PTM 7950 | Phase Change Pad
- 0.04 Thermal Impedance
- 8.5 Thermal Conductivity
- Pad Form
Product Description
PTM7950 is a super highly thermally conductive Phase Change Material (PCM). It is designed to minimize thermal resistance at interfaces, maintain excellent performance through reliability testing, and provide scalable application at a competitive cost. Based on a novel polymer PCM system, PTM7950 exhibits excellent interface wettability during typical operating temperature ranges, resulting in extremely low surface contact resistance. Since PTM7950 comes only in 0.25mm and 0.2mm (thicker versions are under development) you need to be sure that this thickness is compatible and suitable for the flatness of your package.
Available Versions: (Check the difference between pad and paste versions)
- PTM7950 Pad | Easy application and no drying steps
- PTM7950-SP | Paste version for automatic stencil printing
- PTM7950-SPS | Paste version with slow-drying solvent
PTM 7950 cannot come in pad form on a reel. This is because the material is too soft and tends to wrinkle when rolled, especially when the size gets larger.
Key Features:
- Super low thermal impedance (TI vs Pressure Curve PTM7950)
- Silicone-free, no pump out, bleed out, dry out issues
- Industry-proven superior long-term reliability (Reliability Report PTM7950)
- Min BLT~20um, typical BLT is below 50um (BLT vs Pressure Curve PTM7950)
- 30~40 psi pressure is needed for usage (PCM Application Note)
Highly Recommended For:
- Power modules/inverters in automotive and power applications
- High-performance IT/enterprise computing devices
- Consumer electronics, high-performance IC
- High power LED
PTM7900 and PTM7950 are closely related thermal interface materials with slight differences in performance. PTM7950 features a softer composition, higher thermal conductivity, and lower thermal impedance, enhancing its overall thermal performance. Aside from these improvements, both materials share similar characteristics.
Learn More about PTM7950's superior thermal performance and long-term reliability.
Technical Specifications
General Properties | |
Specific Gravity Specific Gravity Specific gravity (SG) is the ratio of the density of a substance to the density of a reference substance; equivalently, it is the ratio of the mass of a substance to the mass of a reference substance for the same given volume. For liquids, the reference substance is almost always water (1), while for gases, it is air (1.18) at room temperature. Specific gravity is unitless. | 2.8 |
Thickness range | 0.25 mm |
Electrical Properties | |
Dielectric Strength Dielectric Strength Dielectric strength is measured in kV per mm and is calculated by the Breakdown voltage divided by the thickness of the tested material. Those two properties go hand in hand and while Breakdown voltage is always thickness dependent, dielectric strength is a general material property. As an example, the dielectric strength of Polyimide is 236 kV/mm. If we place 1mm of Polyimide between two electrodes, it will act as an insulator until the voltage between the electrodes reaches 236 kV. At this point it will start acting as a good conductor, causing sparks, potential punctures and current flow. | 0.55 kV/mm |
Volume Resistivity Volume Resistivity Volume resistivity, also called volume resistance, bulk resistance or bulk resistivity is a thickness dependent measurement of the resistivity of a material perpendicular to the plane of the surface. | 2.1x1014 Ohms⋅cm |
Thermal Properties | |
Specific Heat Capacity Specific Heat Capacity Specific heat capacity is the amount of heat energy required to raise the temperature of a substance per unit of mass. The specific heat capacity of a material is a physical property. It is also an example of an extensive property since its value is proportional to the size of the system being examined. | 0.97 J/g.K J/(g⋅°C) |
Thermal Conductivity Thermal Conductivity Thermal conductivity describes the ability of a material to conduct heat. It is required by power packages in order to dissipate heat and maintain stable electrical performance. Thermal conductivity units are [W/(m K)] in the SI system and [Btu/(hr ft °F)] in the Imperial system. | 8.5 W/m.K |
Thermal Impedance | 0.04 °C·cm²/W |
Additional Information
Honeywell PTM7950 is one of the most successful TIM products used in high power inverters and high performance computing devices. Ultra-low thermal impedance with minimum achievable BLT and superior long-term reliability make PTM7950 stand out from the competitors. PTM7XXX series also presents stability among vertical applications and pass automotive standard vibration test (Check the Vibration & Shock Test Report), thus PTM7XXX is currently widely used in automotive applications such as power inverters. These silicon-free pads are carbon hybrid based, so any potential outgassing will be from carbon hybrid materials. If high voltage is key to your application then we suggest evaluating thermal gap pads or insulation pads.
