Phase Change Materials
Phase change materials (PCM) are often used as matrix materials for thermal interface applications, because they are solid at room temperature, and soften when heated. They can fully fill the gaps of contact surfaces, therefore providing a thin bondline and high reliability without pump-out issues. This is achieved by adding a TC filler to the PCM matrix which forms a phase change composite with high heat transfer performance.
We offer silicone free, thermally conductive Phase Change Materials in both pad and paste formats. These products are designed to minimize thermal resistance at interfaces and maintain stable performance through the rigorous reliability testing required for long product life applications. Pastes are exactly the same as the pad versions with the addition of solvent that makes them screen printable and ideal for IGBT.
Based on a robust polymer PCM structure, these materials exhibit effective wetting properties during typical operating temperature ranges, resulting in very low surface contact resistance. With a breakdown temperature of ~180°C they provide superior reliability and maintain low thermal impedance, making PCM desirable for high-performance integrated circuit devices.
LTM 6300-SP | Phase Change Paste
- 0.12 - 0.14 Thermal Impedance
- 1.8 - 2.4 Thermal Conductivity
- Highest volume resistivity
- 8 weeks
PCM 45F | Phase Change Pad
- 0.09 - 0.12 Thermal Impedance
- 2.0 - 2.5 Thermal Conductivity
- Pad form
- 8 weeks
PCM 45F-SP | Phase Change Paste
- 0.09 - 0.12 Thermal Impedance
- 2.0 - 2.5 Thermal Conductivity
- High volume resistivity
- 8 weeks
PTM 5000 | Phase Change Pad
- 0.06 - 0.08 Thermal Impedance
- 3.5 - 4.5 Thermal Conductivity
- Pad form
- In stock
PTM 5000-SP | Phase Change Paste
- 0.06 - 0.08 Thermal Impedance
- 3.5 - 4.5 Thermal Conductivity
- Stencil Printable
- 8 weeks
PTM 6000 | Phase Change Pad
- Higher reliability than PTM5000
- 3.5 - 4.5 Thermal Conductivity
- Pad form
- 8 weeks
PTM 6000HV | Phase Change Paste
- 0.14 Thermal Impedance
- 5.2 Thermal Conductivity
- Optimized for IGBT
- 8 weeks
PTM 7000-SP | Phase Change Paste
- 0.06 Thermal Impedance
- 6.5 Thermal Conductivity
- Paste form
- In stock
PTM 7000-SPM | Phase Change Paste
- 0.06 Thermal Impedance
- 6.5 Thermal Conductivity
- Medium drying solvent
- 8 weeks
PTM 7900-SP | Phase Change Paste
- 0.045 Thermal Impedance
- 8.0 Thermal Conductivity
- Paste form
- 8 weeks
PTM 7950-SP | Phase Change Paste
- 0.04 Thermal Impedance
- 8.5 Thermal Conductivity
- Paste form
- In stock
PTM 7950-SPS | Phase Change Paste
- 0.04 Thermal Impedance
- 8.5 Thermal Conductivity
- Slow drying solvent
- 8 weeks
RTM-X22 | Pluggable Phase Change Pad
- 0.7 Thermal Impedance
- >50 Pluggable performance
- 0.15 - 0.22mm Thickness
- 8 weeks
Product Selector Guide
Product name | Specific Gravity | Thickness Range (mm) | Thermal Conductivity (W/m·K) | Thermal Impedance @ no shim (˚C·cm2/W) | Volume Resistivity (ohm·cm) |
---|---|---|---|---|---|
LTM 6300-SP | 1.8 | 0.20-1.00 | 1.8-2.4 | 0.12-0.14 | 3.0×1015 |
PCM 45F-SP | 2.2 | 0.20-1.00 | 2.0-2.5 | 0.09-0.12 | 8.2×1014 |
PTM 5000 | 2.3 | 0.20-1.00 | 3.5-4.5 | 0.06-0.08 | 2.1×1014 |
PTM 5000-SP | 2.3 | 0.20-1.00 | 3.5-4.5 | 0.06-0.08 | 2.1x1014 |
PTM 6000 | 2.3 | 0.20-1.00 | 3.5-4.5 | 0.06-0.08 | 2.1×1014 |
PTM 6000HV | 2.6 | 0.20-1.00 | 5.2 | 0.09 | 2.1×1014 |
PTM 7000 | 2.7 | 0.20-1.00 | 6.5 | 0.06 | 2.1×1014 |
PTM 7000-SP | 2.7 | 0.20-1.00 | 6.5 | 0.06 | 2.1x1014 |
PTM 7000-SPS | 2.7 | 0.20-1.00 | 6.5 | 0.06 | 2.1x1014 |
PTM 7900 | 2.8 | 0.20-1.00 | 8.0 | 0.045 | 2.1×1014 |
PTM 7900-SP | 2.8 | 0.20-1.00 | 8.0 | 0.045 | 2.1x1014 |
PTM 7950 | 2.8 | 0.25 | 8.5 | 0.04 | 2.1×1014 |
PTM 7950-SPS | 2.8 | 0.25 | 8.5 | 0.04 | 2.1x1014 |
Frequently Asked Questions
What are some typical PCM applications?
