Printed Circuit Boards (PCBs)
What is a PCB?
A PCB or Printed Circuit Board is an electronic assembly used in almost every modern electronic device. It is a multi-layered component that uses copper tracing to create communication pathways. Through these pathways, electricity travels to the various components that are mounted onto the surface of the PCB.
How is a PCB Manufactured?
Generally, PCB manufacturing varies greatly based on the type of PCB and manufacturing techniques. PCBs typically start out as a copper-clad laminate, which is then fused to an insulating substrate made of fiberglass-reinforced epoxy, commonly known as FR-4. The PCB design and pathways are created through specialized PCB design software, and then the design is generated and used to guide the manufacturing process. It is then dipped in a chemical bath which etches away the copper in the design not covered by the stencil so that when the stencil is removed the copper conductive traces remain.
After many processing and inspection steps, electronic components like resistors and capacitors are soldered to the board. To create functional circuits, the leads are connected to the conductive traces. Then, a silkscreen layer is printed on top of the board, which contains text and symbols that act as identifiers for the different components.
Finally, the sheet is covered in a solder mask, protecting the board from corrosion and debris. This mask is what gives the PCB its characteristic green color, however, solder masks also come in colors like blue or black. Most importantly, solder masks are what provide the board with electrical insulation.
What is a Flexible PCB?
A category of PCBs is a flex PCB. As the name suggests, this printed circuit board is made with flexible materials, opening up more opportunities for use in constrained areas where flexibility is required. Like a rigid PCB, the flex PCB contains copper tracing communications pathways. The main difference is that instead of a rigid fiberglass-reinforced epoxy substrate, flex PCBs are made with a non-conductive polymer substrate like polyimide or polyester.
Manufacturing a PCB with these materials makes it bendable and light, which can be extremely beneficial in applications where there are space constraints or weight requirements.
In some cases, rigid and flex PCBs are combined to create a rigid-flex PCB. This is a hybrid circuit board that combines both technologies to create a customizable PCB, which can be very fitting to specific applications where rigidity but also flexibility is required.
How to Protect a PCB with Conformal Coatings
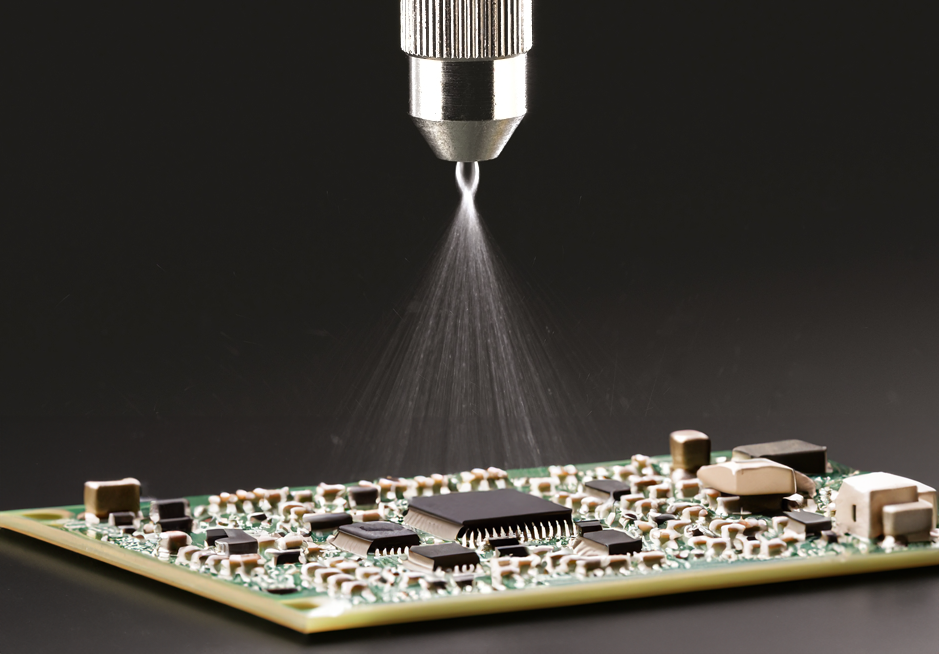
An easy way to protect a PCB and increase its longevity is to apply a Conformal Coating. A conformal coating is a thin film specifically designed to safeguard electronic assemblies. It can protect from dust, corrosion, and moisture, by creating a coating that envelopes the PCB and all its components. Conformal coatings also insulate the PCB, protecting it from electrical failures.
