Thermal Gap Pads
Thermal Gap Pads (TGPs) provide high thermal performance with ease of use for many applications. Ultra-high compressibility enables low stress and excellent conformity to mating surfaces. Honeywell Thermal gap pad models are naturally tacky, and require no additional adhesive which could inhibit thermal performance.
Thermal gap pads provide thermal performance with ease of use across a multitude of applications. They have been designed to minimize thermal resistance at interfaces, exhibit minimal bleeding and maintain effective performance through reliability testing. TGP models are silicone based, therefore they offer a certain anti-shock effect, with electrical isolation and non-flammability. While all interfaces bleed (with zero exceptions), our pads exhibit very low bleeding even under pressure due to the low molecular weight of the remaining unlinked chains.
A range of thicknesses from 0.5mm to 5.0mm are available. Honeywell TGP models come with two surface liners, which enable users to remove the liner after installation (before operation), with no contaminant risk and easier handling.
TGP 1200 | Thermal Gap Pad
- 1.03 Thermal Impedance
- 1.2 Thermal Conductivity
- Competitive cost of ownership
- 8 weeks
TGP 2000E | Thermal Gap Pad
- 0.95 Thermal Impedance
- 2.0 Thermal Conductivity
- Excellent surface wetting
- 8 weeks
TGP3000E | Thermal Gap Pad
- 0.65 Thermal Impedance
- 3.0 Thermal Conductivity
- Excellent surface wetting
- 8 weeks
TGP 1500 | Thermal Gap Pad
- 0.94 Thermal Impedance
- 1.5 Thermal Conductivity
- 0.5 - 5 mm Thickness
- 8 weeks
TGP 3000 | Thermal Gap Pad
- 0.65 Thermal Impedance
- 3.0 Thermal Conductivity
- Low pressure versus deflection
- 8 weeks
TGP 5000 | Thermal Gap Pad
- 0.3 Thermal Impedance
- 5.0 Thermal Conductivity
- Good elastic modulus
- 8 weeks
TGP 6000 | Thermal Gap Pad
- 0.25 Thermal Impedance
- 6.0 Thermal Conductivity
- Excellent surface wetting
- 8 weeks
TGP 8000 | Thermal Gap Pad
- 0.2 Thermal Impedance
- 8.0 Thermal Conductivity
- Low oil bleeding/Outgassing
- 8 weeks
TGP 8000HV | Thermal Gap Pad
- 0.2 Thermal Impedance
- 8.0 Thermal Conductivity
- High Breakdown Voltage
- 8 weeks
Product Selector Guide
Product name | Color | Thickness (mm) | Hardness (Shore00) | Specific Gravity | Thermal Conductivity (W/m·K) | Thermal Impedance(˚C·in2/W)(1mm@10psi)1 | Dielectric Strength (kV/mm) | Dielectric Constant @1MHz | Volume Resistivity (ohm·cm) | Flammability Rating |
---|---|---|---|---|---|---|---|---|---|---|
TGP1200 | Blue | 0.5-5 | 30 | 1.7 | 1.2 | 1.03 | 5 | 4.5 | 4.0 x 1012 | V-0 |
TGP1500 | Grey | 0.5-5 | 40 | 1.8 | 1.5 | 0.94 | 5 | 5.5 | 2.0 x 1013 | V-0 |
TGP3000 | Yellow | 0.5-5 | 40 | 3.1 | 3.0 | 0.65 | 5 | 6.6 | 4.8 x 1013 | V-0 |
TGP5000 | Blue | 0.5-5 | 45 | 3.3 | 5.0 | 0.3 | 5 | 5.0 | 8.0 x 1013 | V-0 |
TGP6000 | Grey | 0.5-5 | 40 | 3.3 | 6.0 | 0.25 | 5 | 8.5 | 3.79 x 1015 | V-0 |
TGP8000 | Grey | 0.5-5 | 30 | 3.4 | 8.0 | 0.2 | 5 | 8.3 | 6.47 x 1015 | V-0 |
TGP8000HV | Grey | 0.5-5 | 60 | 3.5 | 8.0 | 0.2 | 8 | 8.3 | 6.47 x 1015 | V-0 |
All values mentioned above are typical values and not product specifications. The technical data contained herein are intended as reference only. Please contact Honeywell or Caplinq for assistance and recommendations on specifications for this product.
Frequently Asked Questions
What is the standard size and tolerance of Thermal gap pads?