Typical phase change material Applications include:
- Power control unit, inverter, onboard electronics, IGBT
- Auto electronics, traction power inverters, transmission, rechargeable energy storage systems, cockpit electronics, engine control systems, on board charging modules
- Servers, supercomputing, video graphic array (VGA) cards, AI, GPU/CPU/Desktop, solid state drives (SSD)
- Switches, routers, base stations
- Tablets, gaming, notebooks, smartphones, action cameras & lighting
What happens to Phase Change Materials after Shelf Life?
Past the shelf life, the most readily observed response is precut pads (kiss-cut) tend to stick to each other and customers may have difficulty peeling out one without damaging adjacent one. There will be some viscosity change that may or may not affect thermal performance and we will not test or recertify material. We will not be liable for product quality or performance if expired parts are used in manufacturing.
What is the potlife of the PTM7XXX-SP?
Potlife (also referred to as work life) refers to the amount of time the material can be still be used after it has been opened. When kept in the 1kg cans, the potlife is 12 hours from the time the can is opened. When the lid is replaced and the can is closed again, you will have 48 hours to use the balance of the material. The remaining material should also be remixed (or re-rolled on a jar roller) prior to use.
Similarly, in the 280cc cartridge, the potlife is 24hrs if dispensed from the cartridge directly. If the cartridge is opened to add material to the printer and then closed again, the balance of the material should be used within 24-36 hours.
What is the thickness before and after the PTM7XXX-SP paste drying?
It is typical to lose approx. 20% thickness due to solvent drying. For example, a 300µm (0.3mm) thickness stencil of wet PTM7XXX-SP will result in 240µm (0.24mm) after drying. If the thickness loss is more than 20%, then the can was not stirred or rolled and it is indicative of mixing issues prior to dispensing them on the printing equipment.
What is the maximum operating temperature of the Phase Change Materials?
Though the maximum operating temperature for our Phase Change Materials is approximately 150°C. It is not recommended to operate continuously for long period of time above 125°C.
Why choose PCM over Thermal grease?
One can say that it comes down to preference, but it really doesn't. Phase change materials are hands down the best materials you can use as thermal interface IF the application parameters allow it. They are clean, efficient,can achieve the thinnest bondlines out of any other materials and are silicone free. Power cycling? Phase change can easily handle it while thermal grease can be pushed under the chip after a few hundred cycles.
Additionally they come into both paste (stencil print and dispence) and pad form (0.2~1mm thickness) and their Silicon free chemistry can achieve a bondline of 20~30μm making it the thinnest, cleanest and most reliable bondline in the market. Does this make thermal grease bad? Definitely not. Grease is great for all the other application types that PCM can't cover due to the temperature restrictions.
How should I clean Stencil printable PTM?
There are several ways to clean the stencils and printing tools while using PTM pastes or to clean heatsinks and modulus boards during rework. These solvents need to be carefully cleaned with a Non-woven antistatic microfibre (lint-free) cloth.