What are the reliability expectations of the PTM7950?
All the 7XXXseries (PTM7000, PTM7900 & PTM7950) pass the three major reliability tests with flying colours. Honeywell does not test beyond 1000 cycles, 92 hrs HAST and 1000 hrs HTS. However, anecdotally, some automotive customers have taken 7900 to beyond Honeywell’s limits and have found it to pass shock and vibration, longer temperature cycling and longer temperature and humidity soak. (Check Reliability Report PTM7950)
If your lifetime performance is defined mainly by power cycling, then you also check the PTM6000 series which will have the longest life. The main difference between the 7XXX products is the filler content which makes PTM7950 the most conductive.
How to achieve the minimum thermal resistance of PTM7950?
To achieve as low thermal resistance as possible for your device, you choose the material with high thermal conductivity, minimize the bondline thickness, and also improve the surface wettability. PTM7950 excels at the thermal performance since it could achieve minimum bondline of 17um and high TC as 8.5 W/m.K. Clamping pressure (30~40 psi) and temperature (at least 30mins @ 60°C) are suggested to achieve a minimum bond line thickness of the phase change material, typically less than 1.5 mil (0.038mm) for best performance. The material must go through the phase change temperature to exhibit entitlement performance. (Check PCM Application Note) .
The figures below show the TI achieved using PTM7950.
PTM7950 Thermal Impedance (TI) vs. Pressure
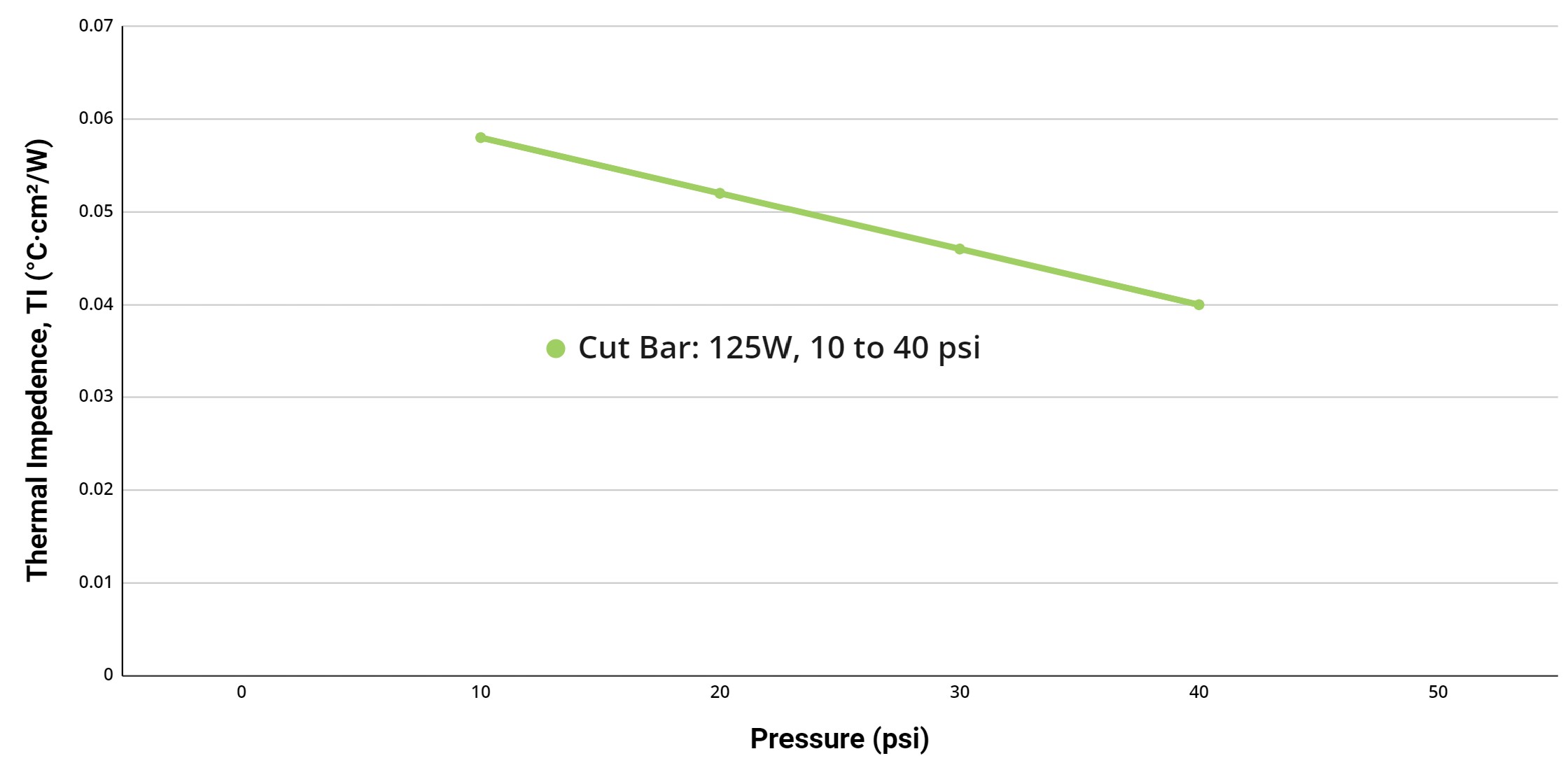
Thermal Impedance of PTM7950 is reduced with pressure
Thermal impedance is a measure of the resistance to heat flow across an interface. The higher the thermal impedance, the greater the resistance to heat flow and the lower the rate of heat transfer. This can lead to an increase in temperature at the interface, which can reduce the performance and lifespan of the components.