There are different types of conformal coatings based on requirements, including acrylic (Loctite Stycast PC 62), polyurethane (Loctite Stycast PC 18M), silicone (Loctite SI 5293), uv-based (Loctite Stycast PC 40-UMF) and rubber based.
How to Protect a PCB with Aculon's Electronic Grade Coatings
Another protection method for electronic components and circuitry are 3M Novec Alternatives, or Electronic Grade Coatings. Aculon's Nanoproof™ 3 Series are specialized coatings designed to replace the now discontinued 3M Novec coating line, which protects electronic components like PCBs from environmental factors such as humidity, heat, and corrosion. They are used in various industries to ensure the longevity and reliability of electronic devices by providing a protective barrier against moisture, dust, and other contaminants that can interfere with their functionality.
Electronic grade coatings are typically applied as a thin layer over electronic components or circuitry to provide a barrier against environmental contaminants, moisture, and corrosive agents. These coatings can be applied through various methods, including spray, dip, or brush application, and can be cured through heat or UV light.
The target thickness of the coatings is based on fluoroacrylate % and varies from as low as <1 μm (Nanoproof 3-001X) up to 6 μm (Nanoproof 3-10).
Nanoproof Alternative | 3M Novec Product |
---|---|
Novec 1720 | |
Novec 1702 | |
Novec 1700, 1902 | |
Novec 1904, 2704 | |
Novec 1908, 2708 | |
Nanoproof 3-10 | Novec 1710 |
Novec 7100 |
How to Waterproof a PCB with Aculon's PCB Waterproofing Treatments
Certain applications may require waterproofing, such as underwater equipment or electronics like smartphones and watches. In these cases, nanocoatings are a great way to achieve various levels of waterproofing. Aculon's PCB Waterproofing Treatments provide an extremely thin coating that adds hydrophobicity without altering the surface of the PCB. The goal of these treatments is to protect the PCB from short circuits and other damage caused by moisture, which can cause corrosion and degrade the performance of the circuit over time.
Aculon's NanoProof™ Series offers customers a range of PCB waterproofing solutions from protecting against accidental water damage to IPX7, immersion in water at one-meter depth for 30 minutes, to greater barrier properties that can withstand 100 hours of immersion in sweat solutions and some of the most stringent test methods developed for non-hermetic components. Some Waterproofing Treatments Caplinq offers include:
- Nanoproof 1.0 - IPX4, best for a broad range of substrates
- NanoProof 2.1 - best for PCBs and electronic components
Treatments depend on various factors including substrate, hydrophobicity or oleophobicity level, coating thickness, etc.
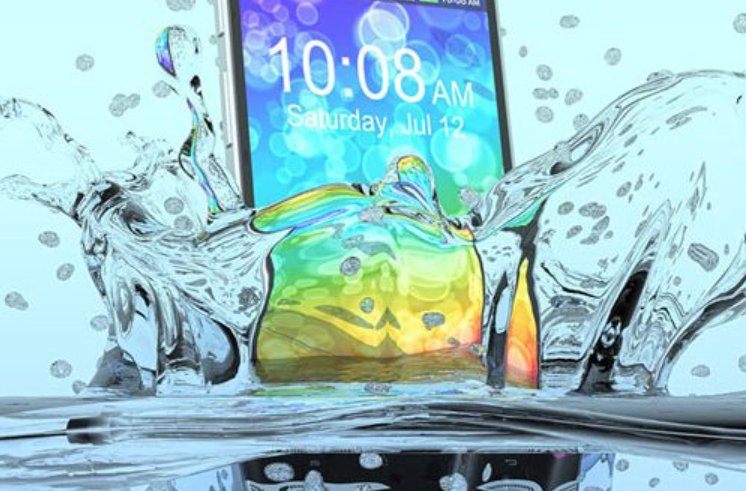