From "safe" options, the best solvents are IPA (isopropyl alcohol) and Isopar M (brand solvent containing small amounts of Naphtha). These are the most suitable for cleaning.
Naphtha and toluene are the best and most efficient solvents for removing phase change materials during reworking, but they have the downside of being carcinogenic and should be handled with care. You could also try Acetone and ethanol but they will not be as good as IPA and Naphtha.
Why are some properties a range?
Phase change materials come in thicknesses ranging from 0.2-1mm. Those are the initial values that are adjusted after you heat up (>45°C) and pressure the material. The installation pressure will determine the final thickness and thermal properties that those materials will keep throughout their lifetime. Thermal conductivity and bond line are directly affected by the installation pressure and no matter the stated properties, the final bondline is what is going to determine the material's thermal fate.
What are the differences between Pads and Pastes?
Phase change Pastes have the exact same chemistry as the phase change pads, with added solvent to make them printable. Stencil print is highly sought after for applications with high throughput such as IGBT screen printing.
Solvents can be adjusted so that the drying process is faster or slower, depending on your application requirements.
Should I use a silicone-based or silicone-free TIM?
There are pros and cons to using both a silicone-based or silicone-free Thermal Interface material. For more information on this, we have written a blog Silicone vs Silicone-free TIMs Advantages of Different Materials which discussed the properties of both materials on thermal management.
Learn More
Phase change materials (PCM) are often used as matrix materials for thermal interface applications, because they are solid at room temperature, and soften when heated (>45 °C). Those Silicone free chemistries rely on thermally conductive fillers such as ZnO, Aluminium and Alumina to achieve their thermal properties (Blog indepth discussion: Silicone vs Silicone-free TIMs Advantages of Different Materials) . Phase change material (PCM) are provided both in pad and paste forms. Pastes are exactly the same as pad versions with additional amount of solvents that make them screen or stencial printable and ideal for automatic production processes.
Thanks to the viscosity drop while increasing the temperature (>45°C) and optimal surface wetting property, the PCM could spread and fully fill the small gaps between contact surfaces, therefore provding a thin bondlines, even 20-30μm. PCM are designed to minimize thermal resistance at interfaces and maintain stable performance through the rigorous reliability tests required for long product life applications.
Their nature doesn't work for high operating temperature applications above 150°C but if the temperatures allow, it is a much better alternative for thermal grease since they are not prone to pump or dry out and are not "messy" at all. They definitely tick the boxes for conformable and reliable.
Compared to other type of TIMs (thermal interface materials) such as silicone grease, PCM have longer molecular chains with high molecular weight and surface tension ensuring a robust polymer structure and a stable filler-polymer matrix to avoid filler migration and separation. The H steric hindrance provides a rigid structure that ensures low filler migration and separation that at the same time limits the material mobility and pump out.
On the other hand, the tried and proven thermal grease has good flowability and low contact resistance but its short chains and Si-O-Si structures create a less rigid structure that has potential for migration, dry out and pump out issues.
To sum up, phase change materials exhibit the following characteristics:
- Optimal surface wetting
- Low contanct resistance
- Low thermal impedance
- Stable thermal impedance across reliability tests
- No bleed out, pump out and flow out
For the details of application, please check the Phase Change Material Application Notes. Content Table:
- Storage and transportation guidelines
- Step 0 - Jar rolling process and pot life
- Step 1 - Paste stencil printing procedure
- Step 2 - Solvent drying schedule
- Step 3 - PCM assembly steps
- Step 4 - Phase change results
- Results Analysis - BLT and thermal impedance curves
- Rework and cleanning guidelines
The phase change temperature is a critical characteristic of phase change materials. It refers to the specific temperature at which the material undergoes a phase transition. For Honeywell Phase Change Materials, the average phase change temperature is around 45 °C. This temperature is a result of the composition of polymeric paraffin waxes within the materials and is considered the average for the phase transition.
The actual/accurate Phase Change Temperature however is routinely assessed for each batch using Differential Scanning Calorimetry (DSC) at peak temperature (see highlighted DSC at the attached sample certificate of analysis), and it is ideally range between 37.5 °C and 52.5 °C to meet acceptable standards. Therefore, we recommend conducting the assembly at temperatures exceeding 60 °C to guarantee the material undergoes the desired phase change.