To increase heat transfer between two surfaces, you want to reduce the thermal impedance at the interface between those surfaces.
What is a Cutbar?
A "cutbar" is a metal bar made of copper or aluminum used to measure thermal performance, simulating heat generated by electronic components. It tests the thermal conductivity of thermal interface material by placing it between the cutbar and a cooling solution, and its performance is observed by measuring its ability to conduct heat away from the cutbar.
The 125W value is the heat dissipated during testing, used to determine thermal impedance.
Bondline thickness of PTM7950 is reduced with pressure
One key characteristic of the PTM7950 is its bondline thickness, which refers to the thickness of the layer of adhesive between two surfaces being bonded. In the image to the left, we can observe how the bondline thickness of the PTM7950 changes under varying pressure conditions.
As the pressure applied to the PTM7950 increases, the bondline thickness decreases. Specifically, a minimum pressure of 10 psi is needed to observe a significant reduction in bondline thickness. This means that lower pressure is sufficient to achieve a thinner bondline, which can be advantageous in certain applications. However, as pressure increases beyond 40 psi, the amount of thin bondline thickness that can be obtained becomes very small. This suggests that higher pressure levels may not result in significantly thinner bondlines and could even be detrimental to the bonding process.
Understanding the relationship between pressure and bondline thickness can be crucial in optimizing the use of the PTM7950 adhesive in different applications. By selecting the appropriate pressure level, it may be possible to achieve the desired bondline thickness, thereby ensuring a strong and reliable bond between surfaces. Furthermore, the pressure level could be adjusted based on the specific application and the materials being bonded, which could further improve the quality and durability of the bond.
