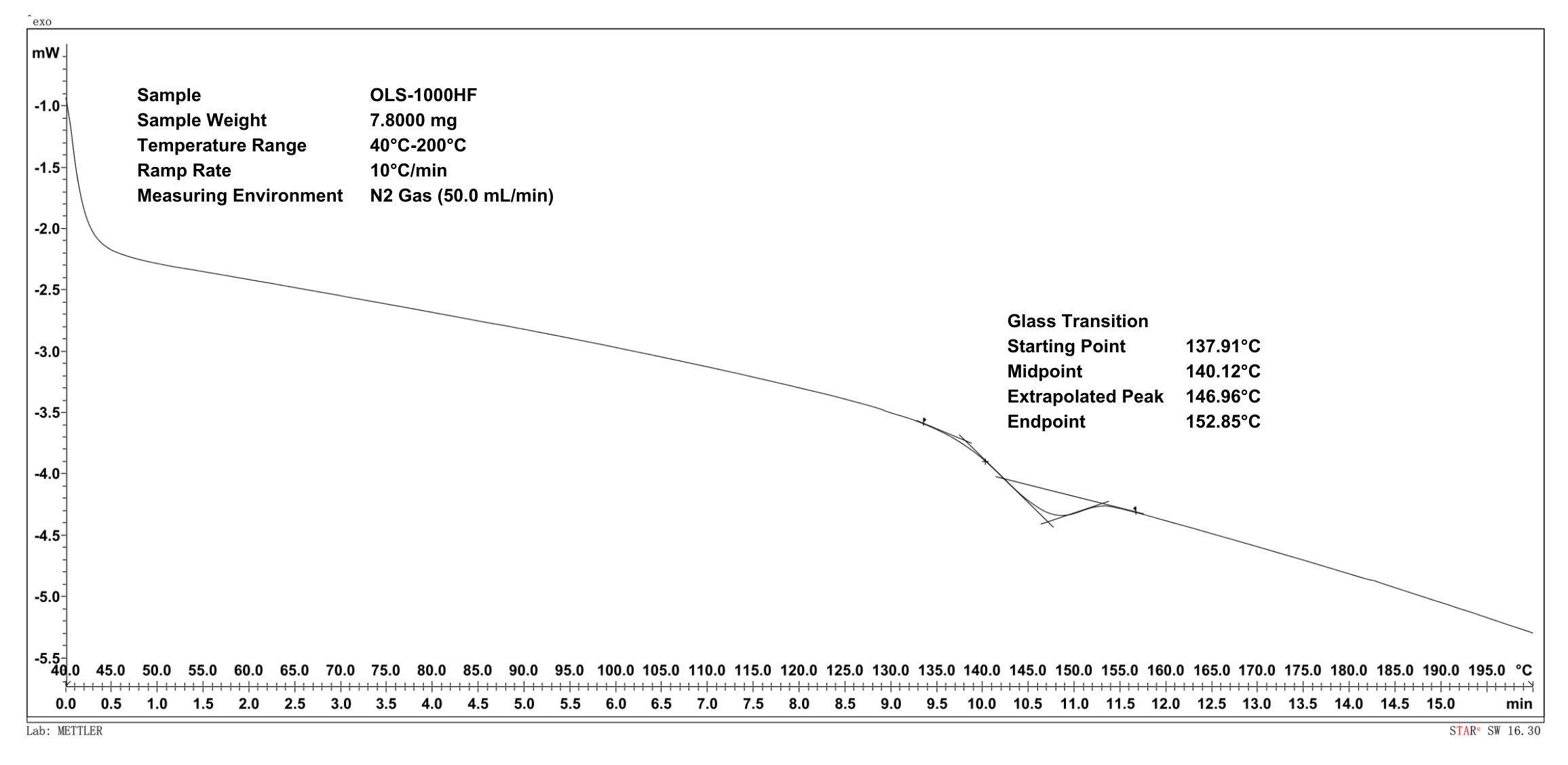
Using Additives
Optolinq OLS-1000HF can be mixed with diffusing agents or color pastes to achieve customer-specific purposes.
Recommended quantity (in weight %) of various diffusing agents and color pastes to be used with OLS-1000HF:
- OCP01-R Red Color Paste: 2-5% by weight
- OCP01-B Blue Color Paste: 1-3% by weight
- OCP01-G Green Color Paste: 2-4% by weight
- ODF-10 Diffusing Agent: 2-5% by weight
Values with our latest pastes and agents TBD.
Storage and Handling
OPTOLINQ OLS-1000HF is supplied in cans and jars and should be kept in a cool (10°C – 25°C) dry place (40% – 75% humidity) away from direct sunlight or temperature extremes. Part B is particularly sensitive to moisture, so be sure to remove moisture after using and to keep the lid of the container tightly sealed after use.
Under these conditions, the shelf life of Part A is 6 months and the shelf life of Part B is 3 months. The data contained herein may be reported as typical value and/or range values based on actual test data and are verified on a periodic basis.
OLS-1000HF Beta Site Performance in E*
Material Properties
Material | Tg | delta CTE | Curing temperature | Refractive Index | Halogen Content | Resistivity | Hardness | Modulus | Water absorption | Viscosity |
CAPLINQ OLS-1000 | 125 | 59 | 110 | 1.51 | Fl, Br, I = < 50 ppm Cl ~696 ppm | Electrically non-conducting | > 88 | 3.4 GPa | < 0.35 | ~1,000 |
Initial Assessment
Test | Remarks |
Shore D | PASSED – Shore D measurements were consistent w/ expected values in TDS |
Transmission Test | PASSED – High transmittance at ~905 nm and comparable w/ current material |
Degree of cure | PASSED - >90% degree of cure obtained from DSC (also consistent w/ Shore D readings) |
Tg | PASSED – Tg values obtained from DSC were close (+/- 20C) from the declared Tg in TDS |
Ease of Dispensing | PASSED – Can be dispensed using current tapered plastic dispense needle and current dispensing machine |
Curing Profile | PASSED – Compatible w/ current conventional convection oven in the production line |
Material Preparation | PASSED – No problems encountered in 1:1 mixing and Thinky Mixer procedure to mix |
Sample build using dummy units
- No other visual defects observed post-cure.
- No cracks, no delamination (time zero), no voids and bubbles, no leak, no cloudy encapsulation.
Good units build for WHTOL
- No issues encountered during production build for WHTOL.