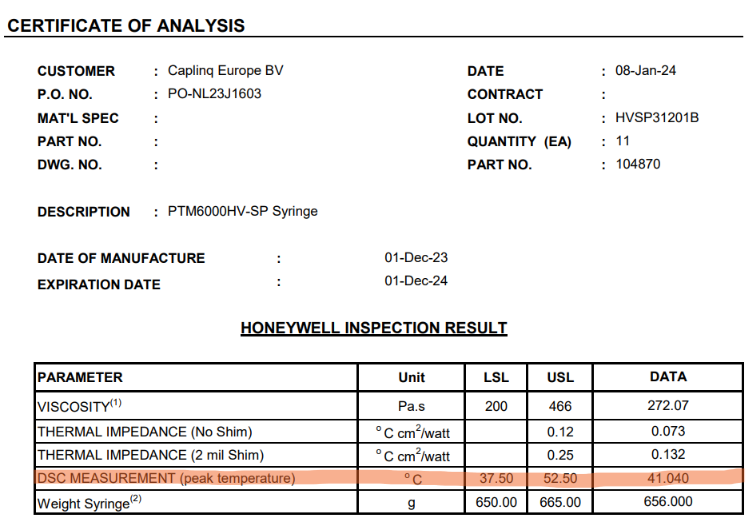
Phase Change Material Application Notes
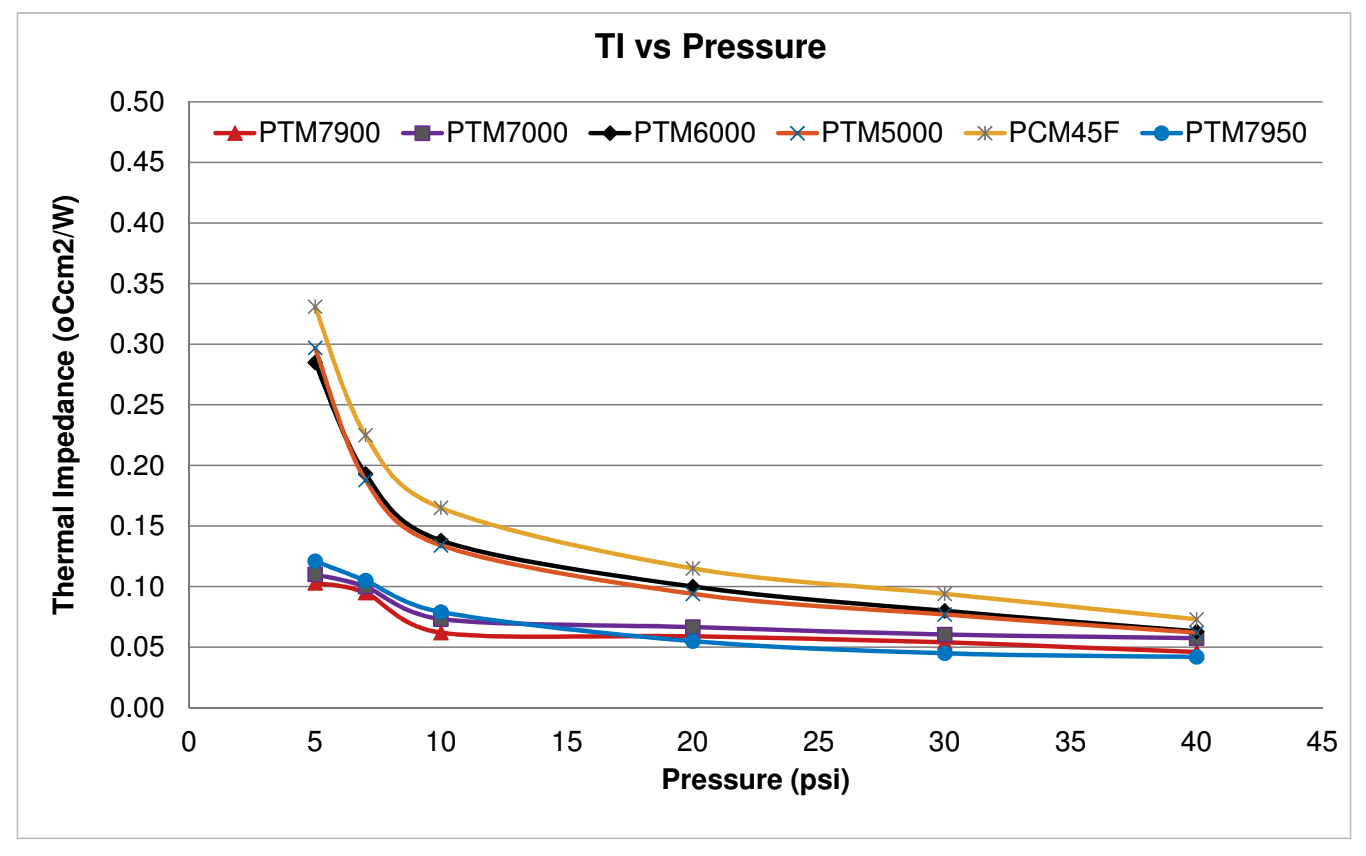
PCM Paste Stencil Printing Process (SP)
Stencil printable Phase change materials require the following steps for a successful application:
- Stencil print. “SP” or “SPS” versions of Phase Change Materials contain solvents which allow the paste to be stencil printed.
- Dry. Stencil-print Phase Change Materials require a drying step to remove the solvent prior to application. This drying time depends on the selected temperature.
- Apply Pressure. Phase Change Materials require pressure to reduce the thermal impedance. A minimum pressure of 70kPa (10psi) is required and must be applied after the drying phase and during assembly.
Step 0 - Storage & Jar Rolling
PCM paste does not need to be refrigerated at 5˚C, it needs to be stored at RT (room temperature) with the lid tightly sealed. If stored at 5 ˚C, it would need 4~5 hrs thawing and mixing at RT before it can be used. Otherwise, the bad homogenization could cause spreading problems. Its shelf life is 12 months at RT.
You should Jar-roll PCM paste jar for 30 minutes before use .After jar-rolling and just before printing, maintain thorough mixing of the SP material utilising a glass rod.