TGP model thermal gap pads are available in standard sheets and also custom die-cut parts, and in a range of thicknesses. It is very important to understand that the applied pressure will directly affect the bondline thickness and the thermal impedance values
Thickness Range: 0.5-5.0mm with 0.25mm incremental
Thickness Tolerance: >1mm, ±10% 0.5-1mm, ±0.1mm
What happens after the expiration date?
Product shelf life is guaranteed when it is stored in the suggested conditions under controlled humidity. After the product "expires" the most readily observed response is precut pads (kiss-cut) tend to stick to each other and there is difficulty peeling out one without damaging adjacent one. There will be some viscosity change that may or may not affect thermal performance and we will not test or recertify material. We will not be liable for product quality or performance issues if expired parts are used in manufacturing.
What is the risk involved in using PCM Materials after the shelf life?
The material could potentially still be used after the shelf life. The risk involve in using materials after their shelf life is the inherent moisture absorption of all polymers, including these PCM materials as well. Moisture related failures are a big concern, and could severely impact the TIM performance. However, an expert in TIMs shared that if the material is baked (>100 °C) for a certain period of time (~30 min), the build up moisture could be evaporated quite easily and used afterwards. We will not be liable for product quality or performance issues if expired parts are used in manufacturing.
What is the operating temperature of Thermal Gap Pads?
Thermal Gap Pads are normally used in operating temperatures up to 80°C - this being the maximum temperature of the surrounding area. However, because of chemistry of these pads, they can easily withstand temperatures from -60 up to 200°C
What is the dielectric strength of Thermal Gap Pads?
Unless it is otherwise listed, the dielectric strength of the gap pads is around 5 - 7 kV/mm while High voltage versions have a dielectric strength around 7.6 - 7.9 kV/mm. Since air voids can occur it is hard to guarantee the exact Breakdown Voltage but you can take 5000V as the base value for non HV version pads. We are actively researching higher Dielectric Strength product versions. Contact us for developmental pads that can reach up to 9.6 kV/mm.
Learn More
A gap filler material is a type of thermal interface material to fill the gap (>0.5mm), while phase change material and thermal grease are designed for thin bondline thickness (<0.1mm) applications. It is expected to be compliant enough to deflect to accommodate multiple module heights and tolerance variation within applications without generating excessive levels of pressure within the system. Thermal gap pads, thermal putty pads, two-part hybrid gels, and one-part hybrid gels are all considered as gap filler materials.
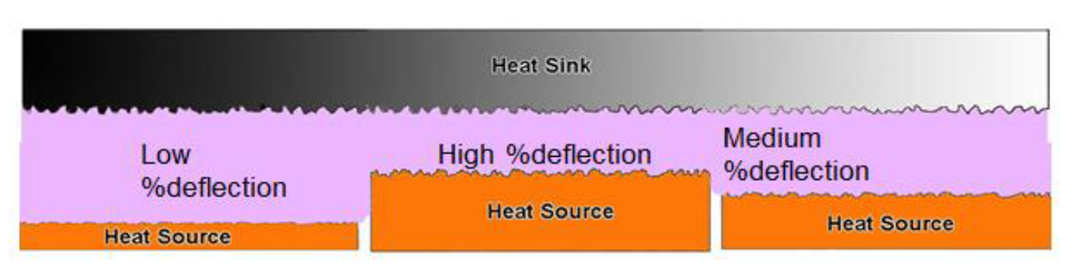
Key Features Of Gap Filler
- Gap fillers are usually silicone based because silicone has so many attractive properties such as excellent surface wetting, high thermal stability, flexibility and physiological inertness. The silicone matrix is filled with thermally conductive fillers such as boron nitride, zinc oxide or alumina. These fillers make up the functional portion of the gap filler which give it its thermal properties.
- Standard thicknesses of gap fillers tend to be 0.25-5mm (10-200 mils) and most have thermal conductivity ranging from 0.5 to 10 W/mK.
- Gap fillers are often expected to deflect 10 to 70 % of their initial thickness (compression) without generating excessive pressure and bleeding issues.