PTM7950 Bond Line Thickness, BLT (mm) vs. Pressure (psi)
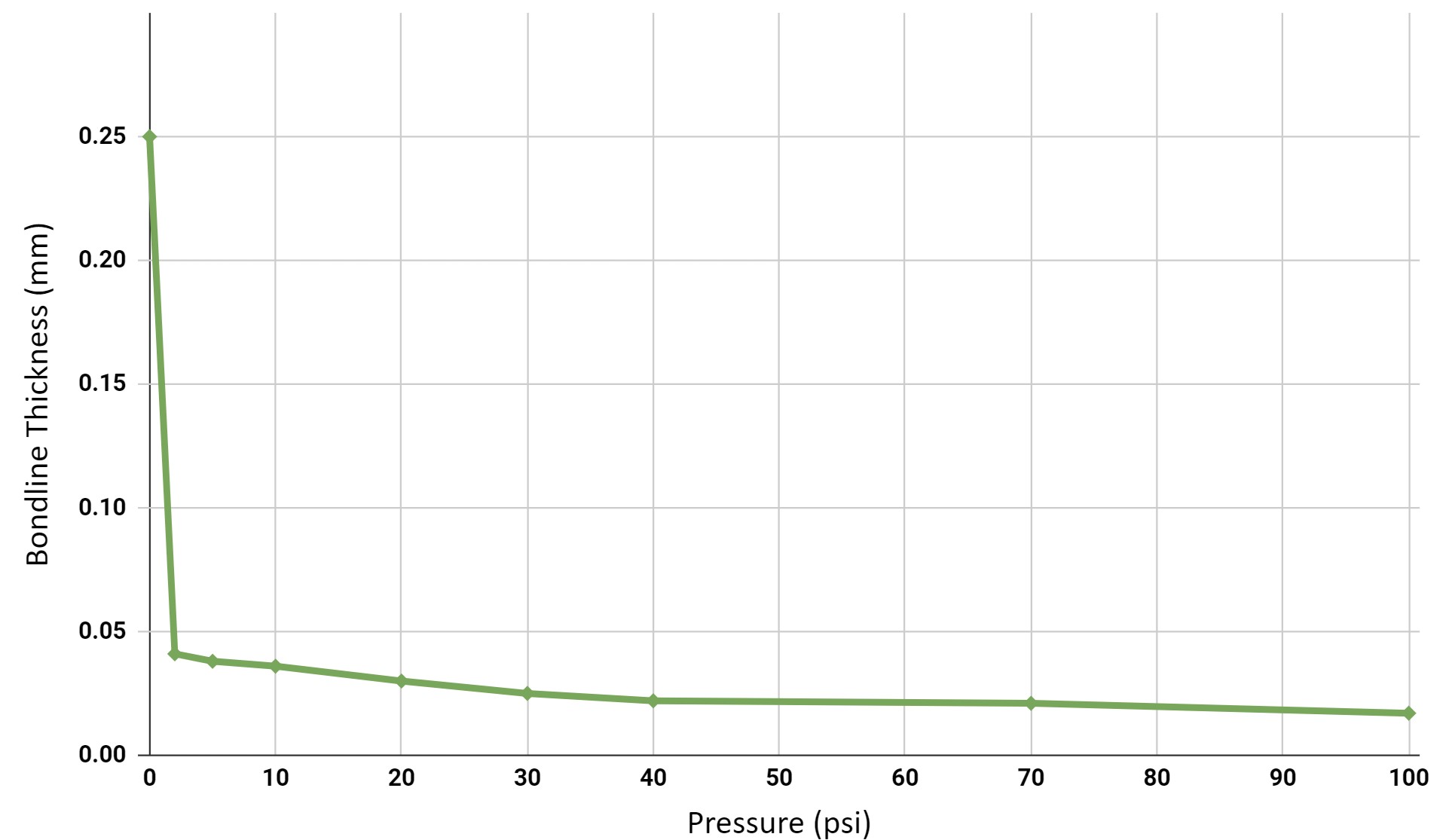
Thermal Impedance Comparison of PTM7000-series against competitors
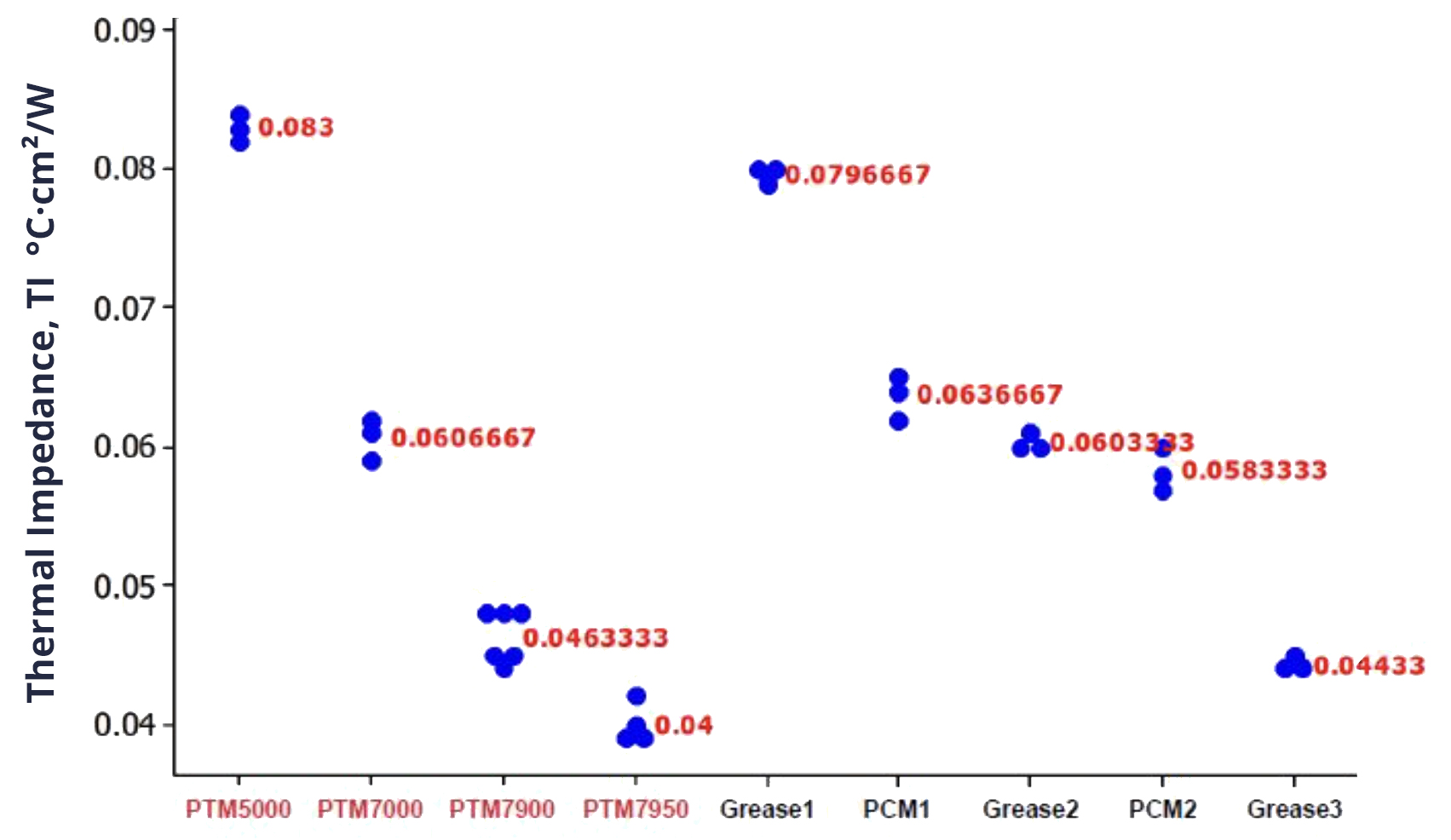
PTM7950 is best-in-class against the competition
The thermal impedance values for various materials are shown in the chart on the left, including the PTM 7900 and PTM 7950. Interestingly, both of these materials have the lowest thermal impedance values when compared to all other materials tested, including competitive thermal greases. Overall, the PTM 7950 is the top performer among all materials tested for thermal impedance.
The PTM 7950 is clearly the best choice for thermal impedance, with the lowest value among all materials tested. This makes it an excellent option for electronic devices that require exceptional thermal management.
What is PTM7958?
We occasionally receive inquiries from customers about a material labeled PTM7958. This part number is often encountered by supply chain teams or engineers during material sourcing or product qualification.
To clarify, PTM7958 is a customer-specific part number assigned to a large consumer of our Phase Change Materials (PCMs). While the part number may differ, PTM7958 is functionally equivalent, if not identical, to our standard PTM7950.
Both materials share the same formulation, thermal performance profile, and reliability characteristics. The only difference lies in the labeling for internal traceability and logistical purposes.
CAPLINQ and Honeywell PTM7950 featured on Linus Tech Tips
If you haven't seen it already, be sure to check out Linus' Tech Tip video which discusses Honeywell PTM7950. Though it mentions that PTM7950 is hard to buy, we've reached out to Linus and his team and let them know that CAPLINQ was the only officially recognized market channel partner to Honeywell's Thermal Interface Material business. CAPLINQ's website is even featured in the video at timestamp 8:28, though we're pretty sure all the technical information Linus references come from our website as well.