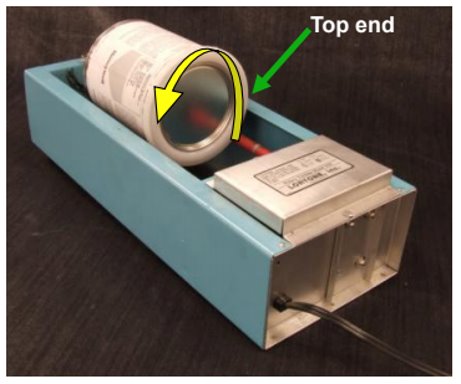
Step 1 - Stencil Printing
The basic printing guidelines can be borrowed from the SMT (Surface mounting Technology) processes of printing solder paste:
- The ideal aspect ratio should be greater than 1.5
- The ideal area ratio should be greater than 0.66
- PHASE CHANGE MATERIALS (PCM) WILL SHRINK 20% AFTER DRYING STEP
- Plan the print height to be 20% higher than the final dried height
For example, for a PCM print of 46 x 40 x 0.2mm
- Stencil Thickness should be 0.25mm (0.2mm/80% = 0.25mm)
- Aspect Ratio = 40 / 0.2 = 200 (OK)
- Area Ratio = (46 x 40)/ (2 x (46+40) x 0.25) = 1840/43 = 42.8 (OK)
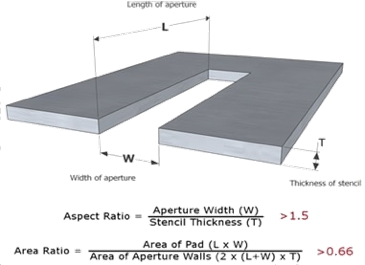
Step 2 - Solvent Drying
Approximate recommended drying times for PTM-Series Stencil Print (SP) type Phase Change Material (based on 0.25mm – 0.3mm thickness):
- 15 hours @ 25°C
- 3.5 hours @ 50°C
- 20 mins @ 80°C
- 2-3 mins @ 100°C
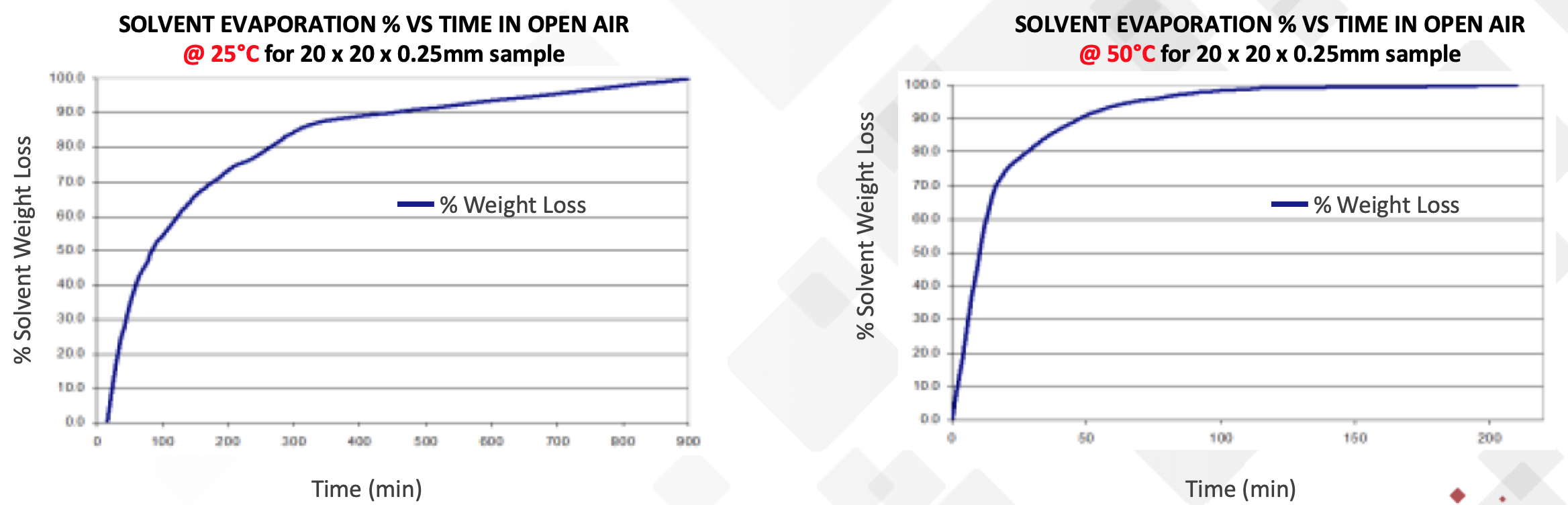
Please note that times are based on the part's temperature and are best measured using a thermocouple. As a pro tip, it is also possible to determine the time required based on the 20-22% height reduction of the Phase Change Material
Different types of Stencil Print materials will dry in different times and temperatures. We generally offer SP, SPM and SPS version. You can imagine them as Normal, Medium and Slow dry. In Room temperature, normal pastes dry pretty fast, at ~2.5 hours. Medium pastes can take up to two days while Slow versions can dry for more than two days... Of course this changes into minutes at 100°C. At 100°C, Normal ones take ~2.5minutes, Medium ones ~7 minutes and Slow ones can take more than 10 minutes to dry.
Thickness Shrinkage
All of our PCM materials come in both Pad and Paste versions (SP). The SP versions are identical to the pads, with the main difference being the added solvent that makes them more viscous. With this form come a couple of questions, first one being, "How much does the solvent shrink and how does this affect the final bondline thickness?".
To answer this we printed in a few different target thicknesses, namely 0.2mm, 0.25mm and 0.3mm. Then we put these samples in the oven for 20 minutes at 80°C for the solvent to dry and measured the outcome. From the resulting thicknesses, we concluded that, regardless of the print thickness, the dry version is ±20% thinner than the thickness right after print. So, for example, to get a 0.25mm final (dry) bondline we need a 0.3mm initial thickness.