- These materials are usually delivered as die cut parts between release films, on a roll, as sheets or in cartridges for automated dispensing
Thermal conductivities, boneline thickness and reliability capabilities are the most important considerations for TIM selection. This also works for thermal fillers like thermal gap pads. However, there are some other features need to be considered specifically for gap filler pads:
- Compression - Some compression (at least 10% compression) is required to overcome/decrease the contact thermal resistance. The relationship between deflection and compression is not linear. You could find the Stree-Strain Curve of compression properties on each product page. For example, the figure below shows the TGP8000 and high breakdown volatge version TGP8000HV's compressibility and how TI (thermal impedance) & Thickness change by compression ratio.
- Thickness Tolerance - When starting the design process, identify the nominal gap and know the tolerances. The thickness range of thermal gap pads we provide is 0.5-5.0mm with 0.25mm incremental. Thickness Tolerance: ±10% while thickness>1mm; ±0.1mm while thickness is 0.5-1mm
- Hardness - Ideally, the softer the gap filler material, the better, since high assembly pressure may cause gap bleeding out and components deformation. However, materials that have a higher thermal conductivity and more curing extent, the harder it gets due to the high filler content. It is harder for high TC product to own elasticity and bounce back while pressure is moved away.
- Additional Layer - Some reinforcement carriers might be added on normal gap pads to enhance sepcific properties as customers need. Some common ones are:
- Woven Fiberglass (no PSA) to provide reinforcement against tearing down and a clean low tack interface surface
- Polyimide Film Or PEM Film to offer an excellent dielectric strength and permit gap pad to see a shearing motion
- Aluminum Foil (with PSA) to allow a pressure sensitive adhesive on the gap pad
The biggest issue we face with silicone pads is bleeding. Surprisingly enough there are no set test methods to control bleeding of Thermal gap pads. As a general rule of thumb there's NO thermal gap pad in the industry right now that doesn't bleed. Silicone pads can and will bleed given the right circumstances, regardless of manufacturer. That doesn't mean that Silicone free pads are not prone to it. Silicone free pads will also bleed. They will just not bleed Silicone.
Bleeding is different than outgassing. It concerns longer molecular chains and it depends on a variety of parameters. Bleeding depends on the pressure differential on the pad, how much free (not cross linked) silicone remains and the molecular weight (length) of the remaining unlinked chains. In this case, pressure plays a much bigger role than heat and orientation.
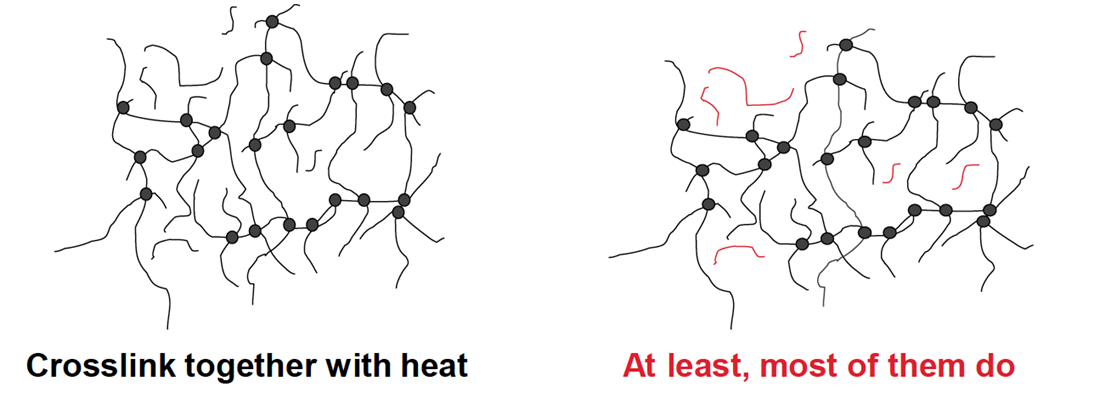
Compared with competitors, we minimize bleeding largely. Check the comparison of bleeding results below.
While bleeding tests are not standardized, Dielectric strength testing is quite straightforward. The sample is placed between two 25 x 25mm Copper electrodes in ambient temperature and 65% ambient relative humidity while the voltage is raised by 0.1kV/s until the AC current crosses through. Optically, this cross through is usually in a form of a pinch/hole in the material, sometimes invisible to the bare eye. Test are being conducted in a Dielectric strength tester - HJC-10KV at the time of writing of this content.
Honeywell's TGP8000HV have the lowest Thermal impedance out of all the entire thermal gap pad portfolio, plus higher breakdown voltage than the plain TGP8000 version. Check the dielectric strength data of TGP8000HV below.