Sample # | Thickness right after print (mm) | Thickness after Solvent dry (mm) | Height reduction |
1 | 0.299 | 0.239 | 20.07% |
2 | 0.247 | 0.195 | 21.05% |
3 | 0.194 | 0.154 | 20.62% |
Step 3 - Mounting and Assembly
Phase Change Materials require pressure for the lowest possible Thermal Impedance. Some application parameters that we should take into account are the following:
- We require clamp pressure of at least 10 psi (70 kPa) to compress the PCM and achieve the lowest thermal impedance and thus the best thermal performance.
The modules with printed and dried PCM layers can be mounted to the heatsink after it has been soldered or pressed in. Spring loaded screws to the heatsink can be fastened and tightened in a single step.
The PCM is solid at room temperature. Screws can be tightened immediately without any relaxation time. - PCM is not compressible at room temperature, but gel like above 45°C and thins down with temperature and pressure increasing.
To achieve the lowest thermal impedance and thus the best thermal performance, check the pressure and thermal impedance curve below. - Once the module has been mounted, the system should be heated up while leaving enough time for PCM to melt.
Be sure the material sees at least 60°C (about 15°C above transition temperature of 45°C ) for at least 30 mins after installation.
Phase change materials will melt, spread, fill gaps and provide an optimal thermal connection between module and heatsink. Spring loaded screws ensure that pressure is sustained.
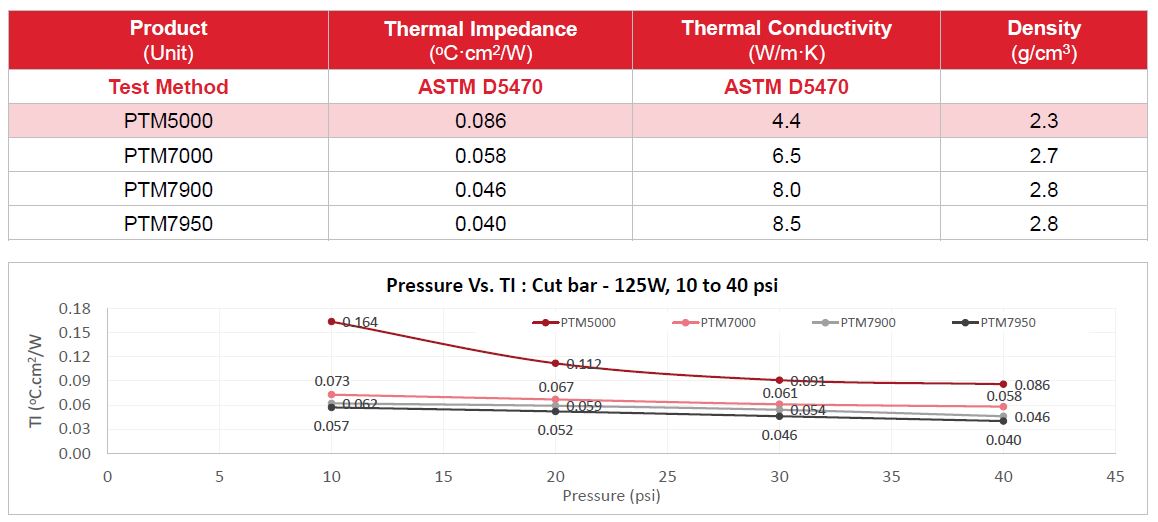
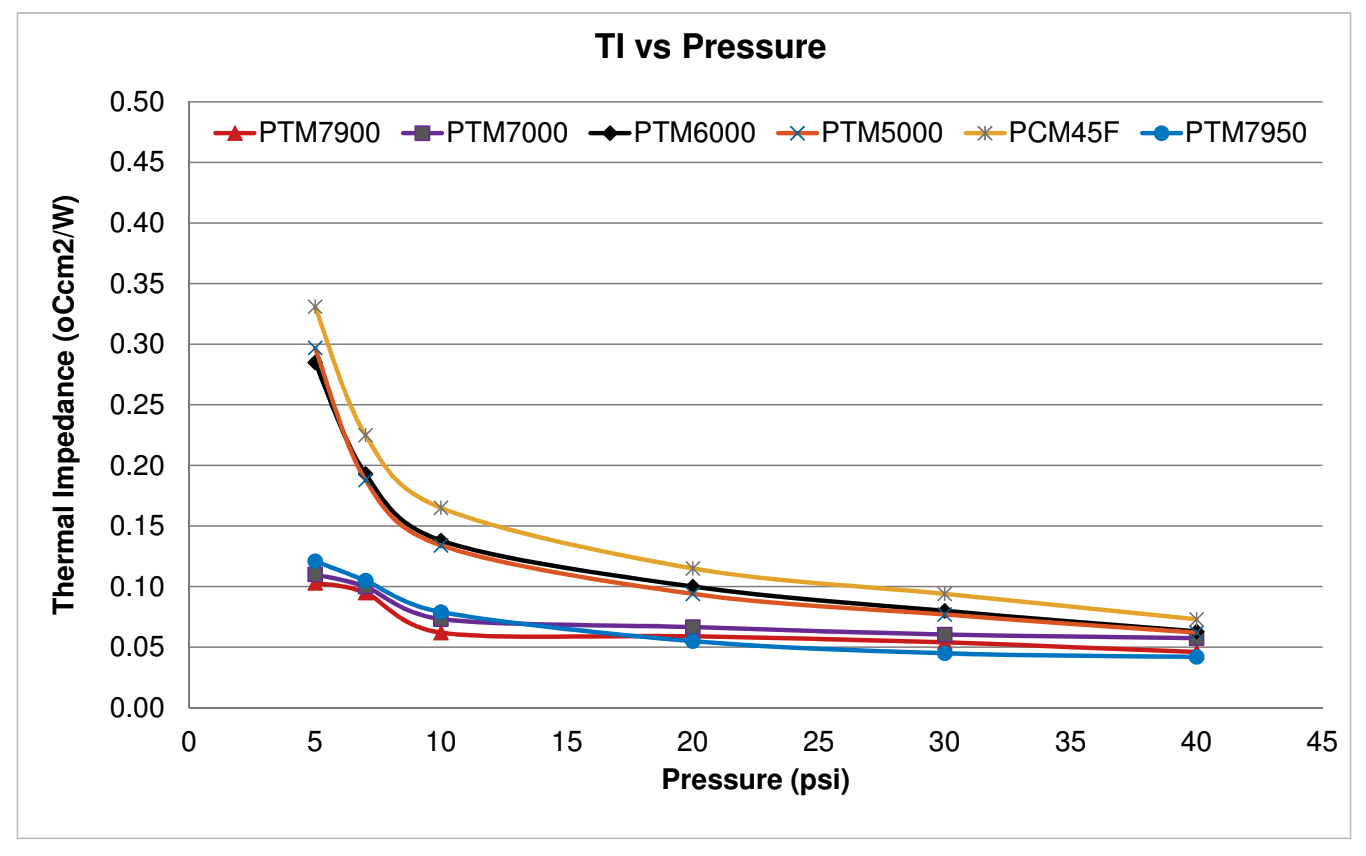
Size change
Typically, most customers use an initial pad size that is 70-80% of the target area to accommodate this spread, when the initial thickness is 0.2mm. You will have to determine the ideal size for your application in a way that fits the equipment in your assembly line.
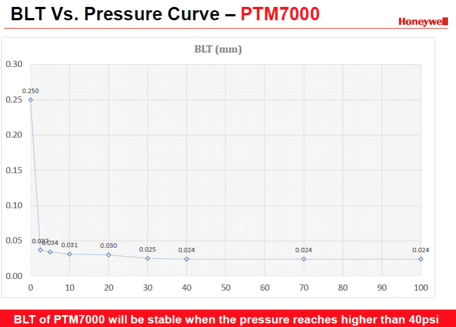
Final Bondline thickness